This article focuses on the impact of tooth profile wear on the dynamic characteristics of double involute gears (DIGs). Through a series of theoretical calculations, model establishment, and analysis methods, the dynamic characteristics of the double involute gear transmission system under wear fault conditions are studied in depth. The research results can provide a theoretical basis and technical support for the design, optimization, and fault diagnosis of double involute gear transmission systems.
1. Introduction
1.1 Research Background
Gears are crucial components in mechanical transmission systems, and their performance directly affects the operation stability and reliability of the entire system. Double involute gears, as a new type of gear, have attracted increasing attention due to their unique advantages. However, during the operation of gears, tooth surface wear is a common failure form, which can lead to a series of problems such as reduced transmission accuracy, increased vibration and noise, and shortened service life. Therefore, it is of great significance to study the dynamic characteristics of double involute gear transmission systems considering wear faults.
1.2 Research Significance
The research on the dynamic characteristics of double involute gear transmission systems considering wear faults can help us better understand the influence mechanism of wear on gear performance. By establishing accurate models and analyzing the dynamic response of gears under different wear conditions, we can provide a theoretical basis for the design of high – performance double involute gears, optimize the gear transmission system, and improve its reliability and durability. At the same time, it also provides a reference for the fault diagnosis and prediction of gear transmission systems, which is conducive to early detection of gear wear faults and timely maintenance, reducing the occurrence of accidents and economic losses.
1.3 Research Status
Many scholars have conducted research on gear wear and its impact on dynamic characteristics. Zhou Changjiang et al. proposed a calculation method for the adhesive wear of helical gear tooth surfaces under quasi – static and dynamic loads. Zhang Jiange et al. presented a mathematical model for calculating gear tooth surface wear considering the thermal – elastohydrodynamic coupling in the contact area. However, the research on the dynamic characteristics of double involute gears considering wear faults is still relatively scarce. There is a lack of in – depth understanding of the distribution law of tooth surface wear depth, the static transmission error without load caused by tooth surface wear, and the time – domain response of gears under different wear conditions.
2. Meshing Characteristics of Double Involute Gear Transmission System
2.1 Calculation of Gear Contact Line Length and Tooth Surface Load
The contact line length and tooth surface load of double involute gears are important parameters reflecting their meshing characteristics. In this study, the contact line percentage method is adopted based on the “segmentation method” idea. When the face contact ratio of double involute gears is greater than the axial contact ratio, the contact line length at different times can be calculated by the following formula:
Time Interval | Contact Line Length Formula |
---|---|
\(0\leq t\leq t_{B_{2}C}\) | \(l_{c}^{i}(t) = r_{b1}\omega_{1}t/\sin\beta_{b1}\) |
\(t_{B_{2}C}\leq t\leq t_{B_{2}D}\) | \(l_{c}^{i}(t) = l_{B_{2}C}/\sin\beta_{b1}\) |
\(t_{B_{2}D}\leq t\leq B_{B_{2}E}\) | \(l_{c}^{i}(t)=l_{B_{2}C}/\sin\beta_{b1}+(r_{b1}\omega_{1}t – l_{CD}-l_{B_{2}C}+l_{-})/\sin\beta_{b1}\) |
\(t_{B_{2}E}\leq t\leq t_{B_{2}B_{1}}\) | \(l_{c}^{i}(t)=(l_{B_{2}E}-l_{CD})/\sin\beta_{b1}\) |
\(t_{B_{2}B_{1}}\leq t\leq t_{B_{2}F}\) | \(l_{c}^{i}(t)=(l_{B_{2}C}-(r_{b1}\omega_{1}t + l_{-}-l_{B_{2}E}))/\sin\beta_{b1}+l_{B_{1}D}/\sin\beta_{b1}\) |
\(t_{B_{2}F}\leq t\leq t_{B_{2}G}\) | \(l_{c}^{i}(t) = l_{B_{1}D}/\sin\beta_{b1}\) |
where \(l_{-}=m_{n}(y_{a}^{*}+y_{d}^{*}-I_{a}^{*}\tan a_{a}-l_{d}^{*}\tan a_{a})\).
Assuming that the tooth surface load is evenly distributed along the contact line direction, the quasi – static load on the m – th segment of the i – th line segment at time t can be calculated by the formula \(F_{m}^{i}(t)=F_{n}\frac{l_{m}^{i}(t)}{l_{z}(t)}\), where \(F_{n}\) is the normal load acting on the contact line of the gear tooth surface, and \(L_{z}(t)=\sum_{i = 1}^{n}l_{c}^{i}(t)\) is the total length of all contact lines at time t.
