Introduction
Gear Shaft components are essential in a variety of mechanical systems, transferring torque and rotation between different parts. The performance and longevity of Gear Shaft components are significantly influenced by their surface finish. Surface finishing methods are used to enhance the properties of Gear Shaft components, leading to improved performance, reduced wear, and increased durability. This article explores various surface finishing methods and their benefits for Gear Shaft components.
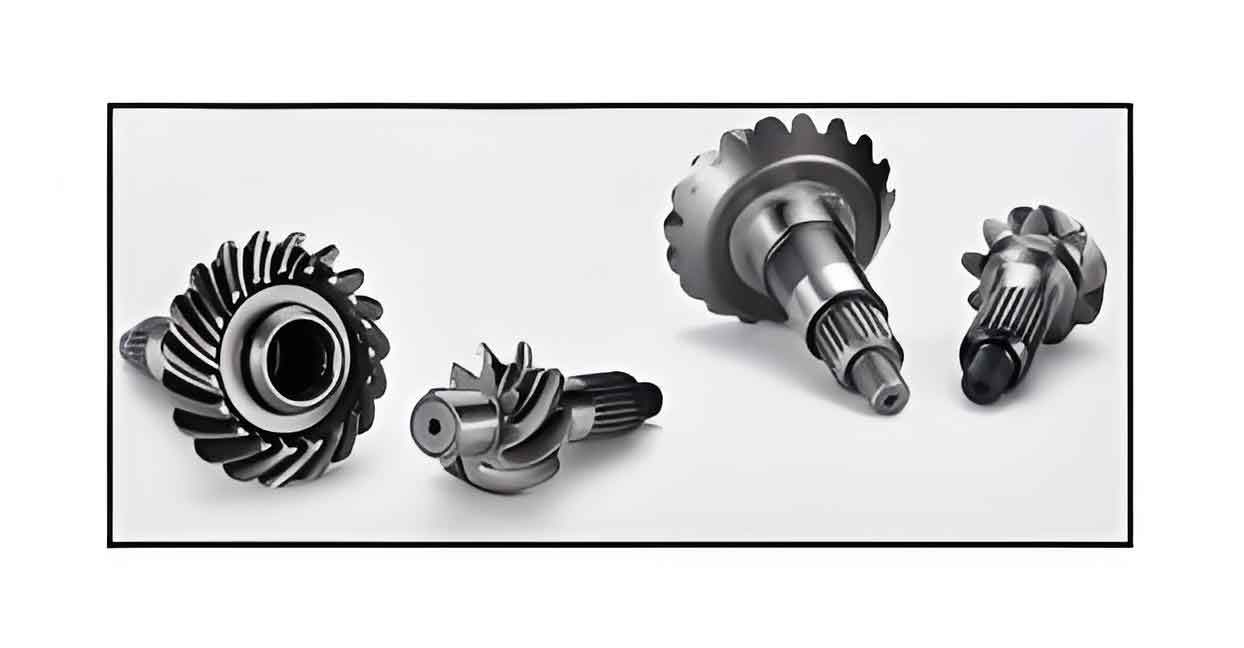
Importance of Surface Finishing for Gear Shaft
Surface finishing processes improve the physical and mechanical properties of Gear Shaft components, enhancing their ability to perform under demanding conditions. A high-quality surface finish can reduce friction, wear, and fatigue, leading to more reliable and efficient Gear Shaft operation.
Key Benefits of Surface Finishing for Gear Shaft:
- Reduced Friction:
- Enhances efficiency by minimizing resistance between moving parts.
- Increased Wear Resistance:
- Extends the lifespan of Gear Shaft components by reducing surface degradation.
- Improved Fatigue Strength:
- Enhances the ability to withstand cyclic loading without failure.
- Corrosion Resistance:
- Protects Gear Shaft components from environmental damage.
- Enhanced Aesthetics:
- Improves the visual appearance of Gear Shaft components.
Surface Finishing Methods for Gear Shaft
Various surface finishing methods can be applied to Gear Shaft components, each offering specific benefits tailored to different applications. Here are some common surface finishing methods:
1. Grinding
Grinding is a machining process that uses an abrasive wheel to remove material from the surface of the Gear Shaft, creating a smooth and precise finish.
Process:
- Preparation:
- The Gear Shaft is securely held in place.
- Grinding:
- An abrasive wheel removes material to achieve the desired surface finish.
- Inspection:
- The finished Gear Shaft is inspected for surface quality and dimensional accuracy.
Benefits:
- High precision and smooth surface finish.
- Improved dimensional accuracy and tight tolerances.
2. Polishing
Polishing uses abrasive compounds to produce a smooth and shiny surface on the Gear Shaft, enhancing its appearance and reducing friction.
Process:
- Abrasive Polishing:
- Sequential application of finer abrasives to achieve a smooth surface.
- Buffing:
- Using a soft cloth and polishing compound to achieve a high gloss finish.
Benefits:
- Enhanced aesthetic appeal.
- Reduced friction and wear.
