This article focuses on the shot peening process of spiral bevel gears and its impact on the residual stress field. It first introduces the importance of spiral bevel gears in mechanical systems and the role of shot peening in improving gear performance. Then, it details the experimental and simulation methods used in the research, including the selection of test specimens, test parameters, and the establishment of simulation models. Through the comparison of simulation and experimental results, the accuracy of the model is verified. Subsequently, the influence laws of shot peening time, shot velocity, and shot diameter on the residual stress field are analyzed in depth. Finally, the research conclusions are summarized, and the application prospects of the research results are prospected.
1. Introduction
Spiral bevel gears play a crucial role in various mechanical transmission systems, especially in high-speed and heavy-duty working conditions. To enhance the fatigue life and service performance of gears, the shot peening process is commonly applied at the end of the manufacturing process. Shot peening induces residual compressive stress on the gear surface by impacting it with high-speed shots, which can effectively improve the contact fatigue strength, bending fatigue strength, and anti-scuffing ability of the gears.
However, in the actual production process, determining the optimal shot peening process parameters through experiments is time-consuming and labor-intensive. Therefore, conducting simulation research on the shot peening process has important practical significance. It can not only save a large amount of resources but also provide theoretical guidance for industrial manufacturing.
2. Experimental Procedure
2.1 Test Specimens
The test specimens are spiral bevel gears of a certain model made of AISI 9310 high-strength alloy steel. The tooth parts have undergone carburizing and quenching treatment. The tooth surface, which is the key area for shot peening, has a hardness higher than 60HRC within a depth of 0.56 mm from the surface.
2.2 Test Parameters
The experiment is carried out using an MP1000Ti CNC shot peening machine. The shot type is ASH110 (55 – 62HRC), the shot peening intensity is 0.178 – 0.228 mmA, the coverage is 200%, the nozzle angle is 17°, the air pressure is 0.25 MPa, the moving speed is 70 mm/min, and the shot peening time is 144 s. The tooth root, convex surface, and concave surface are strengthened separately. The nozzle is perpendicular to the target surface and the distance is 150 mm. The gear turntable rotates at a speed of 30 r/min, and the shot flow rate is 5 kg/min.
2.3 Residual Stress Measurement
The residual stress on the tooth surface is measured. The measuring points are located on the pitch cone line of the tooth surface, as shown in Figure 1. Points a, b, and c are the quarter points of the tooth width, with a being close to the large end of the tooth. To obtain the residual stress field on the gear surface layer, electrolytic polishing is performed on the tooth along the normal direction of the tooth surface, and the polishing depth is measured by a white light interferometer.
The X-ray diffractometer of Proto Company in Canada is used to measure the residual stress on the tooth surface. The tube voltage is 25 kV, the tube current is 5 mA, the X-ray tube is Cr_K – Alpha, the aperture diameter is 1 mm, the wavelength is 2.291 A, the exposure time is 3 s, the exposure times are 7, and the maximum β angle is 20°. The electrolytic polishing instrument is of type 8818 – V3, with a set voltage of 40 V, a flow rate of 8, a polishing time of 3 s, and a polishing current of 2.8 – 3 A.
Measuring Point | Location Description |
---|---|
a | Close to the large end of the tooth on the pitch cone line of the tooth surface |
b | On the pitch cone line of the tooth surface, the middle quarter point of the tooth width |
c | On the pitch cone line of the tooth surface, close to the small end of the tooth |
3. Simulation Model Establishment
3.1 Discrete Element Model
3.1.1 Model Building
The EDEM simulation software is used to set up the discrete element model to simulate the process of shots from the nozzle to the tooth surface. According to the process parameters in Section 2.2, the model parameters are set. The geometric model is shown in Figure 4. To extract the impact information of the target position on the tooth surface, the Hypermesh software is used to mesh the tooth surface. In the model, the tooth surface unit is imported as the gear model. The nozzles are set perpendicular to the tooth root, convex surface, and concave surface of the gear respectively, and the distance from the target surface is 150 mm, and they move along the tooth width direction. The initial velocity of the shots is determined by the empirical formula (1).
3.1.2 Data Extraction and Processing
The calculation results are exported by EDEM software. The impact points are judged by the unit number, and the impacts at the quarter points on the pitch cone line of the tooth surface are screened out for data processing.
- Impact Velocity Vector: Since the gear is a curved surface and the angle between each position and the shot beam is different, and the target plate in the finite element model is a local area on the tooth surface, the absolute velocity of the shots needs to be converted into the relative velocity between the tooth surface unit and the shots. The conversion method is based on the coordinate transformation principle, as shown in Figure 5.
