Due to the different normal grinding depths and wheel speeds at different locations of the involute, the intensity of the grinding heat source varies at different locations of the involute.In combination with MALKIN’s research on grinding temperature field, the heat source intensity flowing into the workpiece during the forming grinding process can be written as follows:
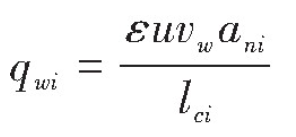
Where QWI is the intensity of the heat source at any position on the involute; e is the proportion of the heat source flowing into the workpiece and is generally acceptable0.55; LCI is the length of the grinding arc at any position on the involute; u is the specific energy for grinding, and
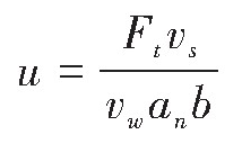
Where Ft is the tangential grinding force and B is the effective grinding width.
During grinding, grinding force can be divided into normal grinding force and tangential grinding force. According to MALKIN’s research on grinding force, the relationship between grinding forces is as follows:
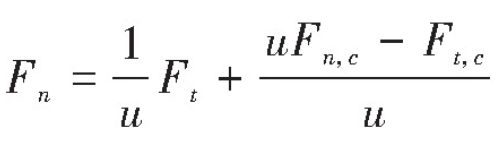
Where Fn is the normal grinding force, Fn, C is the normal cutting force and Ft, C is the tangential cutting force.
In the process of forming grinding, the contact between grinding wheel and workpiece can be assumed to be Hertzian contact of two surfaces. Therefore, an elliptical heat source distribution model is used as the heat source form of forming grinding in this paper, as shown in the figure.
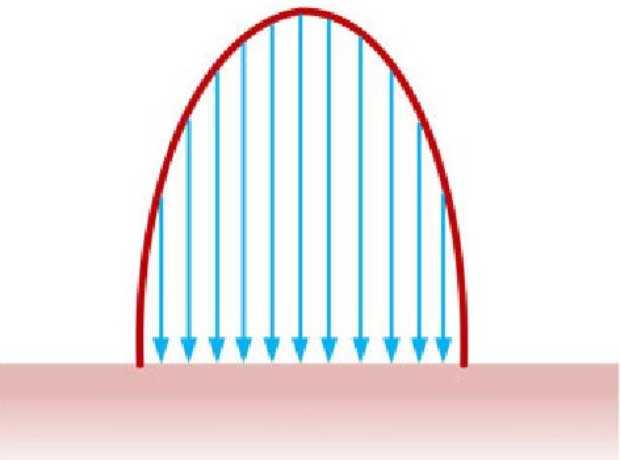
COMSOL Multiphysics @ commercial finite element software is used to simulate the residual stress on the tooth surface of the form grinding. COMSOL Multiphysics @ can effectively realize the quick solution of multi-physical field coupling, which is more suitable for the thermal coupling analysis of the form grinding simulation in this paper.The basic gear parameters used in the study in this paper are shown in Table 1. Firstly, a three-dimensional geometric model of the gear is established as shown in the figure.
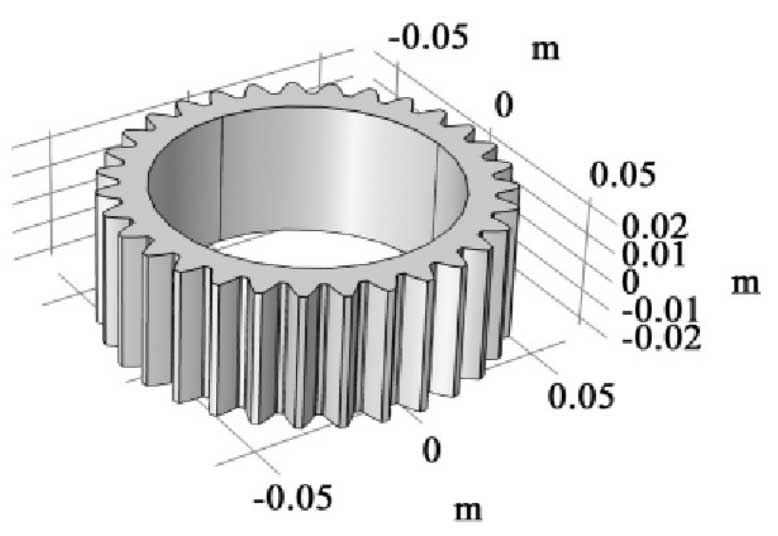
Forming grinding of gears is carried out in the grooves of two adjacent teeth and has symmetry. Therefore, in order to avoid wasting a lot of calculation resources due to the analysis of the entire gear, a single gear is selected for analysis.The individual teeth are meshed and the tooth surface simulated by grinding is refined as shown in the figure. The final complete mesh consists of 13,767 units.
