This article focuses on the spindle system of a spiral bevel gear milling machine, aiming to study the dynamic characteristics of the spindle system and the matching relationship with processing technology parameters. Through in-depth research and analysis, a theoretical basis and practical guidance are provided for improving the machining accuracy and efficiency of spiral bevel gears. Firstly, the research background and significance are introduced, highlighting the importance of this study in the field of mechanical manufacturing. Then, the domestic and foreign research status is reviewed, including the research on dynamic modeling technology, excitation force, and process matching, summarizing the existing research results and deficiencies. Subsequently, the research content and methods are described in detail. The dynamic model of the spindle system is established using the finite element method, and the dynamic characteristics such as natural frequency and mode shape are analyzed. The cutting force model is established, and the influence of different process parameters on the cutting force is studied. Through simulation and experimental verification, the accuracy of the model and the rationality of the selected process parameters are verified. Finally, the research results are summarized, and the future research directions are prospected. This research is of great significance for optimizing the design and processing technology of the spindle system of a spiral bevel gear milling machine, improving the machining quality and efficiency of spiral bevel gears, and promoting the development of the mechanical manufacturing industry.
1. Introduction
1.1 Research Background and Significance
In modern mechanical manufacturing, machine tools play a crucial role as core equipment. With the continuous improvement of industrial production requirements for efficiency and quality, the machining performance of machine tools has attracted increasing attention. The machining performance of machine tools directly affects the quality of workpieces and the efficiency of cutting, and is also influenced by the dynamic performance of the machine tools. During the operation of machine tools, significant vibrations or deformations can directly impact the dynamic accuracy of the machining process, thereby affecting the surface quality of workpieces. This situation can lead to a significant decrease in production efficiency and hinder the production progress. In the long term, it may even shorten the service life of the machine tool and cause premature scrapping. Especially in the current widespread use of CNC machine tools, which achieve automated machining through various detection devices, severe vibrations may affect the normal operation of these detection devices. Moreover, since CNC machine tools are often in an unattended state, once severe vibrations occur, they are often difficult to detect and take countermeasures in a timely manner, which may ultimately affect the machining quality of products and even lead to potential safety hazards in the production process. Therefore, it is of great importance to fully understand and effectively control the vibration problems in the operation of machine tools.
The spindle system of a machine tool, as a key component in direct contact with the workpiece, is of crucial importance for studying its vibration characteristics. The vibration characteristics of the spindle system mainly include three core aspects: the inherent characteristics analysis of the spindle structure, the evaluation of the dynamic response, and the study of the cutting stability. The inherent characteristics analysis of the spindle structure covers multiple key elements such as the natural frequency, damping ratio, dynamic stiffness, and mode shape of components such as the spindle, bearings, and cutter head. These characteristics jointly determine the stability and performance of the machine tool during the machining process. The dynamic response describes in detail the vibration behavior characteristics exhibited by the spindle system during operation, including specific parameters such as the magnitude of the vibration amplitude, the frequency distribution, and the time required for the system to stabilize. These parameters are essential reference bases for evaluating the operational stability of the machine tool and optimizing the machining process. The study of cutting stability mainly focuses on the state of the system under the action of the cutting force, especially when specific cutting parameters are adopted, resonance phenomena may occur between the spindle-tool and the workpiece, which will have a significant impact on the machining quality and the performance of the machine tool. By thoroughly understanding the vibration characteristics of the spindle system, key process parameters such as the feed rate and spindle speed can be selectively adjusted to avoid the possible resonance points and cutting chatter regions of the spindle system. Such optimization measures are helpful for reducing or suppressing the vibrations of the machine tool during the cutting process, thereby improving the machining quality of parts and ensuring the stability and efficiency of production.
In general studies on the dynamic characteristics of machine tool spindle systems, researchers often excite the machine tool when it is shut down and simultaneously measure the excitation force signal and the vibration signal of the machine tool, and then post-process these signals to identify the modal parameters of the machine tool . If the dynamic characteristics of the spindle system during shutdown are the same as those during operation, the identification results during shutdown can be directly applied to the structural design of the spindle system or the machining process. However, from existing research, it can be seen that the dynamic characteristics of the spindle system in the actual operating state are constantly changing, which means that there are certain differences in the dynamic characteristics of the spindle system between the static and operating states [3]. Therefore, it is of great significance to deeply study the dynamic characteristics of the spindle system in the operating state. By revealing the changing laws of its dynamic characteristics during operation, directional guidance can be provided for the adjustment and optimization of machine tool machining parameters. This not only helps to significantly improve the machining accuracy of workpieces but also effectively enhances the machining efficiency.
