Scholars at home and abroad have also done a lot of research and Analysis on the meshing impact of gear teeth. Yaowenxi and others have studied the spur gear meshing impulse excitation by using the analytical method, and given the relationship between the tooth error, tooth deformation, tooth surface load and the meshing impact time, meshing impact force and meshing impulse, The meshing impulse is the integral of the meshing force in the action time. Therefore, the meshing impulse is the function of the above factors, which provides conditions for the further study of the vibration and noise of spur gears.
By analyzing the external meshing mechanism of spur gear transmission line, zhouchangjiang builds the calculation model of system equivalent error and tooth comprehensive deformation along the direction of meshing cooperation line, and deduces the calculation formula of the maximum impact force of the external meshing impact point according to the spur gear meshing principle, tooth comprehensive deformation and load history curve:
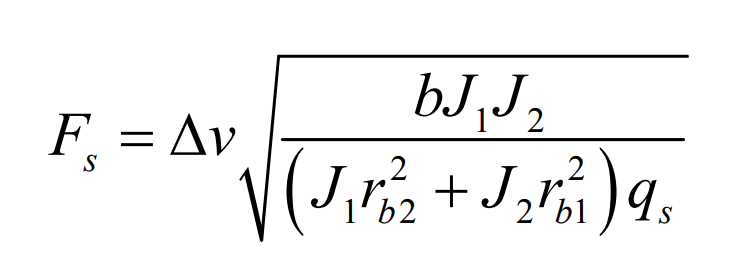
Where:
J1 (J2) – moment of inertia of the driving (driven) wheel;
RB1 (B2 R) – base circle radius of the driving (driven) wheel;
Δ V – speed difference between the meshing point of the driving and driven wheels;
QS — flexibility of initial meshing point of spur gear.
Tang Jinyuan et al. Built a spur gear transmission model based on the relevant theory of contact dynamics, put forward the concept of meshing contact impact of spur gear transmission, studied the tooth contact impact phenomenon caused by different speeds at the meshing points during spur gear transmission, established a mathematical model of spur gear meshing contact impact and gave a solution algorithm, and analyzed the effects of different impact speeds and impact positions on impact resultant force and impact time, The impact position, impact velocity and maximum impact force are calculated by analytical method. The research results show that the impact speed and impact position have a great impact on the meshing impact force and meshing impact time. Figure 1 shows the change curve of impact meshing force and speed.
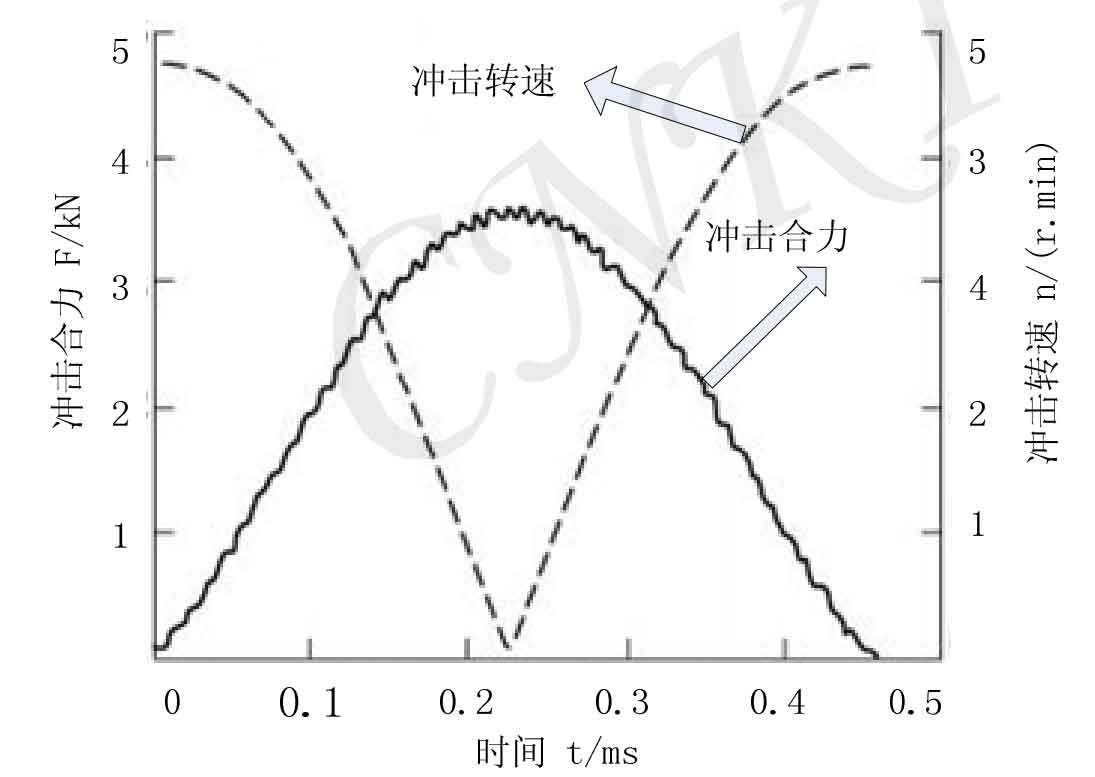