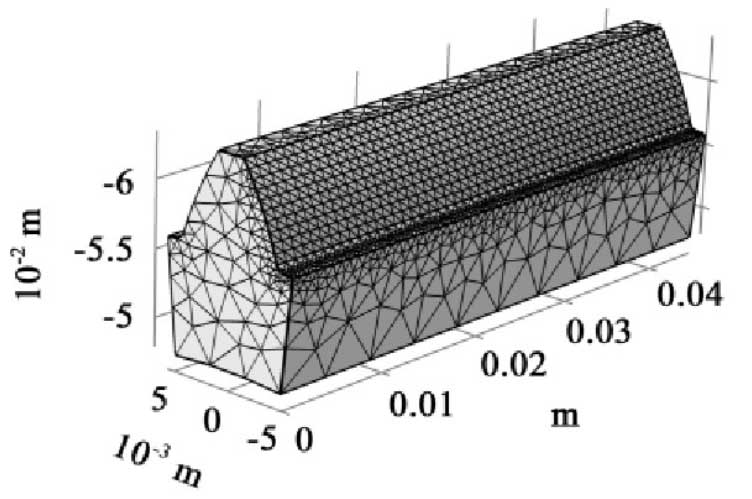
High grinding temperature occurs during grinding. Therefore, the cooling is performed with grinding fluid. In the simulation calculation, the cooling is usually simulated in the form of convection heat exchange coefficient. According to the grinding conditions shown in Table 2, the oil-based grinding fluid can be selected as the convection heat exchange coefficient.2.3X 105 (W/(m2_k)[14].It is assumed that sufficient grinding fluid exists in the grinding process and the grinding phase transition is ignored.The heat source strength and grinding force under this working condition are calculated and loaded on the tooth surface as a moving load. The residual stress field on the tooth surface formed under this working condition is simulated and calculated, and the residual stress cloud diagram of the tooth surface is obtained as shown in the figure.
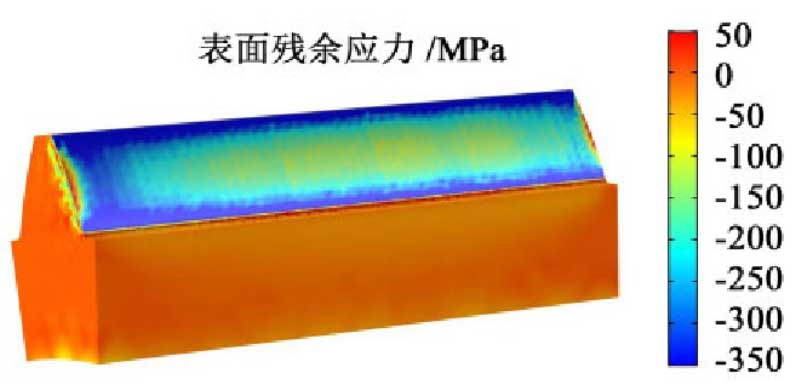
From the calculation results, it can be found that after the forming grinding, the residual stress on the tooth surface is between -350 ~ – 150 MPa, which is smaller than the initial residual compressive stress.The residual compressive stress at the center of the tooth surface of the grinded tooth surface is the smallest, which gradually increases from the center of the tooth surface to the outside, and reaches the maximum value near the top and the root of the tooth.The distribution of residual stress on the tooth surface shows the alternating distribution of tensile stress and compressive stress, from the surface to the sub-surface becomes tensile stress, and continues to reappear further.
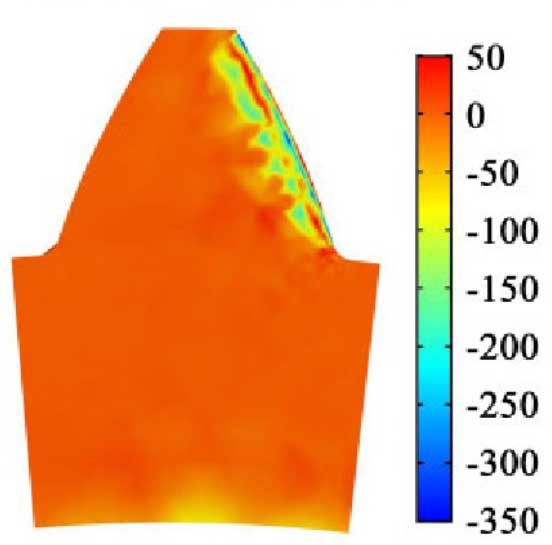