The milling process parameters (such as cutting speed, feed rate, and cutting depth) are the main factors affecting the machining efficiency, machining quality, and tool wear. A large feed rate can increase the material removal rate, but it will also lead to excessive cutting force and a significant increase in machine tool chatter, resulting in a decline in workpiece machining quality. Conversely, a smaller feed rate can ensure the surface quality of the workpiece and reduce machine tool vibrations, but it will prolong the cutting time and reduce the machining efficiency. Currently, the selection of machining process parameters usually relies on existing literature or relevant experience, but this method has limitations. In general, the parameter selection is relatively conservative and cannot fully utilize the performance of the machine tool and the tool, thereby reducing the actual machining efficiency. Therefore, the selection of reasonable process parameters is not only beneficial for reducing machine tool vibrations but also helps to improve the cutting efficiency and ensure the machining quality.
This research addresses the insufficient matching between milling process parameters and machine tool characteristics in production. Combining the current research on the dynamic characteristics of the spindle system of a spiral bevel gear milling machine and the matching of machining process parameters, a method is proposed to judge the matching between machining process parameters and the characteristics of the spindle system of the milling machine through the response status. This method aims to fully utilize the performance of the machine tool, reduce the vibrations in the machining process of the machine tool, and improve the machining efficiency, machining accuracy, and tooth surface machining quality. Specifically, this method analyzes the dynamic response of the spindle system of the milling machine when subjected to the actual cutting force and adjusts the machining process parameters to match the characteristics of the machine tool, thereby maximizing the optimization of the machining process. Under the guidance of this method, the spindle speed and feed rate and other parameters can be flexibly adjusted according to the dynamic response of the spindle system under different process parameters to achieve the best machining effect. By fully understanding and utilizing the dynamic characteristics of the machine tool, the vibrations in the machining process of the machine tool can be effectively reduced, the machining efficiency and machining accuracy can be improved, and better machining quality can be obtained in the tooth surface machining process.
1.2 Research Status at Home and Abroad
1.2.1 Dynamic Modeling Technology
The spindle is a crucial part of the machine tool, and its dynamic characteristics and dynamic performance directly affect the machining efficiency and machining accuracy of the machine tool. The dynamic characteristics of the spindle mainly include key parameters such as natural frequency, mode shape, critical speed, and dynamic response . Before 1960, the design of the spindle mainly relied on the empirical simulation method. However, due to the influence of the equipment and tools at that time, this method not only had limited accuracy but was also quite cumbersome in actual operation. With the rapid development of computer technology, new methods such as the lumped parameter method, transfer matrix method, and finite element method have emerged . These methods provide more accurate and efficient ways for spindle design and analysis.
The lumped parameter model is a widely used structural dynamics modeling method. Its core idea is to concentrate the mass of the structure on several nodes and use a series of massless equivalent elastic beams to simulate the elastic characteristics of the structure. Although the lumped parameter model can provide relatively accurate results in some cases, its limitations are also obvious. Especially for complex machine tool structures, it is often difficult to accurately simulate their dynamic behaviors with simple and reasonable mechanical models. In addition, when considering the nonlinear and coupling effects of the system, the accuracy of the lumped parameter model is usually low.