With the help of finite element software, Liu Wen et al. Established the dynamic finite element analysis model of spur gear transmission system including spur gear, bearing, transmission shaft and box by using rod element, tetrahedron element and spring element, and analyzed the vibration mode of spur gear transmission system, vibration speed and dynamic stress under the impact load of double half sine acceleration. Finally, considering the strength criterion, the impact resistance of spur gear transmission system is analyzed. Lintengjiao et al. Calculated the meshing in and meshing out performance of hypoid gear under the condition of load by using the tooth load contact analysis program, analyzed and obtained the load distribution of each tooth during load meshing, analyzed the acceleration impact and sudden load impact of hypoid gear transmission by using the finite element method of dynamic contact problem, and carried out numerical simulation, The influence of spur gear backlash on meshing impact characteristics is analyzed. Shaoninping, shenyunwen, etc. analyzed the impact of spur gear machining error and elastic deformation on spur gear meshing impact according to the spur gear meshing principle, obtained the mathematical expressions of impact speed and impact action time, and analyzed the relationship between the sound pressure value and sound radiation power and other acoustic characteristics during spur gear meshing impact in combination with acoustic theory, as shown in Figure 2:
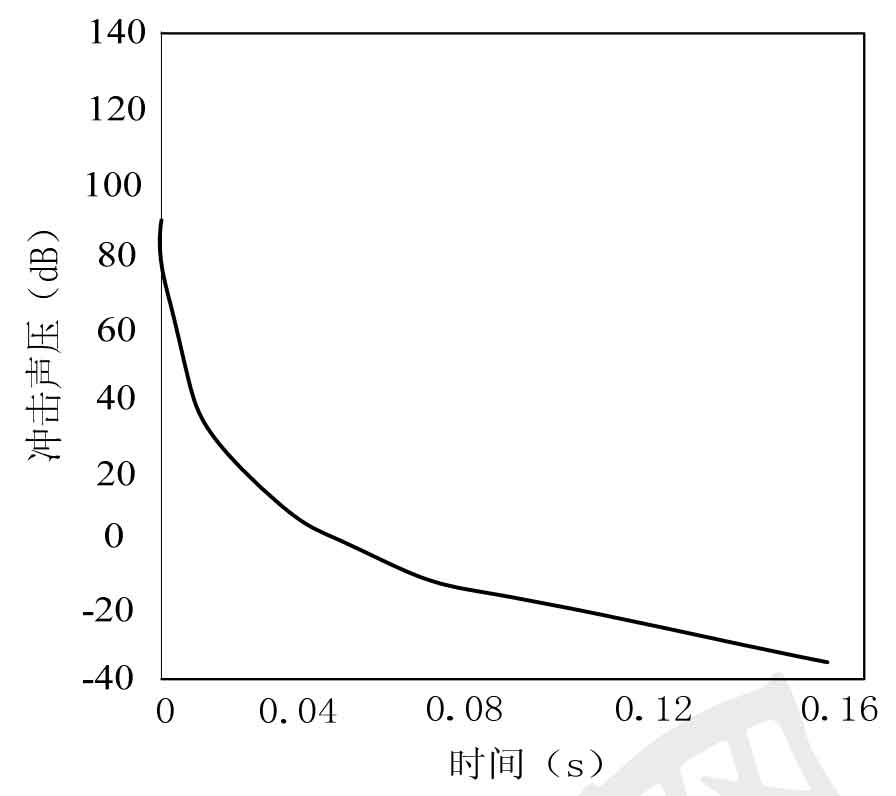
A. Bjae et al. Used the finite element method to consider the dynamic contact and tooth impact, developed a two-dimensional finite element solver, and analyzed the load impact and dynamic stress of planetary gear transmission. Parker used the finite element method to analyze the contact of spur gears and calculate the dynamic meshing force in the meshing process. Howard used the finite element method to calculate the meshing stiffness in order to explore the influence of spur gear friction on the dynamic characteristics. R. I. Raja Hamzah and D. MBA used high frequency acoustic emission technology to monitor the operation of spur gears. The results showed that the running speed of spur gears had a great impact on the dynamic meshing characteristics such as vibration and oil film thickness under load conditions. Lassaad walha et al. Built a two-stage spur gear pair dynamic model considering the spur gear tooth side clearance and time-varying meshing stiffness. In the model, the moment of inertia of the transmission shaft, bearing and load were considered at the same time. The dynamic equation was solved by simplifying the nonlinear problem into a linear problem. Figure 3 shows the angular velocity fluctuation curve of the transmission system under linear and nonlinear conditions.
