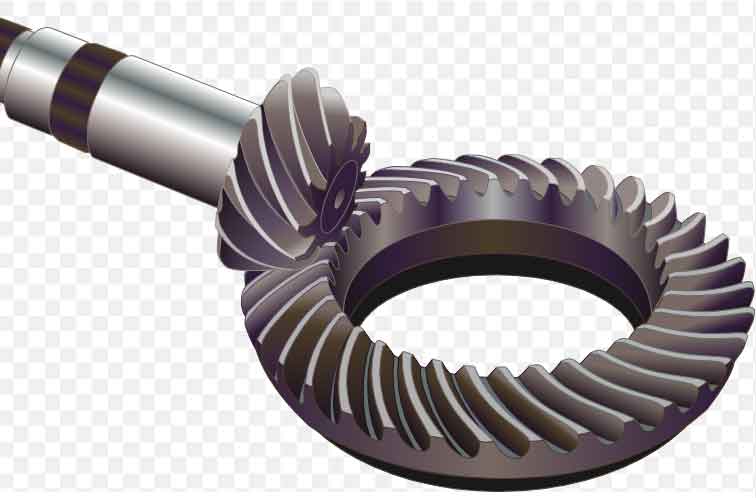
Spiral bevel gears are a specialized type of bevel gears that have helical teeth and are used to transmit power between intersecting shafts. They offer several advantages over straight bevel gears and are suitable for various applications in modern engineering. Advancements in design, manufacturing, and materials have further improved the performance and versatility of spiral bevel gears. Here’s an overview of the advancements and applications of spiral bevel gears in modern engineering:
Advancements:
1. Precision Manufacturing Techniques:
- Advanced manufacturing techniques such as CNC machining, gear grinding, and gear honing ensure high precision in spiral bevel gear production, resulting in accurate tooth profiles and improved gear performance.
2. Advanced Gear Design Software:
- The use of sophisticated gear design software allows engineers to optimize the gear geometry and tooth profiles, ensuring better load distribution and reducing stress concentrations.
3. Microgeometry Modifications:
- Microgeometry modifications, such as tooth crowning and lead corrections, optimize the contact patterns of spiral bevel gears, reducing noise, vibration, and wear.
4. Enhanced Materials and Heat Treatment:
- The selection of high-performance materials and advanced heat treatment processes improves the strength, durability, and wear resistance of spiral bevel gears.
5. Surface Coatings and Treatments:
- The application of specialized surface coatings and treatments enhances the gear’s surface hardness, reducing friction and improving the gear’s overall performance and durability.
6. Noise Reduction Techniques:
- Advancements in noise reduction techniques, such as adding vibration-damping materials or employing gear design optimizations to minimize resonances, result in quieter gear operation.
Applications:
1. Aerospace Industry:
- Spiral bevel gears are used in aircraft engines, helicopter transmissions, and flight control systems due to their high torque transmission capacity, smooth operation, and reliability.
2. Automotive Industry:
- They are employed in automotive differentials, axles, and steering systems, providing efficient power transmission and improved vehicle handling.
3. Marine Applications:
- Spiral bevel gears are used in marine propulsion systems, gearboxes, and steering mechanisms, ensuring precise and smooth power transmission for boats and ships.
4. Robotics and Automation:
- Spiral bevel gears find applications in robotic arms, automated machinery, and industrial robots, where precision motion control and efficient power transmission are essential.
5. Power Generation:
- They are used in power generation equipment, such as wind turbines and hydroelectric generators, to transfer power between shafts at high efficiency.
6. Heavy Machinery and Construction Equipment:
- Spiral bevel gears are employed in heavy machinery, mining equipment, and construction machinery, where they handle high loads and provide reliable power transmission.
7. Military and Defense:
- They are used in military vehicles, tanks, and gearboxes in defense applications, providing robust and reliable power transmission in demanding conditions.
8. Rail Transportation:
- Spiral bevel gears are used in rail transportation for applications such as locomotive power transmission and gearbox systems.
Advancements in spiral bevel gear technology have expanded their applications in modern engineering. Their high efficiency, smooth operation, and ability to handle high loads make them suitable for critical applications in various industries, including aerospace, automotive, robotics, power generation, and defense. The continuous development of design, manufacturing, and materials further enhances the performance and versatility of spiral bevel gears, solidifying their position as a key component in many advanced engineering systems.