In 1964, Taylor first adopted the idea of lumped mass in the stiffness calculation of a radial drilling machine and obtained the natural frequency and mode shape consistent with the measured values . Tlusty and Altintas simplified the machine tool structure and adopted the lumped parameter model for modal experiments. However, due to the lack of theory and equipment at that time, their model only considered a few low-order modes . In 1976, Nelson et al. established a finite element model of the spindle system using the compatibility matrix method. They analyzed two spindle systems with different bearing characteristics and obtained the unbalanced response of the typical cantilever shaft structure. At the same time, they used the lumped mass method to compare and analyze the conclusions in these two cases . Feng Jilu et al. simplified the spindle-bearing system of the machine tool using the lumped mass method, established a spindle vibration analysis model considering multiple factors, and analyzed the nonlinear dynamic characteristics of the spindle-bearing system under the action of unbalanced forces . Yang Yiqing et al. established a 7-degree-of-freedom model of a vertical milling machine using lumped mass and spring-damping elements based on the modal analysis and visualization of the milling machine. Their research results revealed the relationship between machine tool chatter and mode shape, and their model had higher accuracy than the original test frequency response function . Huang Zhikai et al. used the lumped mass method to compare the low-order modal frequencies of equal-section beams with different mass distributions at both ends supported by hinges. Their research provided a feasible method for the simplified calculation of the modal frequency of the beam and obtained the formula for the critical speed of each order of the beam
The transfer matrix method is an important classical method for analyzing the dynamic characteristics of slender structures such as shafts and beams. When analyzing the dynamics of the spindle system, the transfer matrix method adopts a series of discretization steps to divide the spindle system into discrete bodies composed of several lumped masses, rigid disks, and elastic shaft segments. Then, the state vectors of each unit are related to each other using the combined transfer matrix of each unit wheel disk, shaft segment, and spring. Through these relationships and the boundary conditions of the spindle, the frequency polynomial is obtained, and finally, the critical speed and dynamic response of the rotor system are solved using the iterative method. The transfer matrix method has the advantages of simple program, easy implementation and understanding, fast calculation speed, and relatively accurate prediction of the critical speed and mode shape of the system, which can provide important references for engineering design. However, when applying the transfer matrix method, there are also some problems. For example, when calculating high-order modes, the accuracy of the transfer matrix method may decrease , so appropriate processing methods need to be adopted to improve the accuracy of the calculation results. In addition, due to the nonlinear and coupling effects of the system, the transfer matrix method may not be able to fully capture the dynamic behavior of the system, so its applicability needs to be considered according to the actual situation.
Wu Hui studied the spindle system and transmission system of a certain type of centerless machine tool. He established the mathematical model and dynamic model of the spindle system and transmission system of the machine tool using the Riccati transfer matrix method and obtained the inherent characteristics of the transverse vibration of the spindle system and the inherent characteristics of the torsional vibration of the transmission system of the machine tool. His research results provided a scheme for the dynamic optimization of the machine tool structure . Meng Jie established the dynamic model of a high-speed electric spindle after simplifying it based on the transfer matrix method and obtained the natural frequency and mode shape of the electric spindle at a certain speed . Wu Lingwei studied a flying-cut machine tool. He established the transfer matrix of each element of the machine tool system using the transfer matrix method and studied in detail the vibration characteristics and dynamic response of the machine tool . Tian Yue established the dynamic model of the spindle system of a certain machine tool using the transfer matrix method and studied the influence of the spindle eccentricity, the front and rear bearing clearances, and the front and rear bearing stiffnesses on the dynamic characteristics of the spindle system, providing some ideas for the structural optimization of the spindle system . Qian Mu et al. studied the dynamic characteristics of a grinding electric spindle system using the transfer matrix method. The results showed that the transfer matrix method can be applied to the dynamic design of the electric spindle . Zhu Jinhu et al. established the dynamic model of a certain high-speed electric spindle using the transfer matrix method and successfully obtained the relevant parameters affecting the critical speed of the electric spindle . Wu Wenjing et al. proposed an extended transfer matrix method. They divided the mechanical system into three types of elements: rigid bodies, flexible bodies, and joint surfaces, and gave the mathematical models of these elements in matrix form. The research results showed that this method has good accuracy for the modeling and dynamic characteristics analysis of the whole CNC machine tool .
With the rapid development and wide application of computer technology, the finite element method has become an indispensable important numerical analysis tool in scientific research and engineering design. In the field of machine tool spindles, the finite element analysis method can perform static analysis on the spindle system to obtain its static stiffness. At the same time, through dynamic analysis, the natural frequency, dynamic response of the spindle system can be obtained, and further optimization design can be carried out. The static and dynamic characteristics of the spindle system are directly related to the performance of the whole machine and are of great significance for improving product quality and ensuring the dynamic machining accuracy of the machine tool.
