Reducing noise in worm gear systems is crucial for improving performance and user experience. Here are some effective noise reduction techniques:
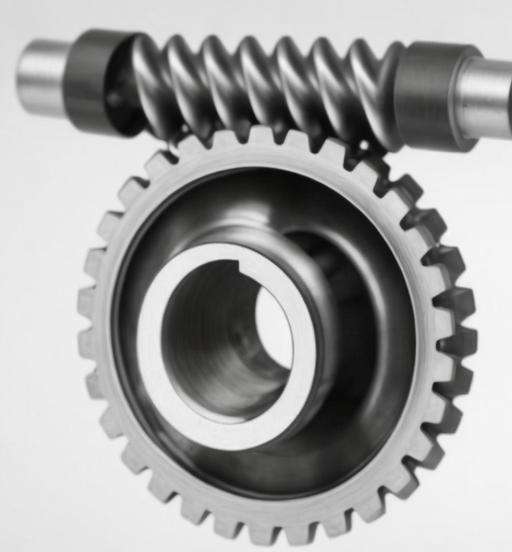
Design Considerations
- Optimized Gear Geometry:
- Tooth Profile Optimization: Designing the worm and wheel teeth for smoother meshing reduces noise. This includes using involute profiles and modifying the tooth shape for better contact.
- Helix Angle Adjustment: Selecting an appropriate helix angle can minimize noise by ensuring smoother engagement between the worm and the wheel.
- Precision Manufacturing:
- High Precision Machining: Using advanced CNC machines to achieve tight tolerances and smoother surfaces reduces noise caused by misalignment and roughness.
- Quality Control: Implementing stringent quality control measures to ensure uniformity and precision in worm gear production.
Material Selection
- Low-Noise Materials:
- Polymer Gears: Using engineering plastics (e.g., nylon, acetal) for worm wheels can significantly reduce noise due to their inherent damping properties.
- Composite Materials: Employing composite materials with good damping characteristics can help absorb vibrations and reduce noise.
- Lubrication:
- Advanced Lubricants: Using high-quality synthetic lubricants can reduce friction and noise. Lubricants with anti-wear additives also help maintain smooth operation.
- Self-Lubricating Materials: Incorporating self-lubricating materials in the worm gear components can minimize the need for external lubrication and reduce noise.
Mechanical Adjustments
- Proper Alignment:
- Accurate Assembly: Ensuring precise alignment of the worm and wheel during assembly reduces misalignment and the resulting noise.
- Adjustment Mechanisms: Implementing adjustment mechanisms to maintain proper alignment over worm gear’s operational life.
- Damping Elements:
- Vibration Dampers: Using vibration dampers or isolators can absorb vibrations and reduce noise transmission to the surrounding structure.
- Damping Coatings: Applying damping coatings to worm gear housings can help in reducing noise by absorbing vibrations.
Operational Techniques
- Controlled Load:
- Load Distribution: Ensuring even load distribution across worm gear teeth can minimize noise caused by uneven wear and stress.
- Shock Load Reduction: Implementing measures to reduce sudden shock loads, such as using flexible couplings, can prevent noise spikes.
- Speed Control:
- Optimal Speed Operation: Operating the worm gear at optimal speeds can reduce noise. Lower speeds typically result in less noise, but this must be balanced with performance requirements.
- Smooth Acceleration/Deceleration: Gradual changes in speed can prevent noise caused by sudden accelerations or decelerations.
Maintenance Practices
- Regular Inspection:
- Wear Monitoring: Regularly inspecting worm gear for wear and damage ensures timely maintenance and replacement, preventing noise from worn-out components.
- Lubrication Maintenance: Regularly checking and replenishing lubrication to maintain optimal lubrication levels and reduce noise.
- Component Replacement:
- Replacing Worn Parts: Timely replacement of worn or damaged components prevents noise due to poor meshing or misalignment.
- Upgrading Components: Upgrading to higher quality or more precise components can also help in reducing noise.
Innovative Technologies
- Active Noise Control:
- Noise Cancellation Systems: Implementing active noise cancellation systems using microphones and speakers to counteract worm gear noise.
- Smart Monitoring: Using sensors and monitoring systems to detect and address noise issues in real-time.
- Advanced Surface Treatments:
- Surface Coatings: Applying advanced surface coatings like Teflon or ceramic can reduce friction and noise.
- Cryogenic Treatments: Enhancing material properties through cryogenic treatments to reduce noise generation.
By combining these design, material, mechanical, operational, and maintenance techniques, worm gear systems can achieve significant noise reduction, resulting in quieter and more efficient operation.