- Impact Times: When the actual shot peening time is , the unit area impact times of the target position is calculated by formula (3).
3.2 Finite Element Model
3.2.1 Meshing and Boundary Conditions
Based on the ABAQUS/CAE commercial finite element software, a finite element model is established to calculate the residual stress field on the tooth surface after shot peening. The shot diameter is 0.3 mm, and the element type is C3D8R. The target plate size is shown in Figure 6. Except for the infinite element body mesh, the target plate size is 1 mm×1 mm×0.5 mm, and the element type is C3D8R. A predefined field is set in this area, and the measured value of the residual stress on the tooth surface before shot peening is used as the initial residual stress of the model. Region I is used to limit the impact center point position of the shots and extract the calculation results of the residual stress. Regions I and II are the refined parts of the mesh, and the element size is 10 μm×10 μm×10 μm. Region III is the transition area from fine to coarse of the finite element mesh. Region IV is of the infinite element body CIN3D8 type, which is used to eliminate the reflection of the stress wave at the boundary of the target plate. The bottom surface of the target plate is completely fixed in the model. The contact relationship between the shots and the target plate is Surface to Surface. The normal behavior is defined as “hard” contact, and the tangential behavior is defined as penalty friction with a friction coefficient of 0.2.
3.2.2 Material Model
The shots are set as elastoplastic bodies and adopt an isotropic constitutive model. The parameters of the shots are set as follows: Young’s modulus , Poisson’s ratio , density , and yield strength . The target body material is 9310 carburized and quenched steel. The material parameters are set as follows: Young’s modulus , Poisson’s ratio , density . The plastic stress – strain curve adopts the Johnson – Cook model, and its basic model is shown in formula (4) and (5). The parameters are obtained by Hopkinson pressure bar test, which are , , , , . To prevent stress wave oscillation, the damping of the target plate material is set as .
3.2.3 Shot Impact Information
The shot impact angle, velocity, and times are determined by the calculation results in Section 3.1.2. According to the size standard of ASH110 type shots, the shots are set as spherical with a diameter of 0.3 mm. Considering the random distribution of the shot impact position in the actual situation, the Python language is used for programming in the simulation, and the Random function is used to generate random positions. The shot impact center points are all within Region I shown in Figure 6.
4. Results and Discussion
4.1 Comparison of Simulation and Experimental Results
To verify the accuracy of the simulation model, the same process parameters as those in the experiment are set in the established shot peening process simulation model. Figure 7 shows the measured and simulated three-dimensional morphology of point b on the convex surface after shot peening. The measured value of the three-dimensional roughness is 0.35 μm, and the simulated calculation result is 0.386 μm with an error of 10.3%. The reason for the lower resolution of the simulation result in the x and y directions compared with the measured result is that the sampling interval of the measured data is 0.5 μm, while the target plate mesh size of the finite element model is 10 μm×10 μm.
The comparison of the residual stress values on the tooth surface along the tooth height direction after shot peening between the experiment and the simulation is shown in Table 1. The results show that the surface residual stress at each point of the tooth is between – 800 and – 880 MPa, and the calculation error is within 6%. Figure 8 shows the distribution of the measured and simulated residual stress along the depth direction at point b on the convex and concave surfaces. After shot peening, the change trends of the residual stress on the convex and concave surfaces of the tooth are the same, and the residual compressive stress value on the concave surface is slightly larger than that on the convex surface. The distribution of the residual stress in the tooth width direction and the tooth height direction is similar. The surface residual stress is about – 800 to – 850 MPa, the maximum residual compressive stress value is between 1200 and 1300 MPa, and the depth is about 20 to 30 μm. The statistics of the surface residual compressive stress and the maximum residual compressive stress value of the tooth are shown in Table 2. The errors between the measured values and the simulation results are all less than 10%, which proves that the simulation model can accurately predict the residual stress field on the tooth surface layer of the spiral bevel gear after shot peening.
Project | Convex Surface Measuring Point | Concave Surface Measuring Point | ||||
---|---|---|---|---|---|---|
a | b | c | a | b | c | |
Experimental Value/MPa | -818.3 | -805.3 | -814.2 | -879.1 | -849.7 | -836.7 |
Simulation Value/MPa | -823.4 | -824.2 | -834.6 | -843.1 | -837.9 | -831.3 |
Error/% | 0.6 | 2.3 | 2.5 | 4.1 | 1.4 | 0.6 |
4.2 Influence of Shot Peening Time
The shot peening coverage is affected by the shot flow rate and shot peening time. The increase in the shot flow rate and shot peening time will increase the shot impact times and the shot peening coverage. This paper mainly studies the influence of shot peening time on the residual stress field. The results are shown in Figure 9. Based on the method of Miao et al. [9], the shot peening coverage is calculated.
