The importance of material selection in gear manufacturing is crucial for ensuring enhanced performance, durability, and cost-efficiency of the gears used in various applications, from automotive to industrial machinery. The right choice of materials affects several key aspects of gear performance, including strength, wear resistance, and longevity. Here’s a detailed exploration of why material selection is so vital:
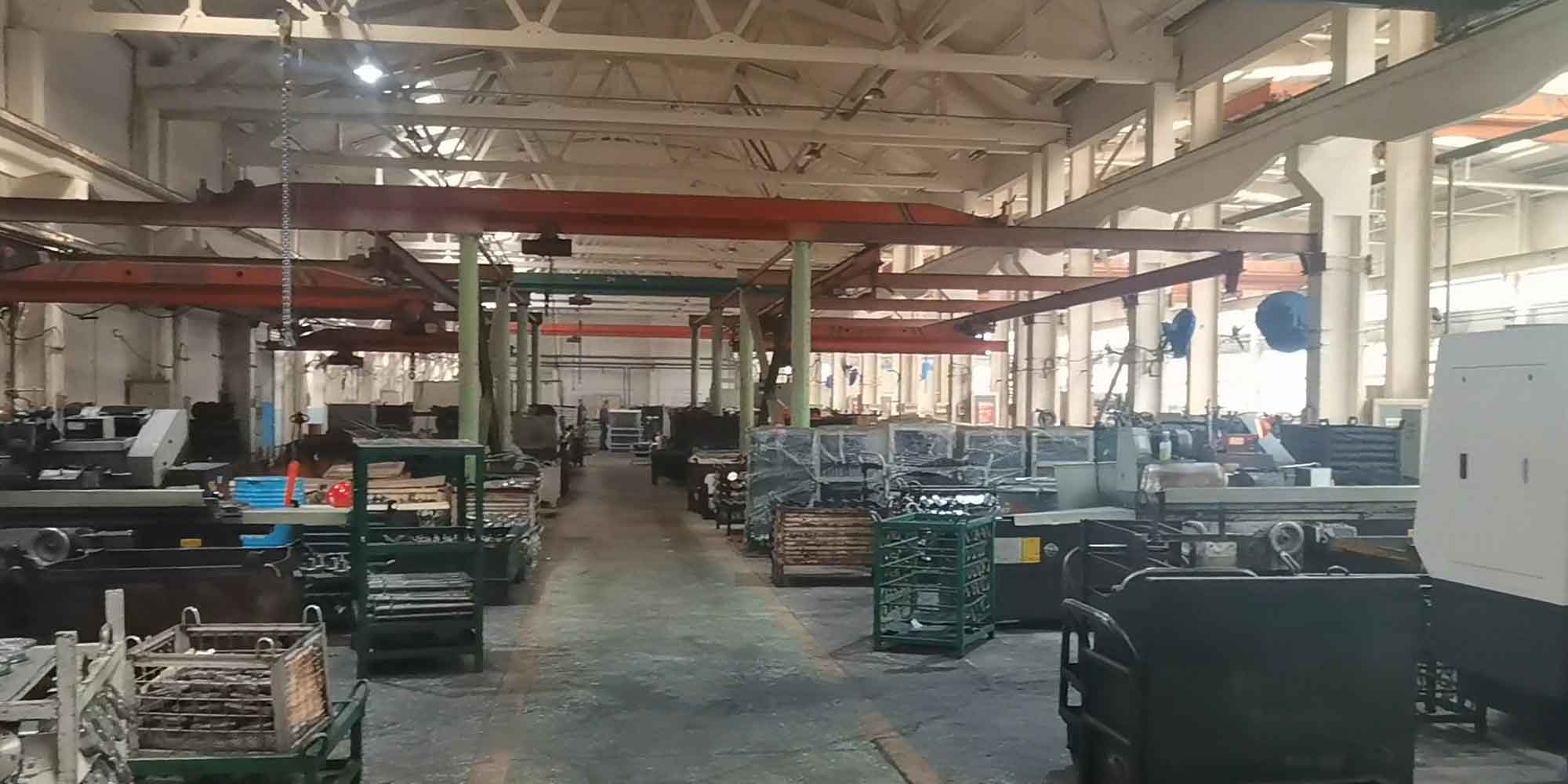
- Strength and Durability: The primary function of a gear is to transmit torque and, in some cases, alter the speed of machinery. The material must have sufficient strength to resist the forces it encounters during operation without failing. Materials with higher strength-to-weight ratios, such as high-grade steels and certain alloys, are often preferred for high-load applications. For instance, carburized alloy steels provide high surface hardness and enhanced core strength, making them ideal for automotive transmissions.
- Wear Resistance: Gears operate in environments where they are in constant contact with other gears and components. The selected material must withstand friction and avoid wear over time, which would degrade the gear’s performance and lead to failure. Materials like bronze and certain polymers are chosen for their excellent wear properties in specific environments.
- Corrosion Resistance: In applications where gears are exposed to harsh environments, such as marine or chemical processing equipment, materials that can resist corrosion are essential. Stainless steels and nickel alloys are examples of materials that offer good corrosion resistance, thereby maintaining gear integrity and functionality over an extended period.
- Heat Resistance: During operation, gears generate significant amounts of heat due to friction. Materials that can withstand high temperatures without losing their mechanical properties are crucial, especially in high-speed or high-load applications. Advanced ceramics and heat-treated metals are often used in such scenarios.
- Manufacturability: The ease with which a material can be processed and manufactured into gears affects the overall cost and feasibility of production. Materials that are more ductile and less brittle, such as certain grades of steel, are easier to machine and can be formed into complex shapes more reliably.
