Helical gear is a fundamental component in modern machinery, offering advantages over their spur gear counterparts in terms of noise reduction, smooth operation, and the ability to transmit higher loads. For beginners looking to understand the mechanics of helical gear, it’s essential to grasp their design characteristics, operational principles, and the reasons behind their widespread use in various applications. Here’s a beginner-friendly guide to helical gear mechanics.
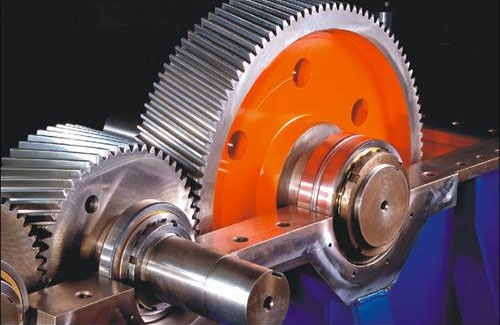
Basic Concepts of Helical Gear
- Definition and Design: Unlike spur gear, which have teeth that are parallel to the gear axis, helical gear has teeth that are cut at an angle to the gear face. This angle is known as the helix angle. The teeth of helical gear engage gradually, starting from one end of the tooth to the other as they rotate, which ensures smoother gear operation.
- Helix Angle: The helix angle plays a crucial role in the gear’s performance. A larger helix angle results in a greater contact area between the teeth of the meshing helical gear, leading to smoother operation and the ability to carry a higher load. However, it also generates axial thrust, which must be accommodated by appropriate bearing support.
- Right-Handed vs. Left-Handed Helical Gear: The helix angle can be oriented in two directions, making helical gear either right-handed or left-handed. When two helical gear mesh together, one must be right-handed and the other left-handed for them to interlock correctly.
Operational Principles
- Smooth Engagement: The helical design allows for a gradual engagement between the teeth of two meshing helical gear, reducing shock loads on the helical gear teeth and minimizing noise and vibration. This gradual engagement makes helical gear ideal for high-speed applications.
- Increased Load Capacity: Due to the larger contact area provided by the angled teeth, helical gear can distribute loads more evenly across their teeth than spur gear. This results in increased load capacity and the potential for longer gear life.
- Axial Thrust: The angled teeth of helical gear introduce axial thrust, which is a force along the axis of the helical gear shaft. This force needs to be considered in the design of the gearbox, requiring specific types of bearings that can handle these loads.
Applications and Advantages
- Versatility: Helical gear is used in a wide range of applications, from automotive transmissions to industrial machinery, due to their efficiency, reliability, and quiet operation.
- High-Speed and High-Power Applications: The smooth operation and robustness of helical gear make them particularly suited for applications involving high speeds and high power, where noise and vibration need to be minimized.
- Durability: The increased contact area and gradual engagement of helical gear teeth lead to less wear and tear over time, contributing to the gear’s durability and longevity.
Challenges and Considerations
- Axial Thrust Management: Designing a system that can effectively handle the axial thrust generated by helical gear is crucial. This often involves using thrust bearings and designing helical gearboxes that can accommodate these forces.
- Manufacturing Complexity: Producing helical gear is generally more complex than manufacturing spur gear, potentially leading to higher costs. The manufacturing process requires specialized equipment and expertise, especially for gears with high helix angles or large dimensions.
- Lubrication: Proper lubrication is essential for maintaining the efficiency and lifespan of helical gear. The lubrication system must be designed to ensure adequate lubricant coverage, particularly in high-speed or high-load applications.
Understanding the mechanics of helical gear provides a solid foundation for exploring their applications and the complexities involved in their design and manufacture. This knowledge is essential for anyone looking to work with or design gear-driven systems, offering a pathway to more advanced studies or practical applications in engineering and mechanics.