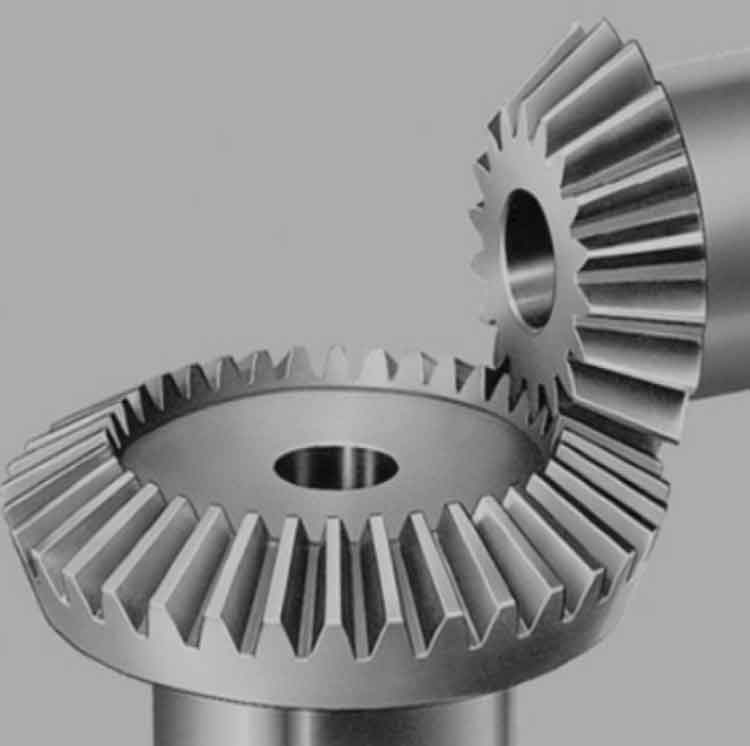
Proper lubrication is crucial for enhancing the lifespan and efficiency of straight bevel gears. Lubrication serves several essential functions, including reducing friction, dissipating heat, preventing wear, and protecting against corrosion. Effective lubrication minimizes power losses and extends the gear’s operational life. Here are some considerations for straight bevel gear lubrication to enhance their lifespan and efficiency:
1. Lubricant Selection:
- Choosing the right lubricant is critical. Factors such as gear design, operating conditions (load, speed, temperature), and the environment must be considered.
- High-quality gear oils with proper viscosity, additives, and EP (extreme pressure) properties are typically recommended for straight bevel gears.
2. Lubricant Viscosity:
- The lubricant’s viscosity should match the gear’s operating conditions. Too high viscosity can cause excessive friction and power loss, while too low viscosity may lead to inadequate lubrication and wear.
3. Lubrication Method:
- Splash lubrication is commonly used for straight bevel gears in enclosed gearboxes, where the gears are partially submerged in the lubricant.
- For exposed gears, oilers or spray systems may be used to deliver lubricant directly to the gear teeth.
4. Lubricant Flow:
- Adequate lubricant flow is essential for proper lubrication. Ensuring that the lubricant reaches all critical points and gear teeth is crucial for reducing wear and preventing damage.
5. Lubricant Contamination Control:
- Proper filtration and maintenance of the lubricant system are vital to prevent contamination by dirt, debris, and water.
- Contaminated lubricant can accelerate wear and lead to premature gear failure.
6. Lubricant Change and Inspection Intervals:
- Regular lubricant inspection and change intervals must be followed to maintain the lubricant’s effectiveness.
- Monitoring the lubricant condition can help identify potential issues early and prevent costly gear damage.
7. Lubricant Additives:
- Lubricant additives, such as EP additives and anti-wear agents, enhance the lubricant’s performance under high-pressure and high-temperature conditions.
8. Lubricant Compatibility:
- Ensure that the selected lubricant is compatible with the gear material to prevent chemical reactions that may lead to surface damage.
9. Temperature Considerations:
- The operating temperature of the gear system affects the lubricant’s performance.
- Extreme temperatures can lead to oil breakdown, affecting lubricity and causing premature wear.
10. Lubrication Training and Maintenance:
- Proper training of maintenance personnel on lubrication procedures is essential to ensure effective gear lubrication.
- Regular maintenance checks should be performed to monitor lubricant levels and condition.
By paying close attention to lubrication practices, gear designers and maintenance teams can enhance the lifespan and efficiency of straight bevel gears, leading to smoother operation, reduced wear, and overall improved performance of the gear system.