[Insert a figure here to show the double involute gear and its contact line, such as a schematic diagram of the gear meshing process with the contact line marked]
2.2 Relative Slip Distance and Equivalent Contact Model
In the study of wear, the “segmentation method” is used to simplify the double involute gear transmission as the contact of multiple spur gear slices. When meshing, multiple pairs of gears are involved in meshing, and the contact line is divided into multiple equal – distance line segments.
The equivalent curvature radius, the curvature radius of the driven wheel, the relative sliding speed, and the entrainment speed at any position m on the contact line can be calculated by the following formulas: \(\begin{cases}R=\frac{R_{1m}^{i}(t)R_{2m}^{i}(t)}{R_{1m}^{i}(t)+R_{2m}^{i}(t)}\\R_{2m}^{i}(t)=N_{1}N_{2}-R_{1m}^{i}(t)\\u_{s}=\vert\omega_{1}R_{1m}^{i}(t)-\omega_{2}R_{2m}^{i}(t)\vert\\u_{r}=\frac{\omega_{1}R_{1m}^{i}(t)+\omega_{2}R_{2m}^{i}(t)}{2}\end{cases}\)
According to the Hertz elastic contact theory, the contact semi – width \(a_{H}\) and the average contact pressure p can be expressed as \(a_{H}=2\sqrt{FR/(\pi E_{eq})}\) and \(p = \frac{4F}{3\pi a_{H}}\), where F is the normal meshing force at the contact point, and \(E_{eq}\) is the equivalent elastic modulus. The slip distances of the meshing points on the tooth profiles of the driving and driven wheels are \(s_{1}=2a_{H}\frac{\vert\omega_{1}R_{1m}^{i}(t)-\omega_{2}R_{2m}^{i}(t)\vert}{\omega_{1}R_{1m}^{i}(t)}\) and \(s_{2}=2a_{H}\frac{\vert\omega_{1}R_{1m}^{i}(t)-\omega_{2}R_{2m}^{i}(t)\vert}{\omega_{2}R_{2m}^{i}(t)}\) respectively.
3. Tooth Surface Wear Model of Double Involute Gears
3.1 Tooth Surface Cumulative Wear Amount
The classical Archard tooth surface adhesive wear calculation model is widely used in dry friction. However, most industrial gears work under mixed elastohydrodynamic lubrication conditions, and the gear tooth surface adhesive wear has complex characteristics such as time – variability and nonlinearity. Therefore, it is necessary to consider the influence of gear tooth surface lubrication on wear.
In the mixed elastohydrodynamic lubrication mode, the tooth surface contact load is shared by the lubricating oil film and the tooth surface micro – protrusions. Based on the classical Archard wear calculation model, MASJEDI proposed an improved Archard wear model and calculated the tooth surface wear rate considering the mixed elastohydrodynamic lubrication state.
The tooth surface wear formula in the mixed elastohydrodynamic lubrication state is \(V = k\psi(\frac{L_{a}}{100})FS\), where k is a dimensional wear coefficient related to gear materials and working conditions, \(L_{a}\) is the rough load ratio, F is the normal load on the contact tooth surface, and \(\psi\) is the film defect ratio. The expressions of \(\psi\) and \(L_{a}\) are \(\psi = 1-\exp[-\frac{X}{u_{r}t_{0}}\exp(-\frac{E_{a}}{R_{g}T_{s}})]\) and \(L_{a}=0.005W^{-0.408}U^{-0.088}G^{0.103}\cdot[\ln(1 + 4470\sigma_{a}^{-6.015}V^{1.188}W^{0.485}U^{-2.741}G^{-2.898})]\) respectively. The dimensionless variables such as the tooth surface contact load W, the tooth surface rolling rate U, the modulus parameter G, the tooth surface hardness V, and the roughness \(\sigma_{a}\) can be calculated according to relevant references.
[Insert a figure here to show the relationship between wear amount and different parameters, such as a graph of wear amount changing with load]
3.2 Calculation of Tooth Surface Cumulative Wear Depth
In the mixed elastohydrodynamic lubrication state, the wear amounts of double involute gears and ordinary involute helical gears under different meshing cycles are calculated. The basic geometric parameters and working condition parameters of the double involute gears are shown in Table 1.
