Introduction
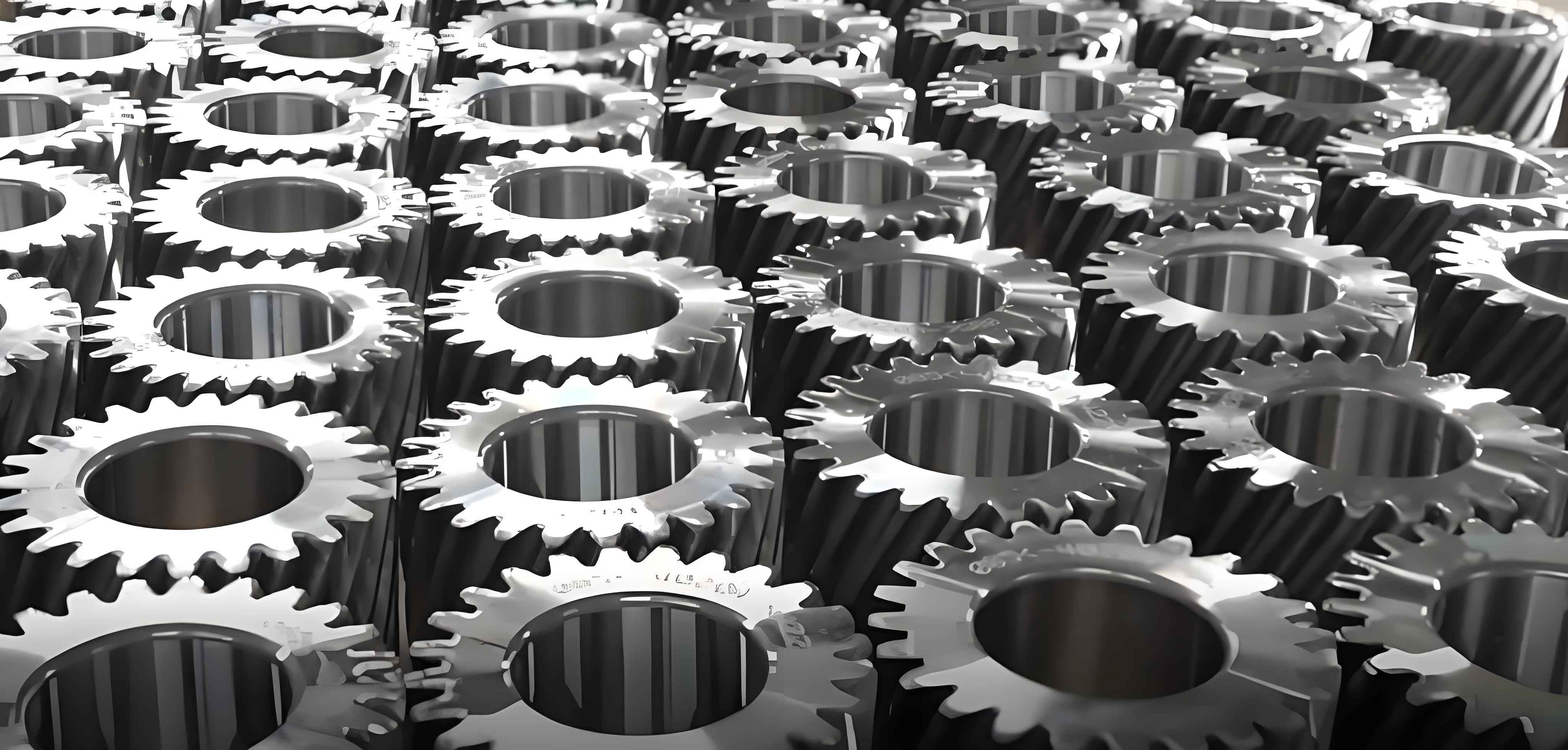
Spur gear is crucial component in the engineering of electric vehicles (EVs). They play a vital role in the transmission of power from the electric motor to the wheels, facilitating efficient and smooth vehicle operation. This article delves into the importance, functionality, and applications of spur gear in electric vehicle engineering.
What is a Spur Gear?
The spur gear is a type of gear with straight teeth mounted on a parallel shaft. These gears are the most common type used in various mechanical applications, including electric vehicles. The primary function of spur gear is to transmit motion and power between parallel shafts.
Importance of Spur Gear in Electric Vehicles
- Efficiency: Spur gear is known for their high efficiency in power transmission. This efficiency is crucial in electric vehicles to maximize the energy obtained from the battery.
- Simplicity: The straightforward design of spur gear makes them easy to manufacture and maintain. This simplicity translates to cost savings in the production and upkeep of electric vehicles.
