When metal is heated in oxidizing atmosphere (air or furnace gas), it will react with O2, H20 or CO2 to oxidize the metal surface. The higher the temperature, the longer the heating time, the more serious the oxidation. After the steel is oxidized, a layer of oxide skin is formed on the surface to cause burning damage: the oxide skin has high hardness, which accelerates the wear of the die. The oxide skin is pressed into the bevel gear forgings, reducing the surface finish and dimensional accuracy of the bevel gear forgings. Oxidation not only forms oxide skin, but also reduces the content of carbon and alloy elements on the surface of steel, and reduces the surface properties of bevel gear forgings.
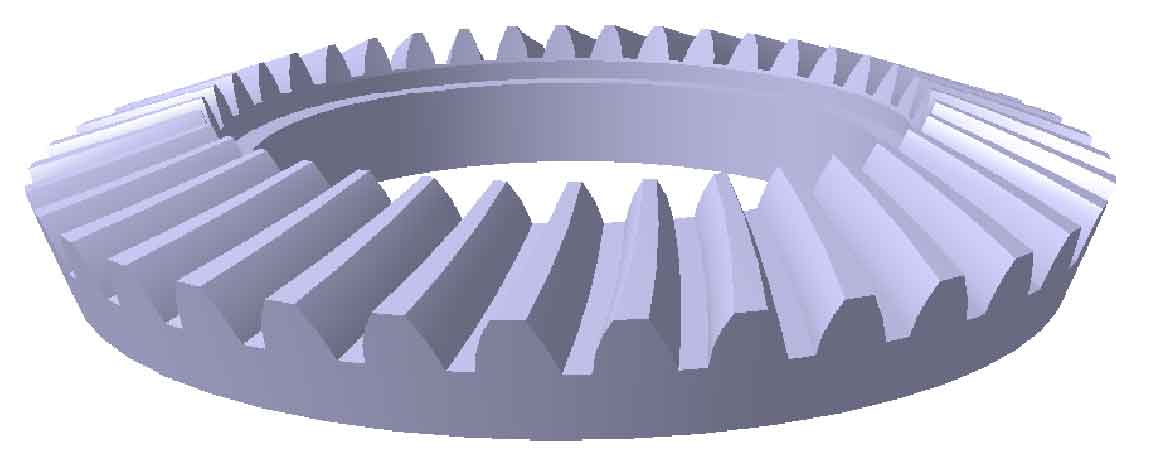
Precision forged bevel gear teeth can be directly used without machining, which puts forward higher requirements for surface quality and dimensional accuracy of bevel gear forgings. Therefore, before hot precision forging, the preform must be heated with less or no oxidation.
Because the medium frequency induction heating has the advantages of fast heating speed, good quality, small burning loss, simple operation, stable process, no pollution, and easy to realize mechanization and automation. The preform is heated by medium frequency induction heating without oxidation. The medium frequency induction heating furnace with frequency of 4000Hz and power of 250KW is selected according to the diameter range of preform from 40mm to 80mm.