The evolution of hypoid gears has been a journey of combining theoretical concepts with practical engineering solutions to meet the demands of various industrial applications. Let’s explore the key stages of this evolution:
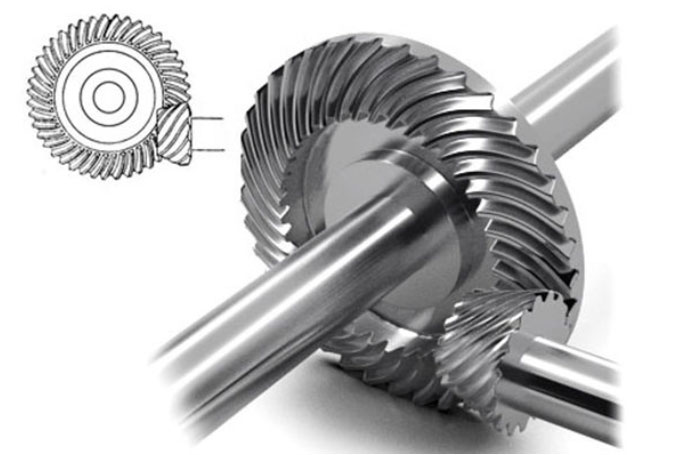
- Early Concept and Design: The concept of hypoid gears emerged from the development of bevel gears, which were used in various applications, including mechanical power transmission and machinery. Early engineers recognized the potential benefits of an offset design to improve load distribution and torque capacity.
- Manufacturing Advancements: As industrial manufacturing techniques advanced, engineers gained the ability to produce more precise and complex gear geometries. This progress allowed for the practical realization of hypoid gears, enabling their use in a wider range of applications.
- Automotive Transmissions: One of the most significant milestones in the evolution of hypoid gears was their adoption in automotive differentials. Hypoid gears proved to be ideal for this application due to their offset design, which allowed for efficient power transmission and smooth operation. Automotive differentials equipped with hypoid gears became essential components in providing torque to the wheels while allowing them to rotate at different speeds during turns.
- Aerospace and Industrial Machinery: As manufacturing processes improved, the application of hypoid gears expanded beyond automotive differentials. The aerospace and industrial machinery sectors recognized the advantages of hypoid gears in terms of load distribution, efficiency, and noise reduction. Hypoid gears found their way into aerospace systems, heavy machinery, marine propulsion systems, robotics, and more.
- Advancements in Gear Design: The continuous evolution of gear design software and simulation tools enabled engineers to optimize hypoid gear designs for specific applications. This led to the development of tailored gear tooth profiles, material selections, and heat treatment processes to enhance gear performance and durability.
- Material Science and Heat Treatment: Innovations in material science allowed the use of advanced alloys and specialized steels for hypoid gears. These materials offer higher strength and wear resistance, improving the gears’ ability to withstand demanding loads and harsh operating conditions. Advancements in heat treatment processes further enhanced the mechanical properties of the gears.
- Noise and Vibration Reduction: Engineers focused on reducing noise and vibration in gear systems, leading to improvements in gear tooth profiles and manufacturing techniques. This development made hypoid gears even more attractive in applications where quiet operation is essential, such as automotive and robotics.
- Sustainability and Green Practices: In recent years, the focus on sustainability and eco-friendly manufacturing practices has influenced the use of hypoid gears. Manufacturers have embraced more efficient production methods, and advancements in lubricants and surface treatments have reduced friction and energy loss, contributing to greater overall efficiency.
- Industry 4.0 Integration: With the advent of Industry 4.0 and the Internet of Things (IoT), the integration of sensors and data analytics has enabled predictive maintenance and real-time monitoring of gear systems. This proactive approach ensures optimal gear performance and reduces the risk of unexpected failures.
The evolution of hypoid gears has been driven by a combination of theoretical developments, advancements in manufacturing technologies, and a deep understanding of the specific needs of diverse industrial applications. From automotive differentials to aerospace systems, hypoid gears continue to play a crucial role in modern engineering, providing efficient power transmission, high torque capacity, and reliable performance across a broad spectrum of industries.