Abroad, Bollinger et al. conducted a preliminary study on the static and dynamic performance of machine tool spindles using the finite element method . R. Reddy et al. established a finite element model of the machine tool spindle based on the finite element method and performed dynamic analysis on it . Severn adopted the Timoshenko beam element considering shear deformation for the dynamic modeling of the spindle system. Each element has two nodes and a total of six degrees of freedom, but no in-depth study was conducted on the response of the spindle system after dynamic modeling . Gagnol et al. modeled the high-speed spindle-bearing system using the Timoshenko beam element and considered the influence of the gyroscopic effect on the dynamic characteristics of the spindle system at the same time. Their model provided a certain reference value for the identification and prediction of the spindle in the actual machining process of the machine tool . Lin adopted the finite element method to model the dynamics of the spindle system and optimized the structure of the spindle system. However, this method is too complex and does not have universal applicability . Jorgensen et al. established the dynamic model of the high-speed spindle system using the Timoshenko beam theory. They considered two factors, external load and thermal deformation, when applying the boundary conditions, so their analysis results are more in line with the actual machining state of the spindle system .
In China, many universities, research institutions, and scholars are also engaged in research in this field . In the 1980s, the “Rotor Dynamics” written by Zhong Yi’e and others from Tsinghua University introduced in detail the analysis methods of the rotor system and has good reference value . Sun Wei et al. took the high-speed spindle system as the research object and systematically analyzed the inherent characteristics of the spindle system in different working states using the finite element analysis method. They also considered the influence of the rotational speed on the frequency response function of the tool tip point. The results showed that there are differences in the dynamic characteristics of the spindle system between the static and motion states . Cao Hongrui et al. constructed the finite element models of each component of the spindle system one by one and then combined these sub-models to construct the dynamic model of the whole system. In the research, they not only considered the gyroscopic effect and centrifugal force of the rotor but also deeply analyzed the influence of the bearing softening on the dynamic characteristics of the spindle system. The research results showed that in order to accurately calculate the dynamic characteristics of the spindle system, the softening effect of the bearing must be considered . Ling Jiayu established the dynamic model of the spindle system considering the spindle box, feed system, and the joint surface of the spindle-tool holder-tool and gave the theoretical calculation formula of the typical joint surface stiffness. Through the established dynamic model, the vibration error of the spindle system was estimated . Kang Ting et al. established the dynamic model of a certain high-speed spindle using the Timoshenko beam element and predicted the vibration response of the spindle by inputting the collected cutting force into the dynamic model. Xu Qingyong took a certain type of CNC milling machine as the research object and performed static and dynamic analysis and structural optimization on the key components of the spindle system using the finite element method .
Through the above research, it can be seen that scholars at home and abroad have adopted a variety of theories and methods to solve the dynamic problems of the whole machine or the spindle system and have conducted in-depth research. They used the lumped parameter method to model the whole machine tool to study its natural frequency and mode shape. They used the transfer matrix method to explore the dynamic characteristics of the spindle system and the influence of the machining component parameters on the dynamic characteristics of the spindle system. At the same time, they used the finite element method to study the response of the spindle system when subjected to external excitation. These studies have deeply explored the dynamic characteristics of the spindle system from different angles and provided important theoretical and technical support for the field of machine tool machining. However, most of these studies focused on common machine tools such as lathes and milling machines or their components, and relatively few studies were conducted on the spindle system of a spiral bevel gear milling machine. Therefore, it is necessary to extend the existing research methods to the spindle system of the milling machine to fill the research gap in this field and further improve the theoretical system and application methods of the dynamics of the machine tool spindle system.
1.2 Research Status at Home and Abroad
1.2.2 Research Status of Excitation Force
At present, most of the research on the dynamic characteristics of machine tool spindle systems focuses on applying artificial excitation to the machine tool when it is shut down to study its dynamic characteristics. However, existing research shows that there are significant differences in the dynamic characteristics of the machine tool between the shutdown state and the running state, especially in the high-speed running state. Therefore, how to apply excitation during the operation of the machine tool to study its dynamic characteristics is a problem that needs to be faced. With the development of technology, some new excitation methods have emerged, such as using electromagnetic exciters, piezoelectric sensors, or using the vibration signal of the machine tool itself as the excitation source. Domestic and foreign scholars have conducted research on this and achieved certain results. Hanna et al. applied random excitation and sinusoidal excitation to the machine tool in operation using exciters and studied the modal and response of the machine tool. The research results showed that the machine tool exhibits nonlinear characteristics in the operating state [34]. Liao Boyu et al. performed modal analysis on the spindle of a lathe when it was rotating using the M-sequence random signal. The research results showed that the modal parameters of the lathe spindle are different in the static and motion states [35].