- Cost-Effectiveness: Finally, the cost of the material plays a significant role in its selection. Gear manufacturer must balance performance requirements with economic feasibility. Materials that offer the best compromise between cost and performance, like cast iron for low-speed, low-load applications, are often chosen to optimize both production and operational budgets.
- Noise and Vibration Reduction: For applications where operational quietness is crucial, such as in automotive transmissions or aerospace systems, the material chosen for gear manufacturing can significantly influence noise and vibration levels. Materials with inherent damping properties, like certain polymers and composite materials, can reduce the noise generated during gear engagement. Additionally, fine-tuning the microstructure of metals through heat treatment or adding elements like vanadium can improve the damping characteristics of traditional gear materials.
- Thermal Expansion: Different materials expand at different rates when heated. In applications where gears must operate over a wide range of temperatures, selecting a material with a thermal expansion coefficient similar to that of mating components is crucial to maintain proper meshing and efficiency. For instance, Invar, an alloy with minimal thermal expansion, is used in applications requiring high dimensional stability.
- Environmental Impact: With increasing focus on sustainability, the environmental impact of material production and disposal is becoming a crucial factor in the selection process. Materials that are more environmentally friendly, such as those that are recyclable or require less energy to produce, are becoming more popular. For example, using recycled steel or aluminum can significantly reduce the carbon footprint of gear manufacturing.
- Customization for Specific Applications: Advances in material science have led to the development of specialized materials tailored for specific gear applications. For example, aerospace gears often use titanium alloys for their exceptional strength-to-weight ratio and corrosion resistance. In racing applications, gears might be made from advanced ceramics to handle extreme speeds and temperatures while minimizing weight.
- Surface Treatments and Coatings: Beyond the bulk material properties, surface treatments and coatings can dramatically enhance gear performance. Techniques such as nitriding, carburizing, and the application of diamond-like coatings can increase surface hardness, reduce wear, and extend the life of the gears. These treatments are particularly important in applications where the gears are subjected to extreme conditions.
- Integration with Digital Manufacturing Technologies: The integration of digital gear manufacturing technologies like 3D printing has opened new possibilities for using materials that were previously challenging to shape into complex gear geometries. 3D printing allows for the use of high-performance polymers and metal powders, enabling the creation of lightweight, high-strength gears that can be designed with intricate features impossible to achieve with traditional gear manufacturing methods.
- Predictive Maintenance: Material selection is also influenced by the integration of sensors and IoT technology in gears for predictive maintenance. Materials that can support these technologies allow for continuous monitoring of gear health, enabling preemptive maintenance actions that prevent costly downtimes.
- Lightweight and High-Performance Materials: As industries like automotive and aerospace push for reduced weight to achieve greater efficiency and lower emissions, the demand for lightweight yet high-performance materials continues to rise. Materials such as magnesium alloys, which are lighter than aluminum and steel, are gaining traction. Additionally, composite materials, which can be engineered to specific performance criteria, are becoming increasingly prevalent due to their ability to reduce weight without compromising strength or durability.
- Smart Materials and Technologies: The future of gear manufacturing is also looking at the incorporation of smart materials that can adapt their properties based on environmental or operational changes. Shape memory alloys and magnetorheological fluids are examples of materials that offer dynamic properties such as changing stiffness or damping in response to temperature or magnetic fields, respectively. These materials could revolutionize gear designs, especially in adaptive and highly automated systems.
- Improved Corrosion Resistance with Nanomaterials: Nanotechnology offers new ways to enhance corrosion resistance, a critical factor for gears used in harsh environments. Nano-coatings can provide a barrier that is highly resistant to corrosion and wear, extending the lifespan of gears significantly. Research into nanocomposite materials also shows promise for creating gears with self-healing capabilities, where small damages can be automatically repaired, thus reducing maintenance needs.
- Challenges in Material Recycling and Reusability: While the use of advanced materials brings many benefits, it also poses challenges in terms of recycling and sustainability. Many high-performance alloys and composites are difficult to recycle using conventional methods, which could lead to increased environmental impacts. Addressing these challenges requires innovations in recycling technologies or designing materials that are easier to separate and reuse.
- Global Supply Chain and Material Availability: The selection of materials is also affected by global supply chain dynamics. Availability, geopolitical factors, and price volatility of materials like rare earth elements, which are crucial for certain high-tech applications, can significantly impact material choices. Gear manufacturer need to consider these factors to ensure supply chain resilience and cost stability.
- Regulatory and Standards Evolution: As the global focus on sustainability intensifies, regulations regarding material sourcing, production, and disposal are becoming stricter. Gear manufacturer must not only choose materials based on performance but also consider the regulatory landscape. Adherence to international standards and certifications can become a deciding factor in material selection.
- Collaborative Research and Development: The complexity of modern gear systems and the materials used in them often exceeds the expertise of any single organization. Collaborations between universities, research institutions, and industry are crucial to drive forward the development of new materials and gear manufacturing technologies. These partnerships help in sharing risks, costs, and benefits, accelerating the pace of innovation.
In conclusion, the selection of appropriate materials in gear manufacturing is a complex decision-making process that impacts the performance, reliability, and lifecycle costs of gears. Advances in materials science continue to introduce new materials and treatments that offer improved properties for gear manufacturing, such as lightweight composites and surface coating technologies. By choosing the right materials, gear manufacturer can significantly enhance the performance and durability of their products.
The interplay of these factors highlights the critical role of material selection in modern gear manufacturing. As technology evolves, the choice of materials will continue to be influenced by a broader range of factors, including operational performance, gear manufacturing technologies, environmental impact, and economic considerations. Each advancement in material science not only extends the operational boundaries of gears but also drives innovations in the industries they serve.