Abstract
In the contact process of transmitting power in a helical gear transmission system under oil lubrication, the tooth surface will stall after collision, triggering the phenomenon of “surge,” which is one of the forms of functional failure of the equipment. The occurrence of “surge” increases the wear rate of gears, reducing their service life. Furthermore, frequent “surge” caused by alternating stress may lead to fatigue damage to gear materials, or even cracks or fractures, significantly impacting the smooth operation and reliability of the equipment. Given the lack of clarity regarding the “surge” mechanism, stall and vibration characteristics caused by “surge,” and control strategies to suppress it, coupled with the scarcity of mature and unified analytical methods for gear transmission system “surge,” there is an urgent need for an accurate and in-depth analysis of the “surge” phenomenon in helical gear transmission systems. This paper establishes a “surge” model for helical gear and, through coupling with a dynamic model, derives specific parameters for the occurrence and development of “surge.” Based on these parameters, control strategies to inhibit “surge” are proposed. The specific contents include: (1) To deeply explore the dynamic behavior of helical gear considering “surge” and the specific parameters affecting it, a meshing impact and lubricant interface slip model is established. By analyzing the change rule of gear speed, lubricant speed, and lubricant flow rate under the consideration of interface slip and meshing impact, the oil film speed under “surge” is derived. Relevant equations are derived and corrected through the change of suction speed and reflux coefficient, establishing a mathematical model of helical gear “surge” which is then compared and verified. (2) The transmission error and time-varying meshing stiffness of helical gear is analyzed to establish a helical gear pair dynamic model considering meshing impact, transmission error, and integrated stiffness. The helical gear “surge” model is coupled with the dynamic model through integrated stiffness and gear speed after the impact. The dynamic characteristics of the helical gear are analyzed in the case of the “surge” effect, and the nonlinear characteristics of the helical gear considering “surge” are analyzed by the excitation frequency and error amplitude. (3) The effect of “surge” on the smoothness and vibration of the gear transmission system is analyzed, showing that “surge” has a greater impact on the vibration of helical gear in the torsional direction, with vibration speed and displacement significantly larger than in the other three directions. The transformation process from a stable motion state to “surge” and back to a stable state is studied, and control strategies to reduce “surge” are proposed. (4) Based on the coupled model of “surge”-dynamics, the influence of rotational speed, torque, load, lubricating oil parameters, and other factors on the “surge” of helical gears is analyzed, theoretically revealing the correlation mechanism between these parameters and “surge,” which provides a theoretical basis for the research on the “surge” suppression strategy of helical gear.
1. Introduction
1.1 Research Background and Significance
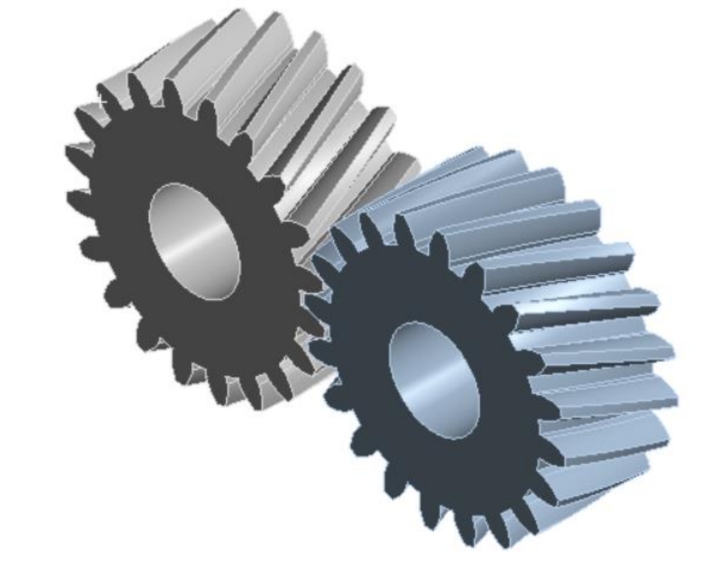
Helical gear is widely used in various mechanical devices due to their advantages such as high contact ratio, smooth transmission, and low noise. However, in high-speed and heavy-load operating conditions, helical gear may experience “surge” during the transmission process, leading to issues such as increased wear, vibration, and noise, and ultimately affecting the smooth operation and reliability of the equipment. Therefore, it is crucial to conduct in-depth research on the “surge” mechanism of helical gear and propose effective suppression strategies.
1.2 Research Status
The current research on gear “surge” is relatively limited, and there is a lack of mature and unified analytical methods. However, relevant research on gear dynamics, elastohydrodynamic lubrication (EHL), and gear transmission errors provides a theoretical basis for studying gear “surge.”
