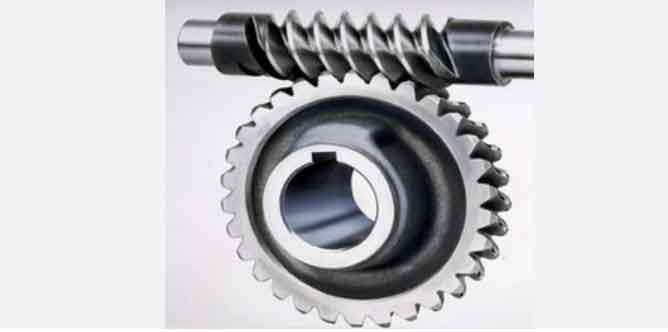
Worm gears play a vital role in robotics, providing precise motion control and torque transmission in various robotic systems. Advancements and innovations in worm gear technology have significantly enhanced the performance and capabilities of robots. Here are some key advancements in worm gears in robotics:
- Miniaturization and Lightweight Design: As robotics moves toward more compact and agile systems, worm gears have been designed to be smaller and lighter while maintaining their efficiency and load-carrying capacity. This allows for the integration of worm gears into small-scale robots, including drones, medical robots, and miniature industrial robots.
- Materials and Coatings: Advanced materials and surface coatings are being used to improve the wear resistance and reduce friction in worm gears. The application of hard coatings, such as diamond-like carbon (DLC), enhances the durability and lifespan of the gears, making them more suitable for high-speed and high-repetition robotic movements.
- Precision Machining and Gear Grinding: High-precision machining and gear grinding techniques ensure that worm gears have accurate tooth profiles and minimal manufacturing errors. This level of precision results in smoother motion, reduced noise, and higher efficiency in robotic systems.
- Integrated Gear-Motor Systems: Manufacturers are developing compact gear-motor assemblies that combine the worm gear and motor into a single unit. These integrated systems eliminate the need for external mounting and alignment, saving space and simplifying the robot’s mechanical design.
- Backlash Compensation: Backlash is a common issue in worm gear systems, leading to lost motion and reduced accuracy. Advanced backlash compensation techniques, such as using preloaded double-enveloping worm gears, are employed to minimize backlash and improve precision in robotic movements.
- Self-Locking Mechanisms: Worm gears possess inherent self-locking properties, meaning they can hold a load without the need for additional braking systems. This feature is advantageous in robotic applications where maintaining position and stability are critical, such as robotic arms in surgical procedures.
- Reduced Noise and Vibration: Innovations in gear design and manufacturing processes have resulted in quieter and smoother operation of worm gears, which is crucial in noise-sensitive environments, like medical facilities and office settings.
- Smart Gear Technology: Some worm gears now come equipped with embedded sensors or monitoring systems that allow for real-time condition monitoring. These sensors can detect issues like gear wear, abnormal loads, or misalignment, enabling predictive maintenance and enhancing the reliability of robotic systems.
- High Torque Transmission: Worm gears are capable of transmitting high torque, which is advantageous in applications requiring heavy lifting or manipulation tasks, such as in industrial robots.
These advancements in worm gear technology have made robotic systems more efficient, reliable, and adaptable to various applications. As robotics continues to evolve, ongoing research and development in worm gear design and manufacturing will further optimize motion control and improve the overall performance of robotic systems.