Introduction
High-speed spur gear applications are critical in industries such as automotive, aerospace, and manufacturing. These gears must endure high rotational speeds, significant loads, and extreme conditions, making their design and manufacturing particularly challenging. This study explores the key challenges faced in high-speed spur gear applications and the solutions developed to address them.
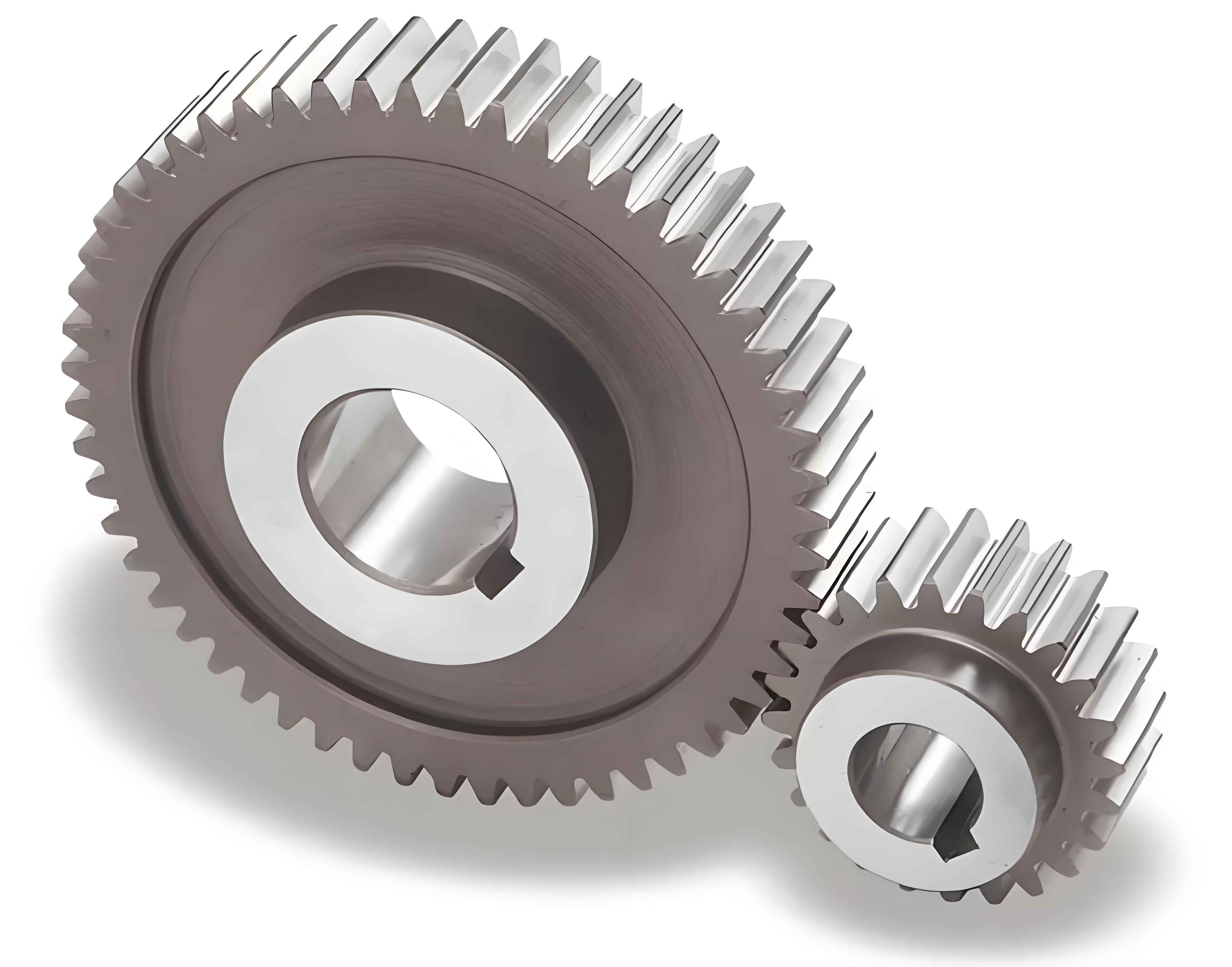
Challenges
- Thermal Expansion and Heat Dissipation
- Issue: High-speed operations generate substantial heat due to friction, leading to thermal expansion that can affect gear meshing and alignment.
