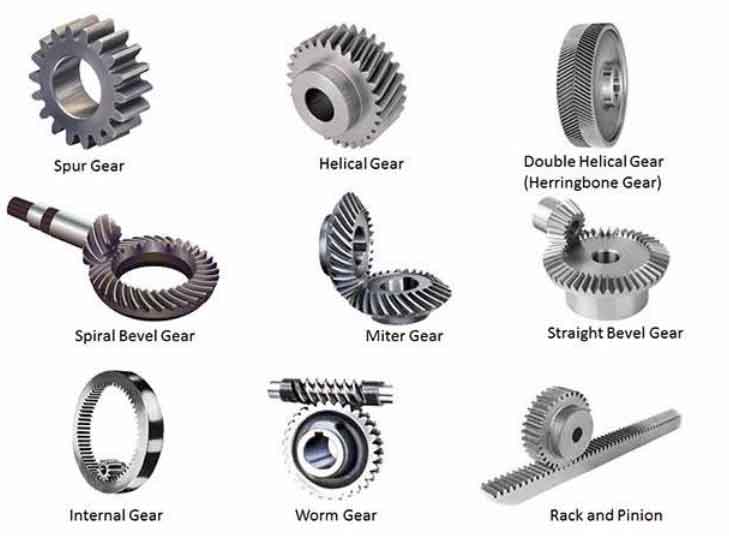
The first can be traced back primitive gear to over 3,000 years ago. They were made of wood and the pins were attached teeth. Early Greeks used metal gears with wedge shaped teeth; Romans gears in their mills used; Stone gears were used in Sweden in the Middle Ages (Gears Manufacturers). All of the cultures found reasons to use basic leverage energy or motion to convert in either a form they could use in technologically advanced devices of their societies. Gears were used by early engineers for lifting heavy loads through the use of their force-multiplying properties.
One example of this type of application was anchored ship lifts and catapults. Gear technology made its biggest leaps during the industrial revolution in Great Britain during the eighteenth century (eFunda). As more sophisticated machines over the years, technology and manufacturing equipment also developed at a rapid pace. Gears became essential elements in countless devices, from clocks to complex machinery. Today, gears used in many of the machines depend on every day people, such as automobiles.
The main objective is leveraging the manipulation of motion in the form of more potent or usable. The different types of gears allow for endless possibilities in manipulating. The three classes are three gears have parallel axis gears, gears nonparallel-coplanar and nonparallelnoncoplanar equipment.
The history of spiral bevel gears is a fascinating journey that spans several centuries, showcasing human ingenuity in mechanical design and engineering. Spiral bevel gears, known for their curved teeth which mesh with a gradual engaging action, represent a significant advancement over straight bevel gears by offering smoother operation, less noise, and the ability to transmit more power. Their development and refinement over the years have been driven by the evolving needs of various industries, including automotive, aviation, and manufacturing.
Early Beginnings
The concept of gears dates back to ancient civilizations, with early examples like the Antikythera mechanism (circa 2nd century BCE) demonstrating the use of gear systems. However, these early gears were primarily straight-toothed, as the manufacturing and design knowledge required for more complex shapes like spiral bevel gears had not yet been developed.
Industrial Revolution and Beyond
- 19th Century: The Industrial Revolution marked a period of rapid technological advancement and increased interest in improving mechanical transmissions. The need for more efficient machinery that could transmit power more smoothly and quietly led to the exploration of gears with curved teeth profiles.
- Late 19th Century: Significant developments in gear design and manufacturing techniques during this period laid the groundwork for the modern spiral bevel gear. Innovations in metal cutting and precision engineering allowed for the production of more complex gear shapes.
The 20th Century: Refinement and Wide-Spread Use
- Early 20th Century: The automotive industry’s growth necessitated the development of more compact and efficient gearboxes capable of handling the increased speeds and loads of motor vehicles. This demand accelerated the refinement of spiral bevel gears, which were ideal for differential gear systems due to their smooth operation and ability to handle varying angles and loads.
- Mid-20th Century: Advances in machining and tooling technologies, along with better understanding of gear tooth geometry, enabled the mass production of spiral bevel gears with high precision. The development of computer-aided design (CAD) and computer-aided manufacturing (CAM) further revolutionized their production, allowing for more complex and accurate designs.
- Late 20th Century: The aerospace industry, with its stringent requirements for lightweight, high-performance components, also contributed to the advancement of spiral bevel gear technology. The need for gears that could operate efficiently at high speeds and under significant loads led to innovations in materials science and heat treatment processes, improving the strength and durability of these gears.
21st Century: Continuing Innovation
Today, the evolution of spiral bevel gears continues, with ongoing research into materials, manufacturing processes, and gear tooth design. The introduction of new materials like advanced alloys and composites offers the potential for even lighter and stronger gears. Additionally, the advent of additive manufacturing (3D printing) presents new possibilities for producing gears with complex shapes and customized designs that were previously unfeasible.
Conclusion
The history of spiral bevel gears is a testament to the continuous quest for improvement in mechanical transmissions. From their early conceptual beginnings to their current status as critical components in a variety of mechanical systems, spiral bevel gears have undergone significant evolution. As technology advances, they will undoubtedly continue to play a vital role in driving forward the capabilities of mechanical systems across industries.