3. Shot Peening
Shot peening involves bombarding the surface of the Gear Shaft with small spherical media (shots) to induce compressive stress, improving fatigue strength and resistance to cracking.
Process:
- Preparation:
- The Gear Shaft is cleaned and prepared for shot peening.
- Peening:
- The Gear Shaft surface is bombarded with shots at high velocity.
- Post-Peening Inspection:
- The treated Gear Shaft is inspected for surface quality.
Benefits:
- Increased fatigue strength.
- Improved resistance to stress corrosion cracking.
4. Hard Chrome Plating
Hard chrome plating involves electroplating a layer of chromium onto the Gear Shaft surface to enhance hardness, wear resistance, and corrosion resistance.
Process:
- Preparation:
- The Gear Shaft is cleaned and pre-treated.
- Electroplating:
- Chromium is electroplated onto the Gear Shaft surface.
- Post-Plating Inspection:
- The plated Gear Shaft is inspected for coating quality and thickness.
Benefits:
- Enhanced hardness and wear resistance.
- Improved corrosion resistance.
5. Anodizing
Anodizing is an electrochemical process that converts the surface of the Gear Shaft into a durable, corrosion-resistant oxide layer, commonly used for aluminum Gear Shaft components.
Process:
- Preparation:
- The Gear Shaft is cleaned and placed in an electrolyte solution.
- Anodizing:
- An electric current is passed through to form an oxide layer.
- Sealing:
- The oxide layer is sealed to enhance durability.
Benefits:
- Increased corrosion resistance.
- Improved surface hardness.
Comparison of Surface Finishing Methods for Gear Shaft
Method | Process | Benefits | Applications |
---|---|---|---|
Grinding | Abrasive wheel removes material | High precision, smooth surface finish | Precision engineering, automotive |
Polishing | Sequential abrasive application, buffing | Enhanced aesthetics, reduced friction | Aerospace, automotive, industrial |
Shot Peening | Surface bombarded with spherical media | Increased fatigue strength, resistance to cracking | Heavy machinery, aerospace |
Hard Chrome Plating | Electroplating of chromium layer | Enhanced hardness, wear resistance, corrosion resistance | Industrial machinery, automotive |
Anodizing | Electrochemical conversion to oxide layer | Increased corrosion resistance, improved hardness | Aluminum components, aerospace |
Applications of Surface-Finished Gear Shaft
Surface-finished Gear Shaft components are used in various industries where durability, performance, and reliability are critical. The choice of surface finishing method depends on the specific application requirements.
1. Automotive Industry
In the automotive industry, Gear Shaft components must withstand high loads and wear. Surface finishing methods like grinding and hard chrome plating are commonly used.
Benefits:
- Enhanced wear resistance for longer service life.
- Improved performance under high torque and stress.
2. Aerospace Industry
Aerospace applications require Gear Shaft components with high precision and fatigue strength. Shot peening and polishing are often used.
Benefits:
- Increased fatigue strength for reliable performance.
- Smooth surface finish for reduced friction.
3. Industrial Machinery
Industrial machinery demands Gear Shaft components that can handle heavy loads and continuous operation. Surface finishing methods like hard chrome plating and grinding are popular choices.
Benefits:
- Increased durability and wear resistance.
- Reduced maintenance and downtime.
4. Precision Engineering
In precision engineering, Gear Shaft components require high accuracy and minimal friction. Polishing and grinding provide the necessary surface finish.
Benefits:
- Precision and reliability in high-performance applications.
- Reduced friction for smooth operation.
Best Practices for Surface Finishing Gear Shaft
To achieve optimal results, certain best practices should be followed during the surface finishing of Gear Shaft components.
1. Material Selection
Choose materials that respond well to surface finishing processes, such as alloy steels, stainless steels, and aluminum.
2. Process Control
Maintain precise control over process parameters such as temperature, pressure, and time to ensure consistent results.
3. Quality Inspection
Conduct thorough inspections before and after surface finishing to ensure the Gear Shaft meets the required specifications and standards.
4. Post-Finishing Processes
Implement post-finishing processes like cleaning, sealing, and coating to enhance the properties of the surface-finished Gear Shaft.
Common Surface Finishing Defects and Solutions
Defect | Cause | Solution |
---|---|---|
Surface Cracking | Excessive stress during finishing | Optimize process parameters to reduce stress |
Uneven Finish | Inconsistent application of finishing methods | Ensure uniform application and process control |
Poor Adhesion | Inadequate surface preparation | Improve cleaning and preparation methods |
Surface Contamination | Contaminants during finishing process | Implement strict cleanliness protocols |
Conclusion
Surface finishing is a critical process in enhancing the performance and durability of Gear Shaft components. By understanding and applying the appropriate surface finishing methods, manufacturers can significantly improve the hardness, strength, and wear resistance of Gear Shaft components. This results in increased operational efficiency, reduced maintenance costs, and extended service life. Ongoing advancements in surface finishing technologies and practices continue to push the boundaries of Gear Shaft performance, contributing to the overall reliability and success of mechanical systems across various industries.