1. Introduction
Spiral bevel gears, also known as Gleason gears, have the characteristics of high transmission efficiency, compact structure, and stable transmission. They are widely used in high-speed and heavy-load equipment such as automobiles, construction machinery, aerospace, and ships. The strength and dynamic performance of spiral bevel gears are of great significance to ensure the smooth operation of mechanical equipment under complex working conditions and reduce vibration and noise.
2. Tooth Surface Modeling of Large and Small Wheels
2.1 Tooth Surface Equation of the Large Wheel
The right-handed large wheel is processed by the generating method, and the tooth surface is a part of the envelope surface of the tool cutting trajectory. By analyzing the processing process, it can be known that the cutter head rotates around the axis to form a cutting cone surface, and the indexing table and the tooth blank of the large wheel to be processed also rotate around the axis to form the tooth surface of the large wheel.
To illustrate the position of the large wheel cutter head, a coordinate system is established as shown in Figure 1. In the figure, is the center of the machine tool, is the center of the cutter head, the plane is contained in the plane where the tool tip is located (coinciding with the machine plane ), is the axial cutter position, and is the angular cutter position.
To illustrate the position of the large wheel blank, a coordinate system as shown in Figure 2 is established. In the figure, is the designed cone vertex of the blank, is the bed position, is the axial wheel position, and is the blank mounting angle.
The coordinate equation of the cutting cone surface is established as follows:
$r_{g1}(U_{g}, \theta_{g}) = \left[\begin{array}{c} (r_{G} \pm U_{g} \sin \alpha) \cos \theta_{g} \ (r_{G} \pm U_{g} \sin \alpha) \sin \theta_{g} \ -U_{g} \cos \alpha \ 1 \end{array}\right] $
where is the coordinate equation of the cutting cone surface, is the tool tip radius (as shown in Figure 4), and the “±” respectively represent the concave and convex surfaces of processing the large wheel.
The unit normal vector of the large wheel cutting cone surface can be expressed as:
$n_{g} = \left[\begin{array}{c} \cos \alpha \cos \theta_{g} \ \cos \alpha \sin \theta_{g} \ \pm \sin \alpha \end{array}\right] $
By performing coordinate transformation through Equation (3), the cutting cone surface equation can be transformed into the coordinate system fixed to the large wheel blank, and the tooth surface equation and the normal vector of the large wheel can be obtained.
In the analysis of the large wheel processing process, it can be known that there is no generating motion in the forming method, so takes zero, and the tooth surface equation only related to and is obtained.
2.2 Boundary Conditions
The surface determined by the tooth surface equation is a spatial surface with a complex geometric shape. The points required to construct the tooth surface of the spiral bevel gear must be within a specified range, so it is necessary to limit the range of the surface coordinate variables and . Through projection transformation, it can be known that the points on the tooth surface of the large wheel must be located in the planar quadrilateral composed of the tooth tip line, tooth root line, front cone surface, and back cone surface, as shown in Figure 5.
The coordinates of the projection point on the plane of the spatial surface point are calculated as follows:
where is the axial displacement, is the radial displacement, and is the normal displacement.
Based on this, it can be judged whether the points calculated by Equation (3) meet the boundary conditions, and then the ranges of the surface coordinate variables and can be obtained. Obviously, this tooth surface equation is a nonlinear equation, and the iterative algorithm is used to call the fsolve function in MATLAB to solve the discrete points of the tooth surface. The algorithm flow is shown in Figure 6.
2.3 Tooth Surface Equation of the Small Wheel
The left-handed small wheel is processed by the cutter tilt method, and the processing principle is basically similar to that of the right-handed large wheel. So the modeling process is similar to the above derivation. The positions of the cutter head and the wheel blank are shown in Figures 7 and 8. In the figures, is the center of the machine tool, is the center of the cutter head, is the angular velocity of the indexing table, is the indexing table rotation angle, and the definitions of other parameters are the same as those of the large wheel.
