Material science plays a pivotal role in transforming gear manufacturing processes, pushing the boundaries of what is possible in terms of performance, durability, and efficiency. Advances in materials science have led to the development of new materials and treatments that significantly impact the design, production, and application of gears across various industries. Here’s an overview of how material science influences gear manufacturing:
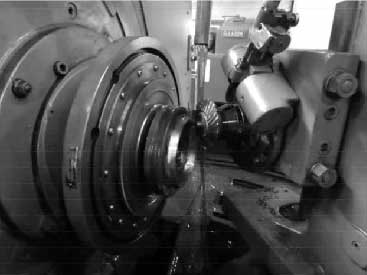
1. Development of Advanced Materials
- High-Performance Alloys: New alloys with enhanced strength, wear resistance, and thermal stability allow gears to operate under higher stresses and temperatures, expanding their use in demanding applications like aerospace and automotive racing.
- Composite Materials: The use of composite materials, including carbon fiber-reinforced polymers, offers a significant reduction in weight without compromising strength or durability. This is particularly beneficial in applications where weight reduction is critical, such as in aerospace and electric vehicles.
- Powder Metallurgy Gears: Advances in powder metallurgy have enabled the production of gears with materials that are difficult to process by traditional methods. These gears can offer superior performance characteristics, including enhanced durability and reduced noise.
2. Surface Treatments and Coatings
- Thermal and Chemical Treatments: Heat treatments (such as carburizing, nitriding) and chemical treatments improve the surface hardness and fatigue resistance of gears, extending their service life.
- Coatings: Advanced coatings, such as diamond-like carbon (DLC) and physical vapor deposition (PVD) coatings, reduce friction and wear, significantly enhancing the efficiency and longevity of gear systems.
3. Additive Manufacturing (3D Printing)
- Rapid Prototyping: Material science advancements have made it possible to 3D print gears using metals, polymers, and composites, allowing for rapid prototyping and testing of new designs.
- Complex Geometries: Additive manufacturing enables the production of gears with complex geometries that are challenging or impossible to create with traditional methods. This can lead to more efficient gear designs with improved performance.
- Customization: The ability to customize materials and designs easily with additive manufacturing opens up new possibilities for tailored solutions in specialized applications.
4. Enhanced Manufacturing Processes
- Precision Machining: The development of ultra-hard cutting tools made from materials like cubic boron nitride (CBN) and polycrystalline diamond (PCD) has enhanced the precision machining of gears, allowing for tighter tolerances and smoother finishes.
- Eco-Friendly Materials and Processes: Material science is also focusing on the sustainability aspect, developing eco-friendly materials and manufacturing processes that reduce environmental impact, such as minimizing hazardous waste and improving energy efficiency.
5. Smart Materials
- Self-Healing Materials: Research into self-healing materials could lead to gears that can repair minor cracks or wear automatically, significantly extending their operational life.
- Sensors Embedded in Materials: The integration of sensor technologies within gear materials can enable real-time monitoring of gear performance and health, facilitating predictive maintenance and reducing downtime.
Conclusion
The impact of material science on gear manufacturing processes is profound and multifaceted. By enabling the development of new materials, surface treatments, and manufacturing techniques, material science contributes to the creation of gears that are stronger, more efficient, and capable of operating in extreme conditions. As material science continues to advance, it is expected to unlock even greater possibilities for innovation in gear manufacturing, leading to further improvements in performance, sustainability, and cost-effectiveness.