Gear meshing and noise reduction are critical challenges in the design and operation of spiral bevel gears. Let’s explore some of the strategies used to tackle these challenges:
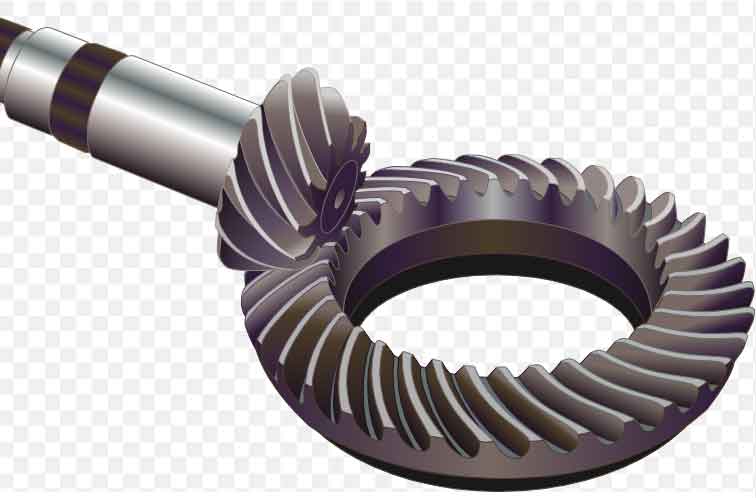
- Tooth Profile Optimization: The tooth profile plays a significant role in achieving smooth and efficient gear meshing. Engineers use advanced design techniques to optimize the tooth profile, such as modifying the shape, pressure angle, and tooth thickness distribution. These optimizations aim to minimize the impact of tooth engagement and improve load distribution, reducing noise and vibration.
- Spiral Angle Optimization: The spiral angle of spiral bevel gears affects how the teeth gradually engage during rotation. By carefully selecting the spiral angle, engineers can control the contact pattern and load distribution across the tooth face. This optimization helps to reduce localized stresses, improve load sharing, and minimize noise generation.
- Precision Manufacturing: High-precision manufacturing processes are essential to ensure accurate tooth geometry and minimize deviations from the design specifications. Advanced machining techniques, such as CNC milling and grinding, are employed to achieve tight tolerances and high surface finishes. Precision manufacturing helps to maintain proper gear meshing, reduce backlash, and mitigate noise issues.
- Gear Alignment: Proper alignment of spiral bevel gears is crucial to achieve smooth meshing and reduce noise. Misalignment can lead to uneven loading, increased backlash, and accelerated wear. Precise alignment during assembly and regular maintenance checks can help minimize gear misalignment and optimize gear performance.
- Lubrication and Surface Treatment: Lubrication plays a vital role in reducing friction and wear between the gear teeth. Proper selection and application of lubricants help to maintain a thin film of oil between the contacting surfaces, minimizing noise generation. Additionally, surface treatments like shot peening or surface coatings can improve the surface hardness and reduce the risk of micro-pitting and surface fatigue, contributing to noise reduction.
- Vibration and Noise Analysis: Advanced analytical techniques, such as finite element analysis (FEA) and computational fluid dynamics (CFD), are employed to study the vibration characteristics and noise generation in spiral bevel gears. By analyzing the gear dynamics, engineers can identify potential issues and make design modifications to mitigate noise problems.
- Material Selection: The choice of materials for spiral bevel gears can significantly impact their noise performance. Materials with high strength, good damping properties, and low resonance frequencies are preferred to reduce noise and vibration levels. Additionally, the use of composite materials or alternative alloys can provide noise reduction benefits in certain applications.
By integrating these strategies into the design, manufacturing, and maintenance processes, engineers can tackle the challenges associated with gear meshing and noise reduction in spiral bevel gears. This allows for the development of quieter, more efficient, and reliable gear systems.