When the initial velocity of the shots is 40 m/s, when the shot peening time reaches 72 s, the shot impact times is 360 per/mm², and the shot peening coverage reaches 98%, that is, full coverage. When the shot peening time is 144 s, the coverage is 200%. With the increase of shot peening time: (1) The residual compressive stress on the target plate surface increases and gradually stabilizes at about 800 MPa after the shot peening time reaches 72 s; (2) The residual compressive stress at 10 μm shows a gradually increasing trend and stabilizes at about 1000 MPa after the shot peening time reaches 96 s; (3) The residual compressive stress at 20 μm continues to increase. After 72 s, the residual compressive stress at 20 μm is higher than that at 10 μm, indicating that the maximum residual compressive stress depth increases from 10 μm to 20 μm. This shows that increasing the shot peening time can effectively increase the residual compressive stress value in the subsurface layer of the material and increase the depth of the maximum residual compressive stress layer.
4.3 Influence of Shot Velocity
The initial velocity of the shots is determined by the nozzle air pressure, shot flow rate, and shot diameter. The nozzle air pressure is the main factor. The increase in the nozzle air pressure will significantly increase the shot velocity and the shot peening intensity.
Referring to the test shot velocity range of Nordin et al. [21], the initial velocity of the shots is set. The calculation results of the residual stress are shown in Figure 10, and the cloud diagram is shown in Figure 11. The results show that when the shot velocity increases from 30 m/s to 40 m/s and 50 m/s, the residual compressive stress induced by shot peening increases. The change in the surface residual compressive stress value is small. The maximum residual compressive stress values are – 1104.7 MPa, – 1144.9 MPa, and – 1167.3 MPa respectively, and the maximum residual compressive stress depths are 20 μm, 25 μm, and 30 μm respectively. The results show that with the increase of the shot velocity, the change in the surface residual compressive stress value of the target plate is not significant, but the maximum residual compressive stress value and the maximum residual compressive stress depth will continue to increase.
4.4 Influence of Shot Diameter
The residual stress fields under the impact of different shot diameters are calculated as shown in Figures 12 and 13. The shot diameters are set according to the SAE standard, and ASH70, ASH110, and ASH170 types of shots are used. Table 3 shows the corresponding relationship between each type of shot and its diameter. The results show that when the shot diameter increases, the surface residual stress value changes slightly, but the maximum residual compressive stress value and the maximum residual compressive stress depth will be significantly increased. When the shot diameter increases from 0.18 mm to 0.30 mm and 0.42 mm, the surface residual compressive stress is between – 760 and – 840 MPa. The maximum residual compressive stress value increases from – 893.6 MPa to – 1145.0 MPa and – 1251.5 MPa, and the maximum residual compressive stress depth increases from 10 μm to 30 μm and 40 μm. However, the increase in the shot diameter will increase the surface roughness of the gear. The reason is that when the shot diameter is larger, the kinetic energy of the shots increases. When impacting the tooth surface, the plastic strain of the material increases, thus increasing the crater radius and significantly increasing the surface roughness of the gear.
Project | ASH70 | ASH110 | ASH170 |
---|---|---|---|
Diameter/mm | 0.18 | 0.30 | 0.42 |
-766.3 | -838.7 | -773.0 | |
-893.6 | -1145.0 | -1251.5 | |
10 | 30 | 40 |
5. Conclusions
In this paper, a simulation calculation model of the residual stress field of the shot peening process of AISI 9310 steel spiral bevel gears is established based on the coupling method of discrete element and finite element, and the correlation laws between the shot peening process parameters and the residual compressive stress on the tooth surface after shot peening are explored.
- The prediction error of the established simulation model for the residual stress field on the tooth surface is within 10%, and the calculation result is accurate.
- When the shot peening time is 72 s, the shot impact number reaches 360 per/mm², and the target plate coverage reaches full coverage. When the shot peening time continues to increase, the surface compressive stress of the target plate gradually stabilizes at about – 800 MPa.
- The shot peening process mainly affects the residual stress field within a depth of 50 μm from the tooth surface. When the depth is greater than 50 μm, the residual stress field is determined by the process before shot peening.