1.2.1 Elastohydrodynamic Lubrication Research
Elastohydrodynamic lubrication theory combines Hertz’s theory of elastic contact with Reynolds’ fluid theory. Dowson and Higginson proposed a general formula for the minimum oil film thickness for point contact gears. Subsequent research has further explored the influence of various factors such as gear geometry, operating conditions, and material properties on EHL characteristics.
Author | Year | Research Focus |
---|---|---|
Reynolds | 1886 | Derivation of Reynolds equation |
Dowson & Higginson | 1959 | General formula for minimum oil film thickness |
Zuo Mingyu | 2022 | EHL of asymmetric polymer gears |
Zhang Yuhao | 2022 | Thermal EHL characteristics of herringbone gears |
Xu Chunhui | 2022 | EHL characteristics of gears based on the multi-grid method |
1.2.2 Gear Transmission System Dynamics Research
Gear dynamics research focuses on the vibration and transmission smoothness of gear systems, which directly affect the performance, reliability, and life of mechanical systems. Existing research has analyzed the vibration and dynamic characteristics of gear systems under various conditions, providing a basis for studying gear “surge.”
Author | Year | Research Focus |
---|---|---|
Xiao et al. | 2024 | Dynamic characteristics of gear-shaft-bearing-housing systems |
Tan et al. | 2024 | Dynamic characteristics of profile-shifted planetary gears |
Dong Wanfu | 2023 | Stiffness calculation and dynamics of modified spur gears |
Zhang et al. | 2024 | Dynamics of wind turbine gear pairs considering lubrication |
1.3 Research Content and Methodology
This paper aims to establish a “surge” model for helical gear and analyze its dynamic characteristics by coupling it with a dynamic model. The influence of various parameters on “surge” is investigated, and suppression strategies are proposed. The main research contents include:
- Establishment of Helical Gear “Surge” Model: Analyze the “surge” mechanism of helical gear and establish a meshing impact and lubricant interface slip model. Derive the oil film speed under “surge” and establish a mathematical model.
- Dynamic Analysis of Helical Gear “Surge”: Establish a dynamic model considering transmission error and time-varying meshing stiffness. Couple the “surge” model with the dynamic model and analyze the dynamic characteristics of the helical gear under the “surge” effect.
- Influence Analysis of Parameters on “Surge”: Analyze the influence of parameters such as rotational speed, torque, load, and lubricating oil parameters on “surge” and propose suppression strategies.
The technical route of this paper is shown in Figure 1-1.
Figure 1-1 Technical Route
plaintext复制代码+-----------------------------------------------------+ | Research Background | +-----------------------------------------------------+ | v +-----------------------------------------------------+ | Establishment of Helical Gear "Surge" Model | +-----------------------------------------------------+ | v +-----------------------------------------------------+ | Dynamic Analysis of Helical Gear "Surge" | +-----------------------------------------------------+ | v +-----------------------------------------------------+ | Influence Analysis of Parameters on "Surge" and | | Suppression Strategy Proposal | +-----------------------------------------------------+
2. Mechanism Analysis of Helical Gear “Surge” Considering Solid-Liquid Interface Slippage
2.1 “Surge” Mechanism of Helical Gear
“Surge” generally occurs in gas turbines such as compressors and centrifugal compressors, manifesting as sudden flow changes and oscillations. Similarly, “surge” can also occur in gear transmission systems due to factors such as manufacturing and installation errors, surface micro-topography, oil supply, and collisions.
2.1.1 Meshing Impact Calculation
When two gears mesh, the relative velocity between them can cause an impact force at the meshing point. This impact force leads to a sudden increase in the convolution speed and a mutation in the theoretical oil film thickness.
Figure 2-1 Schematic Diagram of Involute Gear Meshing Impact
plaintext复制代码Pb1 ------------------------ Pb2 / \ / \ / N1N2 \ / \ O1 -------------------------------------- O2
The position of the meshing impact point can be determined by solving equations (2.1) to (2.6). The impact force Ft and the speed of the gears after impact can be calculated using the slice method.
Equation | Description |
---|---|
(2.1) | Position of meshing impact point |
(2.2) | Relationship between angles |
(2.3) | Involute function |
(2.4) | Pressure angle relationship |
(2.5) | Total deformation |
(2.6) | Deformation angle |
(2.7) – (2.10) | Calculation of impact force |
(2.13) – (2.16) | Speed of gears after impact |
2.1.2 Lubricant Interface Slip Calculation
Under high-speed and heavy-load conditions, the shear stress at the solid-liquid interface may exceed a limit value, causing the lubricant to slip. The slip phenomenon affects the oil film thickness and pressure distribution.