In 1981, Ji Qingfa and Du Shucai from Jilin Institute of Technology proposed using cutting force as the excitation force to study the dynamic characteristics of the machine tool. They conducted relevant experiments on a lathe and successfully identified the natural frequency of the system. They also preliminarily proposed a mathematical method for online analysis of the structural modal parameters of the machine tool using random data analysis theory. However, due to the need to measure the cutting force in the analysis process and the limitations of the identification technology at that time, only the natural frequency could be simply identified, and more comprehensive modal parameter information could not be obtained [36-37]. Jiang Xiaofei established a dynamic excitation force model of the machine tool based on the theoretical model of milling cutting force and through cutting experiments for parameter identification. The excitation force model consists of static force and dynamic force and considers the influence of different process parameters. The dynamic performance of the machine tool in different frequency bands was successfully obtained. At the same time, a dynamic characteristic test system for CNC machine tools was built to meet the measurement of dynamic cutting force under different cutting process parameters [38].
From the above research, it can be seen that domestic and foreign scholars have studied the excitation force of the whole machine tool or the spindle system in a variety of ways, covering different excitation sources and analysis methods. On the one hand, they analyzed the modal of the machine tool in the operating state by applying exciters and applying excitation forces with specific frequencies and amplitudes. On the other hand, some scholars used the cutting force as the excitation source and used corresponding methods to identify the modal parameters of the machine tool structure. This method studied the actual workpiece cutting situation in the machining process and helped to more accurately evaluate the dynamic characteristics of the machine tool. In addition, some researchers measured the dynamic excitation force by changing process parameters such as cutting speed and feed rate to explore the influence of these parameters on the vibration characteristics of the machine tool. However, these research methods are mostly concentrated in the idling state of the machine tool or in common machining methods such as turning and milling. There is relatively little research on the excitation force in the process of spiral bevel gear milling. This is because the spiral bevel gear milling process has complex cutting forces and process parameters and requires more in-depth research on its particularity. Therefore, it is necessary to explore the characteristics of the excitation force in the process of spiral bevel gear milling to improve the research in this field.
1.2.3 Research Status of Process Matching
The milling process parameters are the key factors affecting the machining efficiency, machining quality, and tool durability. For example, if the cutting parameters are set too large, although the material can be removed quickly, the excessive cutting force may cause machine tool chatter and a decline in machining accuracy, and the cutter head wear will be aggravated. Conversely, if the cutting parameters are too small, although the machine tool vibration can be reduced, the prolonged cutting time will directly lead to low machining efficiency. Currently, the selection of process parameters is mostly based on literature or experience, and this conservative selection often cannot fully utilize the performance of the machine tool, thus limiting the improvement of machining efficiency. Therefore, the reasonable selection of process parameters is crucial. It helps to reduce the vibration of the machine tool while improving the cutting efficiency and ensuring the machining quality.
One of the methods to optimize the process parameters is to use optimization algorithms to optimize single or multiple process parameters. Azlan et al. obtained the process parameters that minimize the surface roughness of the workpiece using artificial neural networks and simulated annealing algorithms [39]. Suman et al. found the optimal parameters under different machining processes using the artificial ant colony algorithm [40]. Liu Yang optimized the multi-objective process parameters using the genetic algorithm [41]. Some scholars also improved the accuracy of the optimization results by improving or combining optimization algorithms. Wei Hui established the prediction models of workpiece surface roughness and milling force by measuring the cutting force and the surface roughness of the machined workpiece in the milling process. Then, using the machining deformation and milling force as constraints and the minimum surface roughness and maximum material removal rate as optimization objectives, the process parameters were optimized using the genetic algorithm [42]. Fuad and Bhushan optimized the process parameters from the perspective of machine tool energy consumption using the response surface method [43-44]. Zhong Jinlong established an optimization model with machining time and machining cost as the objectives for a high-speed dry gear hobbing machine and verified the effectiveness of the process parameter optimization through corresponding algorithms and experiments [45]. Jia Xinjie obtained the parameter optimization method for rough milling of spiral bevel gears using the harmony search algorithm and established an optimization model for the rough milling process parameters of spiral bevel gears. Through programming, he obtained the best rough milling cutting parameters [46]. Zhang Zhengwang et al. obtained the optimal combination of milling process parameters using the high-speed milling process parameter optimization method based on the dynamic behavior of the spindle system. The experimental results showed that the obtained optimal milling process parameters will not cause chatter during actual cutting [47].