Parameter/Unit | Value |
---|---|
Number of teeth \(z_{1}/z_{2}\) | 22/110 |
Normal modulus \(m_{n}/mm\) | 3 |
Normal pressure angle \(\alpha_{n}/(^{\circ})\) | 20 |
Helix angle \(\beta/(^{\circ})\) | – |
Tooth width \(B/mm\) | 80 |
Wear coefficient K | \(1\times10^{-16}\) |
Tangential modification coefficient \(y_{a}^{*}=y_{b}^{*}\) | 0.08 |
Height coefficient \(l_{a}^{*}=l_{b}^{*}\) | 0.04 |
Driving wheel torque \(T_{p}/(N\cdot m)\) | 300 |
Elastic modulus \(E/GPa\) | 207 |
Poisson’s ratio \(v_{1},v_{2}\) | 0.27 |
Density \(\rho/(kg/m^{3})\) | 7850 |
According to the established gear wear model, the cumulative wear amounts under different meshing times can be obtained. The distribution of gear wear on the tooth surfaces of the driving and driven wheels of double involute gears and ordinary involute gears after running for \(50h(N = 3\times10^{6})\), \(150h(N = 0.9\times10^{7})\), and \(300h(N = 1.8\times10^{7})\) is shown in Figure 2.
From Figure 2, it can be seen that the tooth surface cumulative wear depth at the tooth root and tooth tip positions of the gear is greater than that near the pitch line. The maximum wear depth occurs at the tooth root position because the slip rate calculation results at the meshing – in and meshing – out positions are large, so the relative slip distance is also large. Due to the step – shaped tooth waist of the double involute gear, the wear amount near the pitch circle is close to 0. In the mixed elastohydrodynamic lubrication state, the maximum cumulative wear difference between the double involute gear and the ordinary involute gear at the tooth root position near the pitch line is reduced from \(0.04023\ \mu m\) to \(0.00207\ \mu m\). The wear of the double involute gear near the tooth root position of the pitch line is significantly reduced, and the wear of the double involute gear near the tooth tip position of the pitch line is less than that of the ordinary involute gear.
4. Wear Stiffness Calculation Model of Double Involute Gears
4.1 Meshing Stiffness Calculation Model of Double Involute Gears
The meshing stiffness of gears is an important parameter affecting the dynamic characteristics of the gear transmission system. In this study, the tooth of the double involute gear is regarded as a non – uniform cantilever beam. During the gear tooth meshing process, under the action of the meshing force, bending deformation, shear deformation, compression deformation, substrate deformation, and contact deformation will occur.
The single tooth of the double involute gear is simplified as a cantilever beam and discretized into multiple rectangular micro – elements by the integral method. According to the cantilever beam theory, the meshing stiffness \(K_{m}\) at the meshing point m of a pair of meshing gears is calculated by the Weber energy method as \(K_{m}=\frac{F_{m}}{\delta_{m}}\), where \(F_{m}\) is the normal contact force at the meshing point m, and \(\delta_{m}\) is the comprehensive elastic deformation amount at the meshing point m. The comprehensive elastic deformation amount \(\delta_{m}=\sum_{i = 1}^{2}\delta_{1im}+\delta_{2im}+\delta_{3im}+\delta_{4im}+\delta_{5im}\), and the calculation formulas of each deformation amount are as follows: \(\begin{align*}\delta_{1im}&=(\frac{F_{m}L_{i}^{3}}{3E_{e}I_{i}}+\frac{F_{m}L_{i}^{2}S_{im}}{2E_{e}I_{i}})\cos\alpha_{j}+(\frac{F_{m}L_{i}^{3}}{2E_{e}I_{i}}+\frac{F_{m}L_{i}^{3}S_{im}}{2E_{e}I_{i}})(S_{im}\cos\alpha_{m}-y_{i}\sin\alpha_{m})\\\delta_{2im}&=\frac{12F_{m}L_{i}(1 + v)}{5E_{e}A_{i}}\cos\alpha_{m}\\\delta_{3im}&=\frac{F_{m}L_{m}}{E_{e}A_{i}}\sin\alpha_{m}\\\delta_{4im}&=\frac{F_{m}\cos^{2}\alpha_{m}}{BE}\\\delta_{5im}&=\frac{1.275}{E_{12e}^{0.9}B^{0.8}F_{m}^{0.1}}\end{align*}\)
where \(E_{e}\) is the equivalent elastic modulus of the gear, B is the tooth width of the gear, \(\alpha_{m}\) is the pressure angle at the meshing point m, and v is Poisson’s ratio.
