The forming quality of forgings directly determines the product quality and service life. After hot die forging, the surface finish of gear blank is not good and the dimensional accuracy is low. Therefore, it is necessary to carry out cold precision forging on the hot die forging gear blank after removing the oxide skin on the surface to improve its dimensional accuracy and forming quality, so as to make it meet the technical requirements of the final product. If the tooth shape of cold precision forging preform is not designed properly, it will not only cause metal folding and other defects due to the unreasonable metal flow, but also seriously affect the service life of cold precision forging die. In conclusion, it has far-reaching practical significance for the tooth shape optimization of cold precision forging preform.
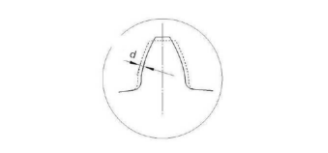
Based on the cold forging drawing, the uniform diffusion tooth profile is a tooth profile scheme, which extends the tooth profile uniformly outwards according to the amount of cold precision forging, and then shrinks the size of tooth top circle radially to make the forging conform to the principle of equal volume. The figure shows the scheme of uniform diffusion tooth. In the figure, the solid line is the tooth shape of cold precision forging die, the dotted line is the tooth shape of cold precision forging preform, and D represents the cold precision forging amount (mm). At present, only similar schemes have been used in literature to study the design of cold precision forging preform tooth profile of spur bevel gear, and it is concluded that when the amount of cold precision forging is large, there will be different degree of folding at the root of spur bevel gear, while when the amount of cold precision forging is small, the forming effect of forging tooth surface will be reduced. In this paper, we first try to use the uniform diffusion tooth profile scheme in the cold precision forging process of spiral bevel gear.
Establishment of finite element model and setting of relevant parameters
For the setting of preprocessing simulation parameters:
1.Since the material of driven spiral bevel gear studied in this paper is 20CrMoH, but there is no such material in the DEFORM-3D material database, aisi4120 with very similar material properties is selected as the workpiece material for simulation and the workpiece is set as plastic body;
2.Because this part focuses on the optimization of the blank tooth shape of the driven spiral bevel gear and the processing temperature of the cold precision forging process is normal temperature, the mold temperature has little influence on the forming process of the workpiece; based on the consideration of improving the operation efficiency, the mold is simplified as a rigid body and not divided into meshes; the temperature of the cold precision forging preform is set as the default 20 ℃;
3.The tetrahedron element type is selected to better characterize the meshing of gears with complex geometric conditions; the relative meshing mode is adopted, and the number of meshes is set to 200000, and the FEM + mesh mode is turned on to activate the automatic compensation to make up for the volume difference caused by mesh distortion in the process of gear forming;
4.Considering the location of the gear blank on the die bore and the geometric characteristics of the gear blank, the gear profile die is set as the lower die;
5.Set the upper mold movement speed to 26mm / sec;
6.The workpiece is cold precision forged after surface treatment and phosphorus saponification treatment, so the lubrication between workpiece and die is good, so the friction coefficient is 0.12;
7.Set the heat conduction coefficient of workpiece and air to 5;
8.Check that the minimum size of the workpiece grid is about 0.9mm. Considering the simulation accuracy and time efficiency, the simulation step size is set to one third of the minimum size of the workpiece grid, i.e. 0.3mm.
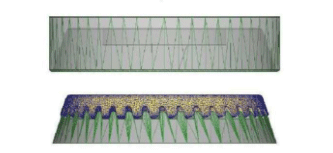