Another method to optimize the process parameters is to conduct experiments or simulations for the objective function, analyze the changes of the objective function under different process parameters, and then select appropriate process parameters. Mao Hanying et al. designed multiple groups of experiments with different cutting depths and cutting thicknesses. In the process, they collected the vibration acceleration signals from the stable cutting state to the occurrence of chatter and then studied the vibration change laws of these signals [48]. Wu Xiao established a two-degree-of-freedom milling dynamics model, a cutting force model, and a cutting thickness model for the machining of non-thin-walled workpieces with end mills. Using the full discretization method, he obtained the prediction model of variable cutting force coefficient and variable speed milling stability. On this basis, he analyzed the influence of the cutting force coefficient and process parameters on milling stability and constructed a multi-objective optimization model with a larger material removal rate and a smaller cutting force as the objectives and milling stability as the constraint. The experimental results showed that the optimized process parameters can ensure a smaller cutting force while improving the material removal rate [49]. Jiang Yancui established the dynamic model of the spindle system of an automobile mold milling machining system and obtained the change laws of its dynamic characteristics. Using the frequency domain method for milling stability prediction and the optimization function for process parameter optimization, the experimental results showed that the optimized process parameters can improve the machining accuracy of the mold surface [50]. Luo Hanbing et al. aimed at the problems in the selection of machining process parameters in the CNC milling process. Taking the high-speed milling process of ball end mills as the research object, they established a nonlinear dynamic model considering the machine tool-tool-workpiece system and analyzed the influence of the dynamic force components in the milling process on cutting chatter. At the same time, based on the dynamic milling force modeling and chatter stability domain analysis and calculation, they proposed a prediction method for the stability limit of the machine tool cutting system. Their research results showed that the model can provide a basis for the reasonable selection of process parameters in the milling process [51].
From the above research, it can be seen that domestic and foreign scholars have fully studied the problems such as the characteristics of the machine tool spindle system and the adjustment of process parameters in the machining process. They either optimize the process parameters using optimization algorithms or select the optimal process parameters through simulation experiments, revealing the relationship and laws between the characteristics of the machine tool spindle and the machining process parameters, indicating the close relationship between the characteristics of the machine tool spindle and the selection of process parameters and the feasibility of this research topic. These studies provide a reliable scientific basis for the selection of cutting parameters, reduce the cutting cost, and improve the machining quality. However, we also note that most of these studies focus on using optimization algorithms to optimize the process parameters, and there are few studies on optimizing the process parameters through the system response. Moreover, there are relatively few studies on the optimization of the process parameters of the spiral bevel gear milling machine. Therefore, this article will conduct research from the aspect of the response of different process parameters and further explore the parameter adjustment methods in the milling process.
In summary, domestic and foreign scholars have conducted a large amount of research on dynamic modeling technology, excitation force research, and the matching of machine tool characteristics and process parameters, providing important theoretical and practical support for the research on the matching of the dynamic characteristics of the spindle system of a spiral bevel gear milling machine and the machining process parameters. Therefore, in view of the problem of the low matching degree between the process parameters and the dynamic characteristics of the spindle in the milling process, combined with the current research results of dynamics and the optimization methods of process parameters, this research starts from the dynamics of the spindle system and studies the excitation and response of the system and the optimization of process parameters.
1.3 Research Content and Research Methods
This article aims to achieve the matching of the characteristics of the spindle system of a spiral bevel gear milling machine and the process parameters to improve the milling efficiency and the quality of the tooth surface machining. According to the basic principles of machine tool dynamics, the finite element method is used to establish the finite element dynamic model of the spindle system of the milling machine. Based on this, the response analysis of the machine tool under different machining parameters is completed using the numerical method, and the correctness of the constructed numerical model and the effectiveness of the selected process parameter combination are verified through finite element simulation and experiments.