4.2 Calculation of the Stiffness of Double Involute Gears with Wear Faults
Tooth surface wear of gears mainly affects the bending deformation amount \(\delta_{1in}\), shear deformation amount \(\delta_{2im}\), and compression deformation amount \(\delta_{3im}\). When tooth surface wear occurs, the geometric parameters of the cantilever beam model change. The changes in the geometric parameters are expressed as \(y=y_{i}-y_{wear}\cos\alpha_{m}\) and \(\begin{cases}I_{i}=\frac{B}{12}(2y_{i}-y_{wear}\cos\alpha_{m})^{3}\\A_{x}=2By_{i}-y_{wear}B\cos\alpha_{m}\end{cases}\), where \(y_{wear}\) is the wear depth at the load – acting point m. By calculating, the single – tooth meshing stiffness of the double involute gear considering tooth surface wear can be obtained.
4.3 Stiffness under Tooth Surface Cumulative Wear Depth
Considering the time – varying characteristics of the meshing stiffness and the relationship between the contact line length and time, the formula for calculating the maximum value of the single – pair gear tooth stiffness of the external meshing gear transmission is \(c’=c_{th}’C_{M}C_{R}C_{B}\cos(\beta)(\frac{F_{t}K_{A}}{100\cdot B})^{0.25}l_{m}'(t)\times10^{6}\). The basic parameters are selected from the literature, and the theoretical value of the single – pair gear meshing stiffness \(c_{th}’\) is \(c_{th}’=C_{1}+\frac{C_{2}}{z_{n1}}+\frac{C_{3}}{z_{n2}}-C_{4}x_{1}-\frac{C_{5}x_{1}}{z_{n1}}-C_{6}x_{2}-\frac{C_{7}x_{2}}{z_{n2}}+C_{8}x_{1}^{2}+C_{9}x_{2}^{2}\).
Through calculation, it can be known that the maximum value of the single – pair gear meshing stiffness of the ordinary involute helical gear is \(3.090211\times10^{9}N/m\), and the error between the calculation result of the cantilever beam model proposed in this study and it is within 10%, indicating that the established cantilever beam model is reliable.
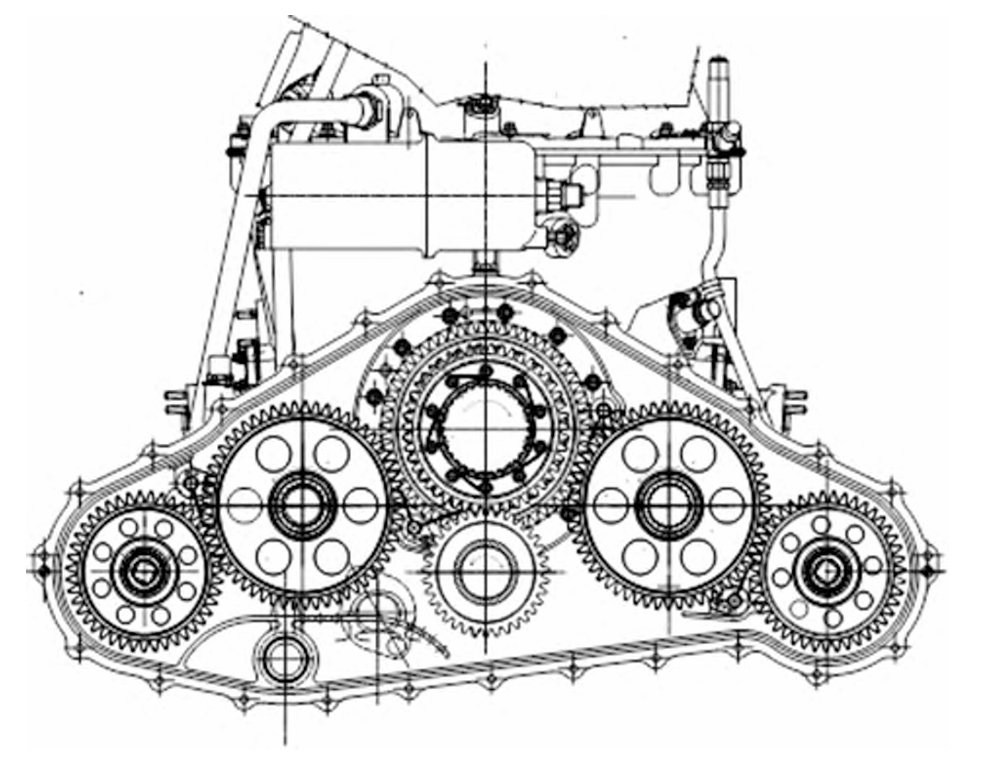