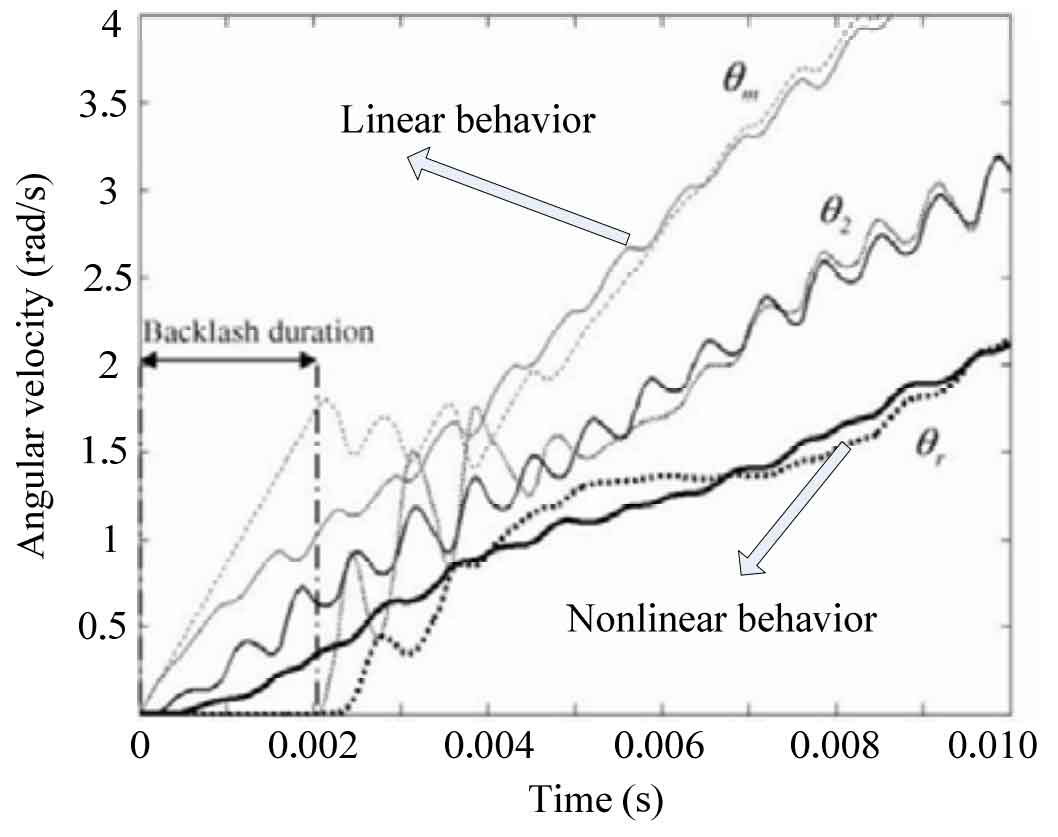
Yongjun Shen et al. Used the harmonic balance method to solve the nonlinear dynamic meshing characteristics of spur gear system, obtained the general solution, and analyzed the difference between multi-order frequency response and single-order frequency response of the system.