The tooth surface of the small wheel processed by the cutter tilt method is enveloped by the cutting cone surface of the cutter head, among which the indexing table rotation angle is constantly changing. From the meshing equation at the contact point, it can be known that the relative speed of the cutter head and the wheel blank is perpendicular to the normal vector , and the relationship is as follows:
Finally, the tooth surface equation of the small wheel is obtained, and the boundary conditions and solution methods are similar to the principle of the large wheel tooth surface.
3. Spiral Bevel Gear Modeling
Write the tooth surface equation and other calculation formulas of the right-handed large wheel and left-handed small wheel analyzed above into corresponding programs, and substitute the basic parameters of the spiral bevel gear pair (Table 1) and processing parameters (Table 2) into the program for operation.
Table 1: Basic Parameters of the Gear Pair
Parameter | Large Wheel | Small Wheel |
---|---|---|
Tooth Number | 33 | 28 |
Face Module (mm) | 4.8 | 4.8 |
Outer Cone Distance (mm) | 123.3 | 123.3 |
Tooth Width (mm) | 37 | 37 |
Tooth Top Height (mm) | 2.2 | 2.3 |
Tooth Root Height (mm) | 3.3 | 2.9 |
Pitch Cone Angle (°) | 49.4 | 40.2 |
Root Cone Angle (°) | 47.5 | 39.3 |
Face Cone Angle (°) | 52.5 | 43.1 |
Table 2: Processing Parameters
Parameter | Small Wheel | Large Wheel | ||
---|---|---|---|---|
Concave Surface | Convex Surface | Concave Surface | Convex Surface | |
Cutter Head Pressure Angle (°) | 20 | 20 | 20 | 20 |
Tool Tip Circular Radius (mm) | 1.8 | – | 2.2 | – |
Cutter Top Distance (mm) | – | – | 2.4 | – |
Radial Cutter Position (mm) | 93.9 | 93.8 | 92.9 | – |
Angular Cutter Position (°) | 48.4 | 45.5 | 49.3 | – |
Machine Tool Rolling Ratio | 2.2 | 2.3 | 1.3 | – |
Bed Position (mm) | 0.55 | -0.65 | 0 | – |
- Calculate the discrete points of the convex and concave surfaces of the large wheel according to Equation (3), as shown in Figure 9.
- Import the obtained discrete point data into the 3D modeling software SolidWorks in text format, use the obtained point cloud for 3D modeling, and complete the modeling by using commands such as curves and surfaces. Place the discrete points in the same coordinate system to generate the concave and convex surfaces of the large wheel, and use surface clipping and shearing the intersection surface to generate the tooth profile modeling of the large wheel. Array the tooth profiles to establish the 3D model of the large wheel of the spiral bevel gear, as shown in Figure 10.
- Similarly, establish the 3D model of the small wheel, assemble the gear pair according to the specified position by using the gear mating command in the mechanical mating, and use the interference inspection function in the SolidWorks software to visually and clearly observe whether the assembly of the spiral bevel gear is reasonable to avoid interference, providing good mating conditions for the next finite element dynamic contact analysis.
4. Finite Element Contact Analysis of Spiral Bevel Gear
4.1 Establishment of the Finite Element Analysis Model
Based on the ANSYS Workbench platform, the transient dynamics module is used to perform dynamic contact analysis of the spiral bevel gear. The main links include setting model material parameters, meshing, setting boundary conditions and contact relationships, and setting solution parameters. Transient dynamics aims to analyze the dynamic response of the structure under transient or steady loads, and its output results are the stress, strain, and displacement of the contact area changing with time. Nonlinear transient dynamics is used to analyze the contact process of the spiral bevel gear, and the commonly used contact analysis algorithm is the augmented Lagrangian method, which can reduce the contact pressure calculation penetration to an acceptable level.
- Set the model material parameters. Import the assembled model into the finite element software Workbench, set the material parameters according to the actual spiral bevel gear material 18Cr2Ni4WA, with an elastic modulus of , Poisson’s ratio , and density .
