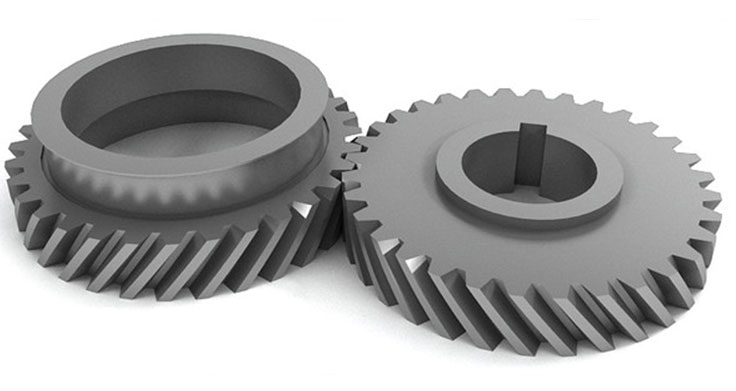
Helical gears offer several advantages that make them a preferred choice in modern mechanical systems. Their unique design and functional features provide various benefits, making them suitable for a wide range of applications. Here are the advantages of using helical gears:
1. Smooth and Quiet Operation:
- Helical gears provide gradual tooth engagement, resulting in smoother and quieter gear operation compared to straight-cut spur gears. This makes them ideal for applications where low noise levels are essential, such as in precision machinery, automotive transmissions, and consumer products.
2. High Load-Carrying Capacity:
- The helix angle of helical gears allows multiple teeth to be in contact simultaneously, leading to a higher tooth contact ratio. This distributes the load across a larger surface area, enhancing the gear’s load-carrying capacity and improving the overall strength of the gear system.
3. Increased Efficiency:
- The gradual tooth engagement in helical gears reduces impact and sliding between teeth, leading to higher efficiency compared to straight-cut spur gears. This efficiency is particularly beneficial in power transmission applications where minimizing energy losses is crucial.
4. Versatility and Adaptability:
- Helical gears can be used in various configurations, such as parallel shafts, intersecting shafts, and crossed helical gear arrangements. Their adaptability makes them suitable for a wide range of mechanical systems, including automotive, industrial, and robotics.
5. Compact Design:
- Helical gears have a more compact design compared to other types of gears, such as bevel gears. This space-saving feature is advantageous in applications where available space is limited.
6. Improved Tooth Strength:
- The helix angle in helical gears improves the tooth’s strength by providing a gradual transition from one tooth to the next. This reduces stress concentrations at the tooth roots, enhancing the gear’s durability and reducing the risk of tooth breakage.
7. Load Distribution and Alignment:
- The helix angle helps in aligning the gears smoothly during meshing, minimizing tooth deflection, and ensuring proper load distribution across the gear teeth. This leads to reduced wear and prolongs the gear’s lifespan.
8. Reverse Rotation Capability:
- Unlike some other gear types, helical gears can transmit power in either direction, making them suitable for applications that require reversing the rotational direction, such as in marine propulsion systems.
9. High Precision:
- Helical gears can be manufactured with high precision, ensuring accurate gear meshing and reducing the risk of backlash. This precision is crucial in applications where accurate motion control is required, such as in robotics and CNC machines.
10. Axial Thrust Management:
- Helical gears produce axial thrust due to their helix angle. This axial thrust can be balanced out in gear pairs with opposite helix directions, ensuring smooth gear operation and reducing the need for additional thrust bearings.
The advantages of helical gears, including their smooth operation, high load-carrying capacity, efficiency, and versatility, make them a popular choice in modern mechanical systems across various industries and applications.