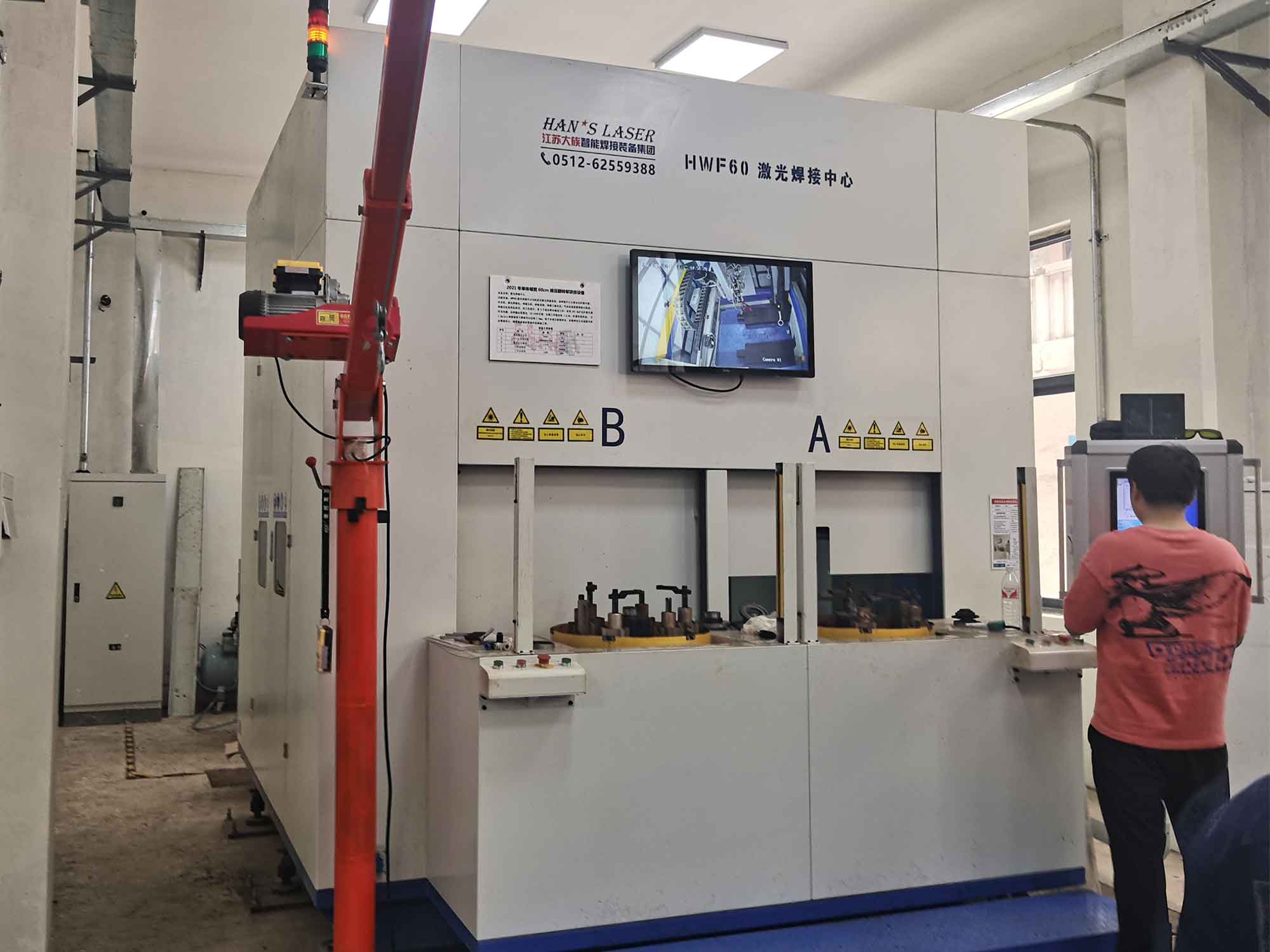
ZHY Gear Manufacturer, like others in the industry, can benefit significantly from adopting and adapting to technological advancements. Here are some of the key technological trends and innovations that could reshape gear manufacturing at ZHY:
ZHY Gear
China Leading Engineer Team. 40+ Years' Experience of Gear Manufacture!
1. Advanced Materials
- High-Performance Alloys and Composites: Utilizing advanced materials such as ultra-high-strength steel, titanium alloys, and carbon fiber composites can lead to gears that are lighter, more durable, and capable of operating under higher stresses and temperatures.
- Surface Treatments: Techniques like cryogenic treatment and advanced coatings (e.g., diamond-like carbon) can significantly enhance the wear resistance and lifespan of gears.
2. Additive Manufacturing (3D Printing)
- Rapid Prototyping: 3D printing allows for the quick production of prototype gears, enabling faster iteration and testing of new designs.
- Complex Geometries: Additive manufacturing enables the creation of gears with complex geometries that are difficult or impossible to achieve with traditional methods, potentially leading to better performance and efficiency.
- Customization and On-Demand Manufacturing: This technology facilitates the economical production of small batches of customized gears, reducing inventory costs and waste.
3. Precision Machining Technologies
- 5-Axis CNC Machining: This technology allows for more complex and precise gear shapes, improving the efficiency and noise performance of gear systems.
- Laser Cutting and Engraving: These methods provide high precision in finishing gear teeth and can be used to mark gears for tracking and quality control.
4. Automation and Robotics
- Automated Assembly Lines: Implementing robotic systems in assembly processes can increase production speed, consistency, and safety.
- Collaborative Robots (Cobots): These robots work alongside human operators to enhance productivity and reduce strain or injury risk in repetitive tasks.
5. Internet of Things (IoT) and Industry 4.0
- Smart Manufacturing: Integrating IoT sensors into gear manufacturing equipment can lead to real-time data collection and monitoring, optimizing maintenance schedules and minimizing downtime.
- Predictive Maintenance: Using machine learning algorithms to analyze data from sensors can predict equipment failures before they occur, significantly reducing repair costs and production delays.
6. Digital Twin Technology
- Simulation and Optimization: Digital twins simulate the manufacturing process and gear performance, allowing engineers to optimize designs and processes without physical trials.
- Lifecycle Management: Digital twins can also track the performance of gears throughout their operational life, gathering data that can be used to improve future designs.
7. Artificial Intelligence and Machine Learning
- Quality Control: AI can analyze images and data from the production line to identify defects or deviations in gear quality, ensuring products meet stringent standards.
- Supply Chain Optimization: AI and machine learning algorithms can optimize inventory management, predict supply chain disruptions, and suggest corrective actions.
8. Sustainable Manufacturing Practices
- Energy Efficiency: Advanced technologies can help in designing processes that reduce energy consumption.
- Waste Reduction: Optimized cutting and material handling processes reduce waste material, contributing to more sustainable operations.
For ZHY Gear Manufacturer, investing in these technologies not only positions the company as a leader in innovation but also aligns with global trends towards efficiency, customization, and sustainability. These advancements can provide ZHY with a competitive edge in both domestic and international markets.