First, based on the finite element dynamics theory and the Timoshenko beam theory, the dynamic model of the spindle system of the milling machine is established. By solving the motion differential equation, the natural frequency and mode shape of the spindle system are obtained. On this basis, the dynamic responses in each direction are calculated using the mode superposition method and the numerical integration method, including the harmonic response analysis and the transient response analysis. At the same time, the finite element software is used to simulate and calculate the response conditions under the same conditions as the numerical model to verify the accuracy of the numerical model and lay the foundation for the subsequent research on the matching of process parameters using the numerical model.
Since the cutting force is the main excitation source in the milling process, this article derives the milling cutting force components in three directions based on the oblique cutting theory and establishes a theoretical cutting force model. On this basis, the influence of different process parameters on the cutting force amplitude is analyzed. Then, the finite element cutting simulation software AdvantEdge FEM is used to calculate the cutting forces under different process parameter combinations. By inputting the results calculated by the theoretical cutting force model into the finite element numerical model for analysis, a set of process parameters with good matching with the dynamic characteristics of the spindle system is obtained. Finally, machining experiments are carried out under this set of process parameters to test the matching effect with the dynamic characteristics of the spindle system. The technical route of this article is shown in Figure 1.1.
The main research content and analysis methods of this article are as follows:
Chapter 1: Introduction
This chapter mainly introduces the source of the research topic, the research background and significance of the paper. It expounds the domestic and foreign research status of the dynamic modeling of the spindle system of a spiral bevel gear milling machine, the research on excitation force, and the matching of process parameters and machine tools.
Chapter 2: Dynamic Modeling and Analysis of the Spindle System
This chapter first introduces the basic principles of rotor dynamics equation construction. Then, based on the Timoshenko beam theory, the finite element dynamic model of the spindle system of the milling machine is established, and the bearing coupling effect is considered. On this basis, the natural frequency, mode shape, harmonic response, and transient response of the spindle system are analyzed using the numerical method, and the response of the spindle system calculated by the finite element software is fully verified.
Chapter 3: Analysis of Milling Cutting Excitation Force
This chapter analyzes the various excitation sources in the milling cutting process and concludes that the cutting force is the most important excitation source in this process. Based on the oblique cutting theory and the relative position relationship between the cutter head and the gear blank in the milling process, the calculation formulas of the cutting forces in each direction when machining the pinion by the generating method are derived, and a theoretical cutting force model is established. Based on this model, the cutting force amplitudes under different process parameters are calculated to lay the foundation for process parameter optimization. At the same time, the finite element cutting simulation software AdvantEdge FEM is used to calculate the cutting forces in each direction under different rotational speeds and feed rates, and the frequency components of the cutting forces are analyzed to study the influence of different process parameters on the cutting force and the cutting force frequency.
Chapter 4: Verification of Dynamic Characteristics Analysis and Process Matching Effect
Based on the calculation of the theoretical cutting force amplitudes under different process parameters in the previous chapter, this chapter selects and analyzes the cutting forces under four groups of process parameters and obtains a set of optimal parameters. By conducting experiments on this set of parameters and another set of parameters that cause a sudden change in the main cutting force amplitude, a set of optimal parameters is obtained. The harmonic response analysis of the cutting force under this set of parameters is carried out using the established numerical model to verify the matching situation between this set of process parameters and the spindle system. In addition, the sensitivity of the main cutting force is analyzed, and two ways to change the sensitivity of the spindle system are proposed to ensure the quality of the tooth surface machining.
Chapter 5: Summary and Outlook
This chapter summarizes the research work carried out in this article and gives the conclusions. At the same time, according to the deficiencies in the research work of this article, the outlook for the next work is put forward.
2. Dynamic Modeling and Analysis of the Spindle System
2.1 Basic Principles of Rotor Dynamics Equation Construction
The dynamic characteristics analysis of the spindle system of a spiral bevel gear milling machine can establish its dynamic model through the basic principles of dynamics and then obtain the inherent characteristics of the system by solving the corresponding equations. At present, the establishment of a dynamic model usually adopts theoretical modeling, experimental modeling, and a combination of theoretical and experimental modeling methods [52].