- Solution: Use of advanced materials with high thermal conductivity and low expansion coefficients, and implementation of efficient cooling systems such as oil jets and heat exchangers.
- Wear and Fatigue
- Issue: High rotational speeds accelerate wear and fatigue, reducing gear lifespan and increasing maintenance needs.
- Solution: Application of surface treatments like carburizing, nitriding, and coatings (e.g., diamond-like carbon), and use of high-performance alloys that enhance wear resistance.
- Noise and Vibration
- Issue: High-speed gear operation often results in increased noise and vibration, leading to discomfort and potential damage to surrounding components.
- Solution: Precise manufacturing tolerances, use of helical gears where possible, and implementation of vibration damping materials and structures.
- Lubrication Challenges
- Issue: High speeds can lead to oil starvation or inadequate lubrication, causing increased friction and wear.
- Solution: Use of high-performance lubricants designed for high-speed applications, advanced lubrication systems that ensure consistent oil supply, and real-time monitoring of lubrication conditions.
- Dynamic Load Variation
- Issue: High-speed gears often experience fluctuating loads, which can lead to dynamic stress and potential gear failure.
- Solution: Design optimization using finite element analysis (FEA) to predict and mitigate stress concentrations, and incorporation of flexible couplings to absorb load variations.
- Alignment and Installation Precision
- Issue: Misalignment in high-speed gear systems can cause uneven load distribution and premature failure.
- Solution: Use of precision alignment tools during installation, continuous monitoring systems for real-time alignment adjustments, and implementation of self-aligning bearing systems.
Solutions and Technological Advancements
- Advanced Materials
- Development of composite materials and high-performance alloys that offer superior strength, wear resistance, and thermal properties.
- Use of lightweight materials to reduce inertia and improve efficiency.
- Innovative Manufacturing Techniques
- Adoption of precision manufacturing techniques such as CNC machining and additive manufacturing to achieve tighter tolerances and complex geometries.
- Implementation of laser surface treatments to enhance surface hardness and reduce friction.
- Improved Gear Designs
- Optimization of gear tooth profiles using computer-aided design (CAD) and finite element analysis (FEA) to enhance load distribution and reduce stress concentrations.
- Use of asymmetric gear teeth designed specifically for high-speed applications to improve load capacity and efficiency.
- Advanced Lubrication Systems
- Development of synthetic lubricants with superior thermal stability and wear resistance properties.
- Integration of automated lubrication systems that can adjust oil flow based on real-time operating conditions.
- Monitoring and Diagnostics
- Implementation of advanced sensor technologies and IoT (Internet of Things) for real-time monitoring of gear conditions such as temperature, vibration, and lubrication status.
- Use of predictive maintenance algorithms to anticipate potential failures and schedule timely interventions.
- Noise and Vibration Control
- Use of active vibration control systems and damping materials to minimize noise and vibration levels.
- Design of gear housings and mounts with acoustic insulation to reduce noise transmission.
Conclusion
High-speed spur gear applications pose significant challenges, primarily related to thermal management, wear and fatigue, noise and vibration, lubrication, dynamic loads, and alignment precision. Addressing these challenges requires a combination of advanced materials, innovative manufacturing techniques, optimized gear designs, improved lubrication systems, and real-time monitoring and diagnostics. By leveraging these solutions, it is possible to enhance the performance, reliability, and lifespan of high-speed spur gears, thereby meeting the demanding requirements of modern industrial applications.