- Reliability: Spur gear provide consistent performance and have a long lifespan, ensuring the reliability of the electric vehicle’s transmission system.
Applications of Spur Gear in Electric Vehicles
Spur gear is used in several key areas within electric vehicles:
- Transmission Systems: Spur gear is integral in the main transmission systems, helping to transfer power from the electric motor to the wheels.
- Auxiliary Systems: They are also used in auxiliary systems such as steering mechanisms, where precise control is essential.
- Power Steering: Spur gear facilitate the functioning of electric power steering systems, providing drivers with the ability to steer the vehicle with minimal effort.
- Regenerative Braking: In regenerative braking systems, spur gear help to convert kinetic energy into electrical energy, which is then stored in the battery for later use.
Design Considerations for Spur Gear in Electric Vehicles
When designing spur gear for electric vehicles, several factors must be considered to ensure optimal performance and longevity:
- Material Selection: The choice of material is critical. High-strength alloys and composites are commonly used to enhance durability and reduce weight.
- Gear Ratios: The gear ratio must be carefully calculated to balance speed and torque, providing the best possible performance for the electric vehicle.
- Lubrication: Proper lubrication is essential to minimize friction and wear, extending the life of the spur gear.
- Noise Reduction: Electric vehicles are known for their quiet operation, so reducing gear noise is a significant design consideration. This can be achieved through precise manufacturing and the use of noise-dampening materials.
Comparative Analysis: Spur Gear vs. Other Gear Types
Feature | Spur Gear | Helical Gear | Bevel Gear |
---|---|---|---|
Tooth Design | Straight | Angled | Conical |
Efficiency | High | Moderate | Moderate |
Manufacturing | Simple | Complex | Complex |
Noise Level | Moderate to High | Low | Low to Moderate |
Cost | Low | High | High |
Load Capacity | Moderate | High | High |
Application in EVs | Transmission, Power Steering | Transmission, Differential | Differential, Transfer Case |
Advantages of Using Spur Gear in Electric Vehicles
- High Efficiency: Spur gear provide efficient power transfer, which is crucial for maximizing the range of electric vehicles.
- Cost-Effective: The simple design and manufacturing process make spur gear cost-effective option for electric vehicle manufacturers.
- Ease of Maintenance: The straightforward design of spur gear allows for easy maintenance and replacement, reducing downtime and repair costs.
- Robustness: Spur gear is known for their durability and reliability, ensuring consistent performance over the lifespan of the vehicle.
Challenges and Solutions
While spur gear offer numerous advantages, there are also challenges that engineers must address:
- Noise and Vibration: The meshing of straight teeth can generate noise and vibration. Solutions include using precision manufacturing techniques and employing noise-dampening materials.
- Wear and Tear: Spur gear is subject to wear and tear over time. This can be mitigated through the use of high-quality materials and proper lubrication.
Future Trends in Spur Gear Design for Electric Vehicles
- Advanced Materials: The development of new materials, such as carbon fiber composites, promises to enhance the strength and reduce the weight of spur gear.
- Additive Manufacturing: Also known as 3D printing, additive manufacturing allows for the creation of complex gear geometries that were previously impossible to produce with traditional methods.
- Smart Lubrication Systems: The integration of smart lubrication systems can ensure optimal lubrication at all times, reducing wear and extending the lifespan of spur gear.
- Noise Reduction Technologies: Ongoing research into noise reduction technologies aims to further decrease the noise generated by spur gear, enhancing the overall driving experience of electric vehicles.
Conclusion
Spur gear play a pivotal role in the engineering of electric vehicles. Their efficiency, simplicity, and reliability make them an ideal choice for various applications within the vehicle. As technology advances, the design and manufacturing of spur gear continue to evolve, promising even greater performance and efficiency in the future of electric vehicle engineering.
Summary Table: Key Points about Spur Gear in Electric Vehicles
Key Point | Description |
---|---|
Efficiency | High efficiency in power transmission |
Simplicity | Easy to manufacture and maintain |
Reliability | Consistent performance and long lifespan |
Applications | Transmission systems, power steering, regenerative braking |
Design Considerations | Material selection, gear ratios, lubrication, noise reduction |
Advantages | Cost-effective, ease of maintenance, robustness |
Challenges | Noise and vibration, wear and tear |
Future Trends | Advanced materials, additive manufacturing, smart lubrication, noise reduction |
In conclusion, the integration of spur gear in electric vehicle engineering is indispensable for ensuring efficient power transmission, reliable operation, and cost-effectiveness. With continuous advancements in materials and manufacturing techniques, spur gear will continue to be a fundamental component in the development of high-performance electric vehicles.