When constructing a theoretical model, it is often necessary to simplify the system structure. However, due to the lack of a unified and standardized theoretical calculation method for the dynamic characteristics of the joint, there may be a large deviation or error between the established model and the actual situation. However, compared with other models, it has significant advantages in structural optimization. The experimental model can truly reflect the dynamic performance of the machine tool, but due to its limited degrees of freedom and the need for experimental prototypes, the design cost is relatively high. Although the hybrid model combines the advantages of the theoretical model and the experimental model, it also inherits the limitations of the experimental model.
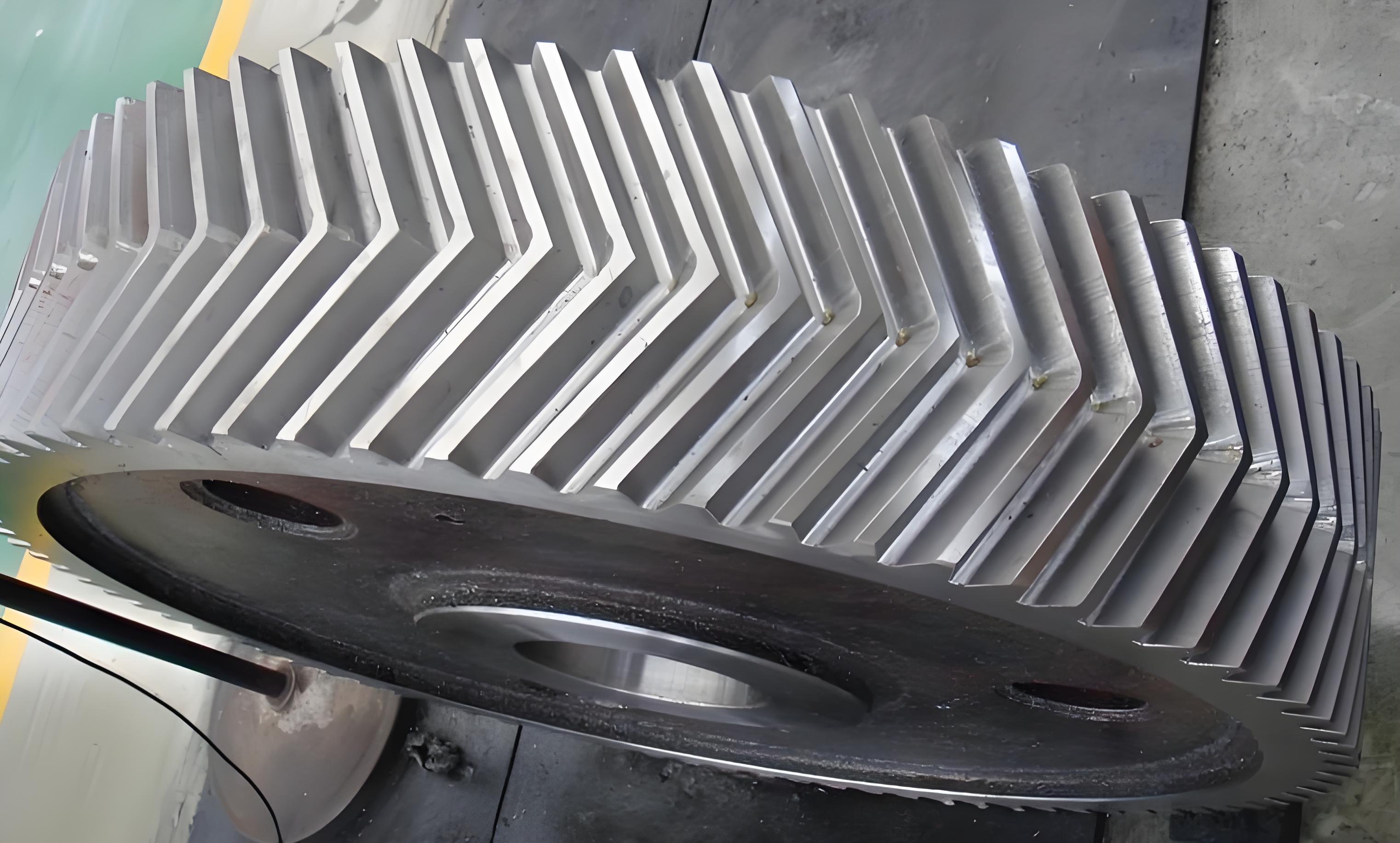