Figure 2-2 Schematic Diagram of Slip State Velocity Distribution
plaintext复制代码u1' -------------------------- u2' / \ / \ / Contact Area \ / \ Gear 1 --------------------------------- Gear 2
The velocity distribution in each lubrication layer can be obtained by solving equation (2.19), and the volume flow rate in the x and y directions can be calculated using equation (2.20).
Equation | Description |
---|---|
(2.18) | Shear stress balance equation |
(2.19) | Velocity distribution in lubrication layers |
(2.20) | Volume flow rate in x and y directions |
2.2 Transmission Parameter Analysis of Helical Gear
2.2.1 Helical Gear Transmission Model
The contact trajectory of helical gear forms an inclined line during meshing due to their spiral angle. The length of this contact line changes periodically during the meshing process.
Figure 2-3 Schematic Diagram of Helical Gear Meshing
plaintext复制代码Ob1 -------------------------- Ob2 / \ / \ / \ Gear 1 ---------------------------- Gear 2
The length of the contact line l can be calculated using equations (2.24) and (2.25), and the total contact line length for multiple pairs of gears can be obtained using equation (2.26).
Equation | Description |
---|---|
(2.21) | Relationship between curvature radii |
(2.22) | Composite curvature radius |
(2.23) | Velocity component in the contact area |
(2.24) & (2.25) | Length of contact line |
(2.26) | Total contact line length |
2.2.2 Time-Varying Contact Line Length
The length of the contact line changes continuously during the meshing process of helical gear. The length of a single contact line can be calculated using equations (2.24) and (2.25).
Figure 2-4 Variation of Contact Line Length
plaintext复制代码Length of Single Contact Line | | | | | | |________________________________| Time
The total contact line length for multiple pairs of gears can be obtained by summing the lengths of individual contact lines.
2.2.3 Load Distribution on Helical Gear
The load distribution on helical gear tooth surfaces can be determined using the contact line percentage method. The load on a single tooth during meshing can be calculated using equation (2.27), and the unit load on the contact line can be calculated using equation (2.29).
Figure 2-5 Variation of Load on a Single Tooth
plaintext复制代码Load on Single Tooth | | | | | | |________________________________| Time
Equation | Description |
---|---|
(2.27) | Load on a single tooth |
(2.28) & (2.29) | Unit load on the contact line |
2.3 Helical Gear “Surge” Model
2.3.1 Establishment of the “Surge” Model
The generalized Reynolds equation for helical gear under traditional conditions is shown in equation (2.30). To derive the Reynolds equation applicable to “surge” conditions, the reflux equation and reflux coefficient are introduced.
Equation 2.30 Generalized Reynolds Equation
frac∂∂x(η∗ρh3∂x∂p)+∂y∂(η∗ρh3∂y∂p)=6u∂x∂(ρh)+12∂t∂(ρh)
The Reynolds equation considering “surge” is shown in equation (2.33).
Equation 2.33 Reynolds Equation Considering “Surge”
frac∂∂x(η∗ρh3∂x∂p)+∂y∂(η∗ρh3∂y∂p)+∂x∂(η∗ρh3usp)+∂y∂(η∗ρh3vsp)=6u∂x∂(ρh)
2.3.2 Dimensionless and Discretization of the “Surge” Equation
The dimensionless forms of the various equations are shown in equations (2.42) to (2.47). These equations are then discretized using the central difference method, and the discrete equations are solved using iterative methods such as Gauss-Seidel and Jacobi.
Equation | Description |
---|---|
(2.42) | Dimensionless Reynolds equation |
(2.43) | Boundary conditions of the dimensionless Reynolds equation |
(2.44) – (2.47) | Dimensionless film thickness, viscosity-pressure, density-pressure, and load balance equations |
2.3.3 Solution and Verification of the “Surge” Model
The “surge” model is solved using the multi-grid method, and the solution region is divided into five layers of grids. The convergence criteria are set as εP=10−5 and εF=10−4.
Figure 2-6 Flowchart of Solution for Helical Gear EHL Calculation Considering “Surge”
plaintext复制代码Start | Initialize parameters | Divide the solution region into grids | Set initial pressure and load | Iterate using Gauss-Seidel method | Check convergence criteria / \ Yes No | | Output results Repeat iteration | End
The influence of impact speed and impact position on “surge” is analyzed, and the results are compared with existing literature to verify the accuracy of the model.