- When the shot peening coverage is 200%, the changes in the shot diameter and velocity have little influence on the surface residual compressive stress of the parts used in this paper.
- When the initial velocity and diameter of the shots increase, the change in the surface residual compressive stress value of the target plate is small, but the maximum residual compressive stress value and the maximum residual compressive stress depth on the surface layer of the target plate are significantly increased. The maximum residual compressive stress value can be increased to – 1251.5 MPa, and the maximum residual compressive stress depth can be increased to 40 μm.
- The research results of this paper have important guiding significance for the optimization of the shot peening process parameters of spiral bevel gears. By accurately predicting the residual stress field under different process parameters, manufacturers can select the most suitable process parameters to improve the fatigue life and service performance of gears, thereby reducing production costs and improving product quality.
- In future research, we can further explore the influence of other factors on the shot peening process, such as the material properties of the shots and the gear, the shape and distribution of the shots, and the influence of different nozzle designs. In addition, we can also combine the shot peening process with other surface treatment technologies to explore more effective methods to improve the performance of spiral bevel gears.
- In conclusion, the shot peening process is an important method to improve the performance of spiral bevel gears. Through continuous research and optimization of the process parameters, we can better play its role and promote the development of the mechanical manufacturing industry.
- Furthermore, with the development of advanced manufacturing technology and materials science, new materials and manufacturing processes for spiral bevel gears may emerge. It is necessary to continuously update and improve the simulation model to adapt to these changes. For example, the application of new alloy materials with higher strength and better wear resistance may require adjusting the shot peening parameters to achieve the best surface strengthening effect.
- Moreover, the research on the shot peening process can also be extended to other mechanical components with similar working conditions and performance requirements. By sharing and applying the research results in different fields, we can promote the overall progress of the manufacturing industry.
- In the future, we can also use more advanced experimental techniques and measurement methods to obtain more accurate data on the residual stress field and surface topography. These data can be used to further verify and improve the simulation model, making it more reliable and practical.
- In addition, considering the environmental impact and energy consumption of the shot peening process, we can explore more environmentally friendly and energy-efficient shot peening methods. For example, optimizing the shot recycling system to reduce waste and energy consumption during the process.
- Overall, the research on the shot peening process of spiral bevel gears has broad prospects and potential for development. Through continuous efforts in research and innovation, we can continuously improve the performance and quality of mechanical products and contribute to the development of modern manufacturing.
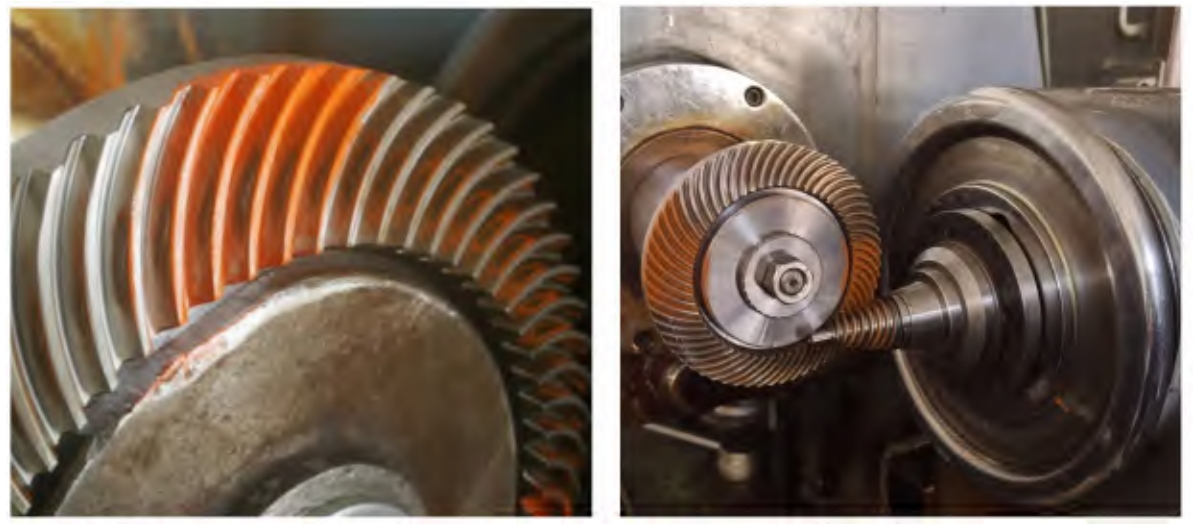