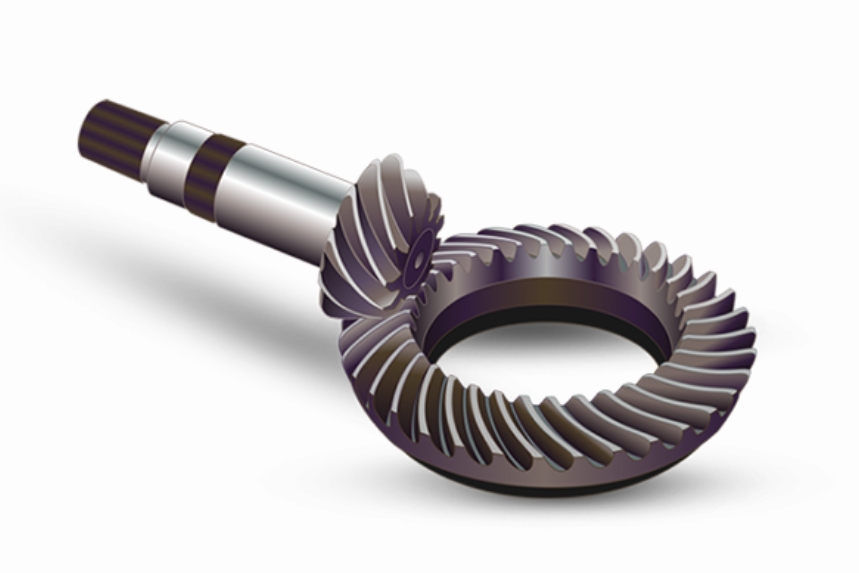
Advancements in spiral bevel gear technology have been significant over the years, driven by the need for more efficient, durable, and quieter gears in various industries such as automotive, aerospace, and industrial machinery. Here are some key advancements in this field:
- Materials and Heat Treatment: The development of advanced materials, such as new steel alloys and composites, and improved heat treatment processes have significantly increased the strength, durability, and longevity of spiral bevel gear.
- Precision Manufacturing: Advancements in manufacturing technologies, including CNC machining and 3D printing, have allowed for more precise and consistent production of spiral bevel gear. This precision leads to better meshing of gears, reduced vibration, and less noise.
- Computer-Aided Design (CAD): The use of CAD software has revolutionized the design process for spiral bevel gear. Engineers can now create more complex and precise gear geometries, simulate gear performance under various conditions, and optimize designs for specific applications.
- Coatings and Surface Treatments: The application of advanced coatings and surface treatments can reduce friction, wear, and corrosion, thereby enhancing the performance and life of spiral bevel gears.
- Noise Reduction Technologies: Addressing noise and vibration is critical in many applications. Advanced gear design, such as modifying the tooth geometry and using noise dampening materials, has been instrumental in reducing gear noise.
- Lubrication Technologies: The development of specialized lubricants and lubrication systems has improved the efficiency and lifespan of spiral bevel gear, especially under high stress and temperature conditions.
- Analytical Methods and Testing: Improved analytical methods, such as finite element analysis (FEA), and advanced testing techniques provide better insights into gear stresses, failures, and performance, leading to more reliable and durable gear designs.
- Customization and Flexibility: The ability to customize gear designs for specific applications and the flexibility to adapt to various sizes and configurations have expanded the use of spiral bevel gear across different industries.
- Integration with Electronics: The integration of spiral bevel gear with electronic systems, such as sensors and actuators, in smart machinery and vehicles, allows for real-time monitoring and control of spiral bevel gear performance, enhancing efficiency and reliability.
- Sustainability Considerations: There is a growing emphasis on sustainable manufacturing practices and the use of recyclable or eco-friendly materials in spiral bevel gear production.
These advancements not only improve the performance and efficiency of spiral bevel gear but also open up new possibilities for their application in emerging technologies and industries.