Gear modification is an important technology to reduce gear vibration noise and prolong its service life. Because of the variety of gears, the complexity of working conditions, and the different gear modification parameters under different working conditions, it is difficult to form a complete gear modification system.
Under ideal conditions, the meshing gear pair with absolute rigidity and high manufacturing and installation accuracy will not have any transmission problems. Under actual working conditions, because the gear material will have elastic deformation under the force, and at the same time, it will be affected by the installation position deviation and manufacturing accuracy error, the meshing gear pair will inevitably form meshing in and meshing out impact, which will eventually cause geometric interference of the gear pair. In addition, the whole gear transmission system will also experience elastic deformation due to load, such as contact, shear, bending deformation of gear teeth, torsion, bending deformation of shaft body, which will eventually lead to partial eccentric load of gear teeth during meshing. In order to reduce the meshing impact and the eccentric load caused by the elastic deformation of the gear transmission system, Walker H first proposed the concept of gear modification in 1938. Later, after a long exploration by many scholars, the theory of gear modification technology was initially formed in the 1970s. Nowadays, more and more scholars are obsessed with this, and they have no hesitation to rush to the fertile land of gear modification, and bloom and bear fruit on this land.
In terms of tooth profile modification, Yang Y et al. used ANSYS to simulate and compare the transmission error of helical gears engaged with different tip clearance to the finite element model and the size of time-varying meshing stiffness, and obtained the conclusion that properly thinning the tip will reduce the vibration response of helical gears. Yoon M et al. calculated the peak and peak values of transmission error and contact stress of different parts of the helical gear teeth under different load conditions based on the finite element method, and finally determined the optimal tooth profile modification parameters of helical gear teeth from the top to the root under this working condition. LiX established a new calculation model for meshing stiffness of nonlinear swing array gear pair, and proved theoretically that proper tooth profile modification can optimize the torsional meshing stiffness and transmission error of gears. Tang H C et al. modified the tooth profile and tooth direction of the main gear pair, eliminated the gear interference caused by the tooth profile error, and adopted the drum shape modification to improve the uneven distribution of its contact stress, which effectively suppressed the gear squeal noise of the automobile transmission. Wang Jun et al. applied tooth profile modification to improve the lubrication performance of cycloidal gears during meshing, and deeply studied the influence law between tooth profile modification and friction loss power. Yang Long et al. obtained the influence law of the tooth surface temperature of the modified gear by using ANSYS simulation, and believed that proper tooth profile modification could reduce the tooth surface temperature and improve its meshing transmission characteristics.
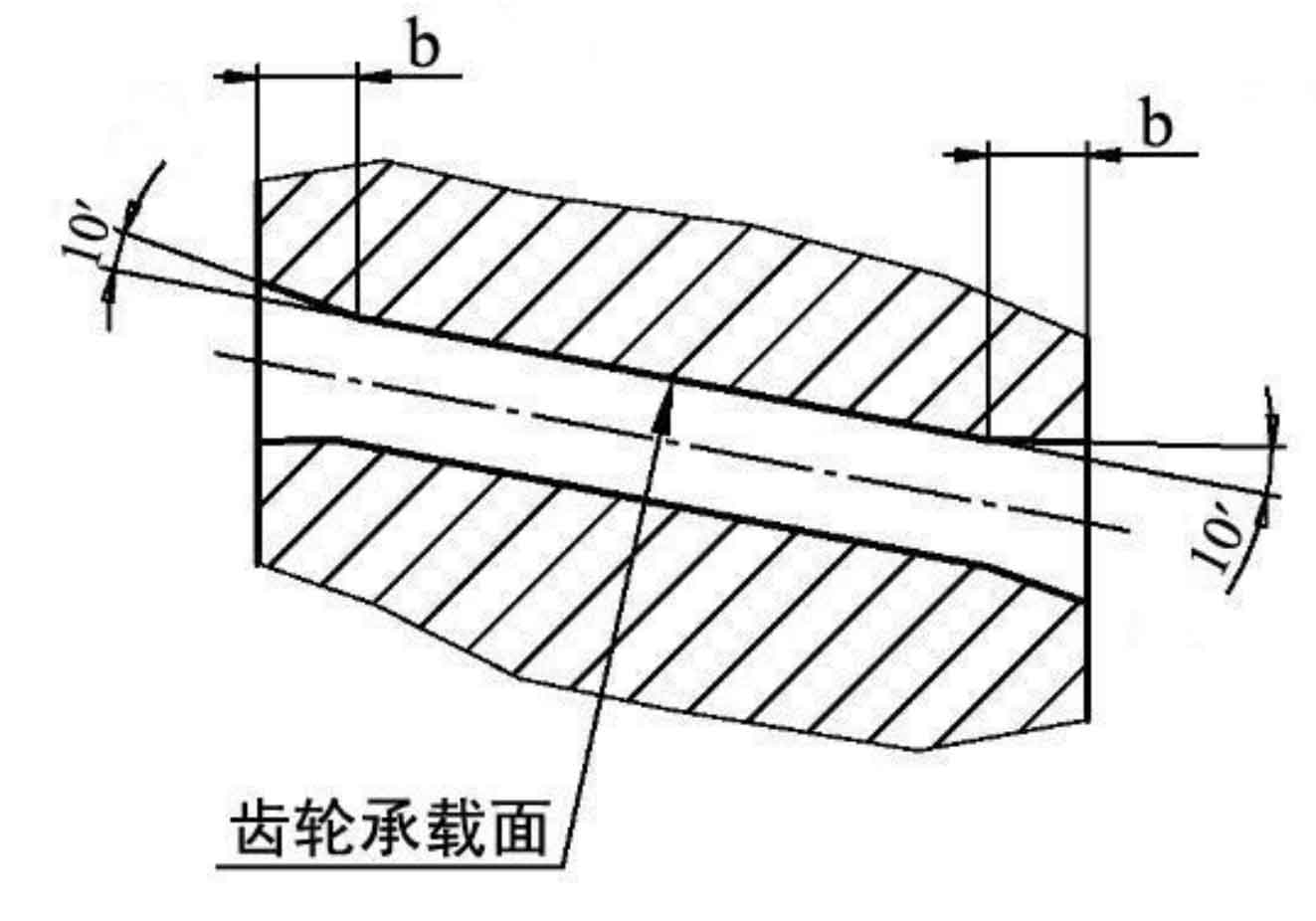
In terms of tooth modification, Jiang J et al. optimized the meshing model of gear pair considering axial displacement and deformation by using genetic algorithm, improved the transmission instability caused by installation deviation, bending and torsion deformation, elastic deformation, etc., and proved that tooth modification can make the load distribution on the tooth surface more uniform. Cui HY et al. modified the bevel gear with equidistant tooth direction based on the classical modification theory. Using finite element analysis and enterprise production practice, the service life of the modified bevel gear increased by 10%. Shu You and others solved the problem of uneven stress distribution and excessive vibration noise of gear teeth by using the composite modification technology of tooth profile involute and tooth direction drum. In order to reduce the frequency of tooth surface scratches and fractures at the root of helical gear, Yang Ke compared the stress of helical gear teeth under different modification schemes on the basis of finite element analysis based on the classical tooth direction modification theory. After weighing, he adopted a special tooth end modification method (as shown in the figure) to effectively avoid stress concentration along the tooth width direction of the load, and reduce the root stress and the vibration noise of helical gear.