Figure 2-7 Variation of Center Film Thickness with Displacement
plaintext复制代码(a) Center Film Thickness at Single Tooth Meshing Point (b) Center Film Thickness at Node (c) Center Film Thickness at Single Tooth Exit Point Displacement (m) | Center Film Thickness (μm) -----------------+-------------------------- 0 | 0.1 0.1 | 0.15 0.2 | 0.2 ... | ... 1.0 | 0.5
Figure 2-8 Variation of Minimum Film Thickness with Displacement
plaintext复制代码(a) Minimum Film Thickness at Single Tooth Meshing Point (b) Minimum Film Thickness at Node (c) Minimum Film Thickness at Single Tooth Exit Point Displacement (m) | Minimum Film Thickness (μm) -----------------+------------------------------ 0 | 0.05 0.1 | 0.075 0.2 | 0.1 ... | ... 1.0 | 0.25
3. Dynamic Characteristics of Helical Gear “Surge”
3.1 Dynamic Excitation of Helical Gear
3.1.1 Transmission Error Analysis
Transmission error can be simplified as a harmonic function, as shown in equation (3.1). In practical applications, the first harmonic term is often considered, as shown in equation (3.2).
Equation 3.1 Transmission Error Simplified as a Harmonic Function
e(t)=i=1∑neisin(iωt+ϕi)
3.1.2 Comprehensive Stiffness Analysis
In the meshing cycle of a helical gear pair, the load borne by the gears and the length of the contact line vary dynamically with the rotation of the gears, leading to fluctuations in the system stiffness. These stiffness fluctuations, in turn, excite internal vibrations within the system, a phenomenon known as stiffness excitation. When considering lubrication effects, the comprehensive stiffness of the helical gear pair consists of two components: the meshing stiffness of the gear teeth under dry friction conditions and the oil film stiffness formed by the lubricant.
(1) Meshing Stiffness of Helical Gear
Based on the parameters of the helical gear given in Table 2.1 and applying the corresponding calculation method for contact ratio, the contact ratio of the helical gear is found to be 2.38. This indicates that during meshing, the helical gear pair consistently exhibits alternating meshing states with two and three teeth. A mathematical equation describing the variation in stiffness along the meshing line for a single helical gear tooth is provided in reference [29]:
frackq(x)kp=23(xbt)0.5exp[−1.125(xbt)2]
where kp represents the tooth stiffness at the pitch point, and x denotes the position along the meshing line.
The stiffness kp at the pitch point can be calculated using the following equation:
kp=0.125Cb(btzv2)[1+2.5(zvc1)+(zvc2)2]
where Cb is a constant related to gear geometry, zv is the equivalent tooth number, and c1 and c2 are constants.
For the helical gear pair under consideration, the total meshing stiffness can be viewed as a system of springs connected in parallel. Therefore, the total meshing stiffness Kq can be calculated as:
Kq=i=1∑Nkq(xi)
where N is the number of teeth meshing simultaneously.
(2) Oil Film Stiffness
According to Hertz theory, when an infinitely curved equivalent cylinder comes into line contact with a rigid plane, the resulting contact pressure can be approximated as rectangular in theory. In such cases, the oil film in the contact region can be modeled as an elastic element, known as an “oil film spring.” To evaluate the stiffness characteristics of the oil film, the average deformation and the applied pressure are typically calculated. During the analysis, the entire computational domain is divided into several regions, and each region is processed using integration methods. Subsequently, an iterative algorithm is employed to solve for the oil film stiffness in each region, yielding values that more closely approximate actual contact conditions. Given these variations in geometric parameters, the oil film stiffness Ko is calculated using the method outlined in reference [88]:
Ko=n1i=1∑nΔxipi
where n is the number of nodes in the computational domain, pi is the pressure at node i, and Δxi is the distance between nodes.
(3) Coupled Stiffness
To investigate the influence of “surge” on the dynamic characteristics of the gear system, the meshing stiffness of the gears and the stiffness of the oil film are coupled, resulting in a single-tooth comprehensive stiffness Kt that reflects the interaction between the two:
Kt=kq+Ko
For multiple teeth meshing simultaneously, the total stiffness KT is given by:
KT=i=1∑NKti
The variation of the coupled comprehensive stiffness of the helical gear is illustrated in Figure 3-2. Both the single-tooth and total coupled stiffness of the helical gear exhibit a trend of increasing first and then decreasing. Notably, the coupled comprehensive stiffness is lower than the uncoupled stiffness for both single-tooth and total stiffness.
In summary, this section analyzes the transmission error and comprehensive stiffness of the helical gear, laying the foundation for the subsequent establishment of a dynamic model that considers these factors. By incorporating the coupled stiffness into the dynamic model, a more accurate simulation and prediction of the dynamic response of the helical gear pair under actual working conditions can be achieved, providing a scientific basis for designing helical gear transmission systems with higher performance and reliability.