This article focuses on the performance analysis and test verification of spiral bevel gear transmission systems. It begins with an introduction to the importance and challenges of such systems, followed by a detailed discussion on the construction of mechanical models for key components. Static and dynamic characteristics analysis methods are presented, along with experimental verification. The research aims to provide a comprehensive understanding and accurate evaluation of spiral bevel gear transmission systems, facilitating their design optimization and performance improvement.
1. Introduction
1.1 Background and Significance
Spiral bevel gears are widely used in various industries due to their high transmission efficiency, strong bearing capacity, and compact structure. However, the complex geometry and meshing characteristics pose challenges in analyzing their performance accurately. Any malfunction in the gear transmission system can lead to significant production losses and safety hazards. Therefore, a detailed performance analysis is crucial for ensuring the reliable operation of machinery.
1.2 Research Objectives
The main objectives of this research are to develop accurate and efficient methods for analyzing the static and dynamic characteristics of spiral bevel gear transmission systems and to verify these methods through experimental tests. This involves understanding the mechanical behavior of each component, predicting the system’s response under different loads, and optimizing the design to reduce vibration and noise.
2. Mechanical Model Construction for Key Components
2.1 Transmission Shaft Model
- Entity Finite Element Model: The transmission shaft is modeled as an entity finite element to accurately represent its macroscopic stiffness characteristics. A proper mesh division is carried out, considering the installation positions of bearings and gears. Hexahedral elements are used to balance calculation accuracy and resource consumption.
| Parameter | Value |
|–|–|
| Elastic Modulus | |
| Poisson’s Ratio | 0.3 |
| Density | | - (Beam Element Model): For the beam element model, the Timoshenko beam element is selected considering the characteristics of the transmission shaft. The stiffness matrix of the beam element is derived based on its geometric and material properties.
2.2 Gear Pair Model
- (Equivalent Meshing Force): The meshing contact of the gear pair is simplified as an equivalent meshing force. The normal force at the meshing node is calculated based on the torque and power, and then decomposed into axial, radial, and tangential forces. The forces are then translated to the axis according to the parallel theorem, considering different offset conditions.
| Force Component | Calculation Formula |
|–|–|
| Tangential Force () | |
| Axial Force () | |
| Radial Force () | | - (Equivalent Rigid Body Model): The gear contact is further modeled as an equivalent rigid body, considering the meshing stiffness as a spring model and the energy dissipation as a damper. The gear is treated as a rigid disk with a certain moment of inertia to improve the analysis efficiency.
2.3 Bearing Model
- (Structural Characteristics and Force Analysis): The cone roller bearing is analyzed in terms of its structure and force distribution. The contact loads and deformations of the rolling elements are calculated, considering the effects of contact angles and offsets.
| Parameter | Description |
|–|–|
| Inner Ring Width () | Width of the bearing inner ring |
| Outer Ring Width () | Width of the bearing outer ring |
| Overall Installation Width () | Total width of the bearing installation | - (Stiffness Matrix Calculation): The stiffness matrix of the bearing is derived based on the force-displacement relationship. The nonlinearity and coupling of the stiffness in different directions are considered, and the stiffness matrix is calculated for a six-degree-of-freedom system.
3. Static Characteristics Analysis
3.1 Calculation of Meshing Misalignment
The meshing misalignment of the gear pair is defined as the relative displacement of the initial installation position due to the deformation of the transmission shaft and bearings under load. The calculation method is derived based on the geometric relationships of the gear axes and the deformation of the components.
3.2 Analysis Model Based on Entity Finite Element
- (Transmission Shaft Coupling Analysis Model): An entity finite element coupling analysis model of the transmission shaft is established. The model considers the meshing force, bearing stiffness matrix, and the geometric and material properties of the components. A proper mesh division is carried out to ensure the accuracy of the analysis.
| Analysis Step | Parameter | Value |
|–|–|–|
| Define Analysis Step | Time Length | 0.1 |
| | Calculation Step Length | 0.005 |
| Define Constraint | Number of Ground Springs per Guide Point | 5 | - (Tooth Loading Contact Analysis Model Considering Meshing Misalignment): Based on the meshing misalignment results, a tooth loading contact analysis model is constructed. The model adjusts the meshing position and 姿态 of the gears and analyzes the contact characteristics under load. A local mesh refinement strategy is used in the contact area to improve the calculation accuracy.
3.3 Instance Analysis and Result Comparison
- (Construction of Comparative Analysis Models): To verify the accuracy of the proposed method, comparative analysis models based on beam elements and full finite elements are constructed. The models are used to calculate the meshing misalignment, transmission error, and loading mark of the gear pair.
| Model Type | Advantage | Disadvantage |
|–|–|–|
| Beam Element Model | High calculation efficiency | Less accurate results |
| Full Finite Element Model | High accuracy | High resource consumption | - 结果对比 (Result Comparison): The results of the different models are compared in terms of meshing misalignment, loading mark, and transmission error. The entity finite element model shows good agreement with the full finite element model, with errors within a small range.