- Meshing. The accuracy and type of meshing directly determine the accuracy of the 3D model analysis results. Excessive mesh density will increase the calculation time and occupy a large amount of computer resources. In order to obtain accurate calculation results and improve calculation efficiency, a tetrahedral mesh is selected to divide the model, and the gear contact surface expected to mesh is locally refined. The mesh size of the refined part is 1 mm, and the mesh size of the non-refined part is 10 mm. The finite element mesh model is shown in Figure 11, with a total of 619,607 nodes and 418,275 elements.
- Set boundary conditions and contact relationships. During the operation of the spiral bevel gear pair, the motor applies a torque to the driving wheel to rotate around the central axis through the wheel shaft, and the driving wheel and the driven wheel mesh to drive the driven wheel to rotate around the central axis. The driven wheel not only has input torque but also has load. Therefore, the applied load is that the driving wheel rotates around the central axis at a speed of 600 r/min. In order to compare the influence of the load on the contact area, the resistance torques of the driven wheel are 30 N·m and 500 N·m respectively. Select the locally refined tooth surface as the contact area, set the large wheel as Contact, and the small wheel as Target, and select the augmented Lagrangian method as the contact algorithm. Considering the contact area as a type with friction, the friction coefficient is selected as 0.2 under normal working conditions. Use the finite element model simulation results to obtain the distribution value of the tooth surface stress during the meshing process and obtain the contact mark area. According to the actual working conditions, it is known that generally, two or more pairs of teeth of the spiral bevel gear mesh simultaneously during operation. In order to facilitate the observation of the stress area change situation, the simulation results of one pair of tooth surfaces at two different loads of 30 N·m and 500 N·m are taken for explanation. The driving wheel rotates clockwise, and the stress distribution of the instantaneous contact area of the working concave surface is obtained at three state moments of starting, middle, and exiting, and the tooth surface stress cloud diagram is shown in Figure 12.
- Solution settings. The parameter setting in the transient dynamics contact analysis is more important, and the parameter setting of the load step determines whether the nonlinear solution proceeds smoothly. After analysis and testing, the total load step time is set to 0.0125 s, the initial load sub-step is 50, the minimum load sub-step is 20, the maximum load sub-step is 3,000, the large deformation option is turned on, and the iterative algorithm is used for the transient solution of the nonlinear contact.
4.2 Simulation Results Analysis and Experimental Comparison
It can be seen from Figure 12 that as the spiral bevel gear pair rotates, the tooth surface contact area moves from the small end to the large end of the tooth. Due to the elastic deformation of the tooth surface, the contact area becomes larger with the increase of the load, but the overall contact trend does not change due to the change of the load. The contact area is distributed in the middle of the tooth surface and is smaller at the end and presents a jujube-shaped, forming a certain angle with the tooth surface direction. Through the calculation of the unit mesh, the contact area length is about 47% of the tooth length, and the height is about 60% of the full tooth height. The simulation results are basically consistent with the design results, indicating that the established model is accurate and reliable.
In order to further verify the correctness of the model and simulation results, a practical mating experiment is carried out on the ground spiral bevel gear. A 500 mm universal rolling inspection machine is used, as shown in Figure 13. Since the universal rolling inspection machine is used to check the overall contact mark distribution of the contact area, an appropriate load can achieve the experimental purpose, so the load is set to 30 N·m.
Adjust the installation position of the spiral bevel gear pair through tooth surface coloring to make it cooperate normally, start the machine, wait for the tooth surfaces to mesh normally, and observe the tooth surface contact situation after a certain period of movement, and obtain the contact mark on the concave surface of the large wheel as shown in Figure 14. By analyzing the contact marks in Figures 12 and 14, it is found that the finite element simulation and the experimental results are basically consistent, verifying the accuracy of the established model and the finite element contact analysis results. The contact marks obtained through simulation and experiments all meet the distribution range of the contact area in the design criteria, indicating that the designed and manufactured spiral bevel gears can meet the actual use requirements.
5. Conclusion
In this paper, the discrete points of the tooth surface are solved based on the forming principle of the spiral bevel gear, and a 3D model is established through the tooth point cloud, which improves the modeling accuracy. The finite element model is established by using the transient dynamics module in ANSYS Workbench, and the contact mark on the concave surface of the large wheel during the meshing process of the spiral bevel gear is extracted. Through analysis, it is found that the simulation results are accurate and reliable. The contact marks obtained through simulation and experiments all meet the requirements of the contact area in the design criteria, indicating that the designed and manufactured spiral bevel gears can meet the actual use requirements.
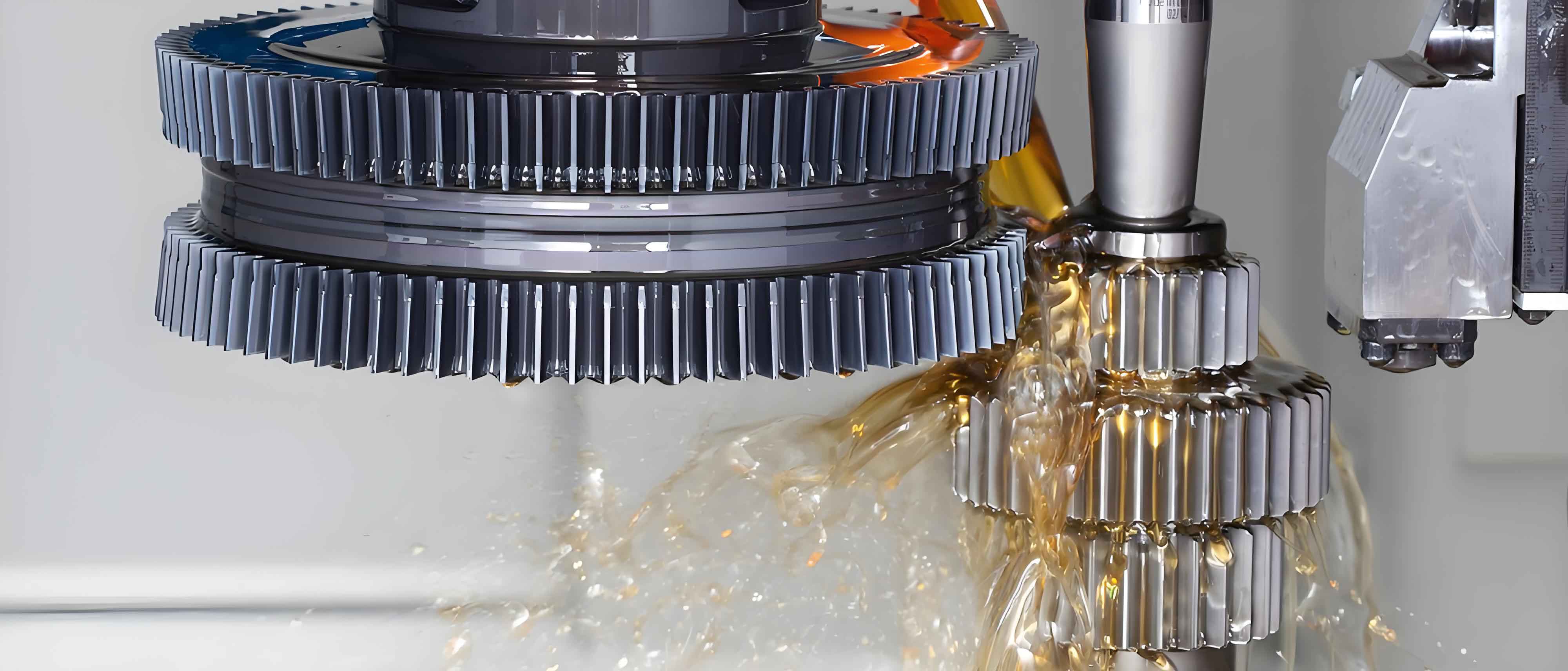