4. Dynamic Characteristics Analysis
4.1 Analysis Model Considering Meshing Stiffness
Based on the meshing stiffness of the gear pair, a dynamic analysis model of the transmission system is constructed. The model includes the transmission shaft beam element model, gear rigid disk model, and bearing stiffness matrix. The meshing stiffness is calculated using the finite element method.
4.2 Modal Analysis of the Transmission System Model
The modal analysis of the transmission system model is carried out to obtain the inherent frequencies and mode shapes of the system. The analysis considers the material damping and the meshing stiffness of the gears. The first 20 orders of inherent frequencies and mode shapes are presented.
4.3 (Harmonic Response Analysis)
The harmonic response analysis is performed to study the dynamic response of the transmission system under the excitation of the meshing force. The meshing force is transformed into a harmonic load using the Fourier transform, and the dynamic response is calculated using the modal superposition method. The vibration acceleration amplitude-frequency characteristics curves of the transmission shaft are obtained.
5. Test Experiment
5.1 Experiment Preparation
- (Experimental Object): The gear pair samples are prepared based on the theoretical spiral bevel gear model. The cutting and grinding parameters are adjusted according to the meshing misalignment results.
- (Experimental Scheme): The gear pair is installed and adjusted according to the meshing misalignment. The acceleration sensor and microphone are arranged to measure the vibration and noise of the gear pair during operation. A LabShop software is used for data acquisition and analysis.
- (Experimental Equipment): The experimental equipment includes a CNC rolling inspection machine, acceleration sensors, microphones, and a data acquisition card. The equipment is selected for its high sensitivity and stability.
5.2 Experiment Results
- (Experimental Results of Gear Pair Static Characteristics): The static characteristics of the gear pair, such as the contact mark and transmission error, are measured and compared with the theoretical results. The experimental results show good agreement with the theoretical results, validating the accuracy of the analysis model.
| Parameter | Experimental Value | Theoretical Value |
|–|–|–|
| Transmission Error (First Order Amplitude) | 47.22urad | 54.43urad | - (Experimental Results of Gear Pair Dynamic Characteristics): The dynamic characteristics of the gear pair, such as the vibration acceleration amplitude-frequency characteristics curves and the noise amplitude-frequency characteristics curves, are measured and compared with the theoretical results. The experimental results show good agreement with the theoretical results, validating the accuracy of the dynamic analysis model.
5.3 方案优化 (Scheme Optimization)
Based on the experimental results, an optimization scheme is proposed to improve the performance of the gear pair. The optimization scheme aims to make the load distribution on the tooth surface more uniform and reduce the amplitude during the meshing process. The optimized gear pair is tested again, and the results show an improvement in performance.
6. Conclusion and Outlook
6.1 Research Summary
This research has developed accurate and efficient methods for analyzing the static and dynamic characteristics of spiral bevel gear transmission systems. The methods have been verified through experimental tests, showing good agreement with the theoretical results. The research has provided a comprehensive understanding of the mechanical behavior of spiral bevel gear transmission systems and has facilitated their design optimization and performance improvement.
6.2 Future Research Directions
Future research can focus on improving the accuracy of the analysis methods, considering more complex factors such as time-varying stiffness and multiple contact nodes. The dynamic characteristics analysis can be extended to include other dynamic indicators, and the optimization scheme can be further refined to achieve better performance of the gear pair.
In conclusion, the research on spiral bevel gear transmission systems is of great significance for improving the performance and reliability of mechanical equipment. The methods and results presented in this article provide a valuable reference for future research and engineering applications.
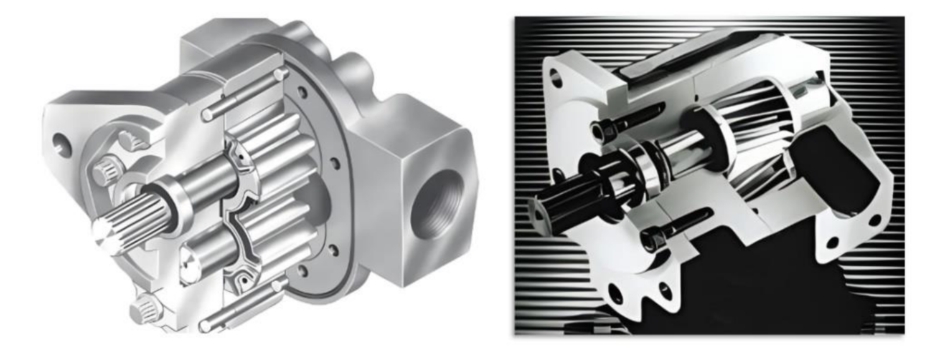