Quality control in gear manufacturing is a critical aspect of the production process to ensure that the gears meet specified requirements and perform reliably in their applications. Here are the key components of quality control in this field:
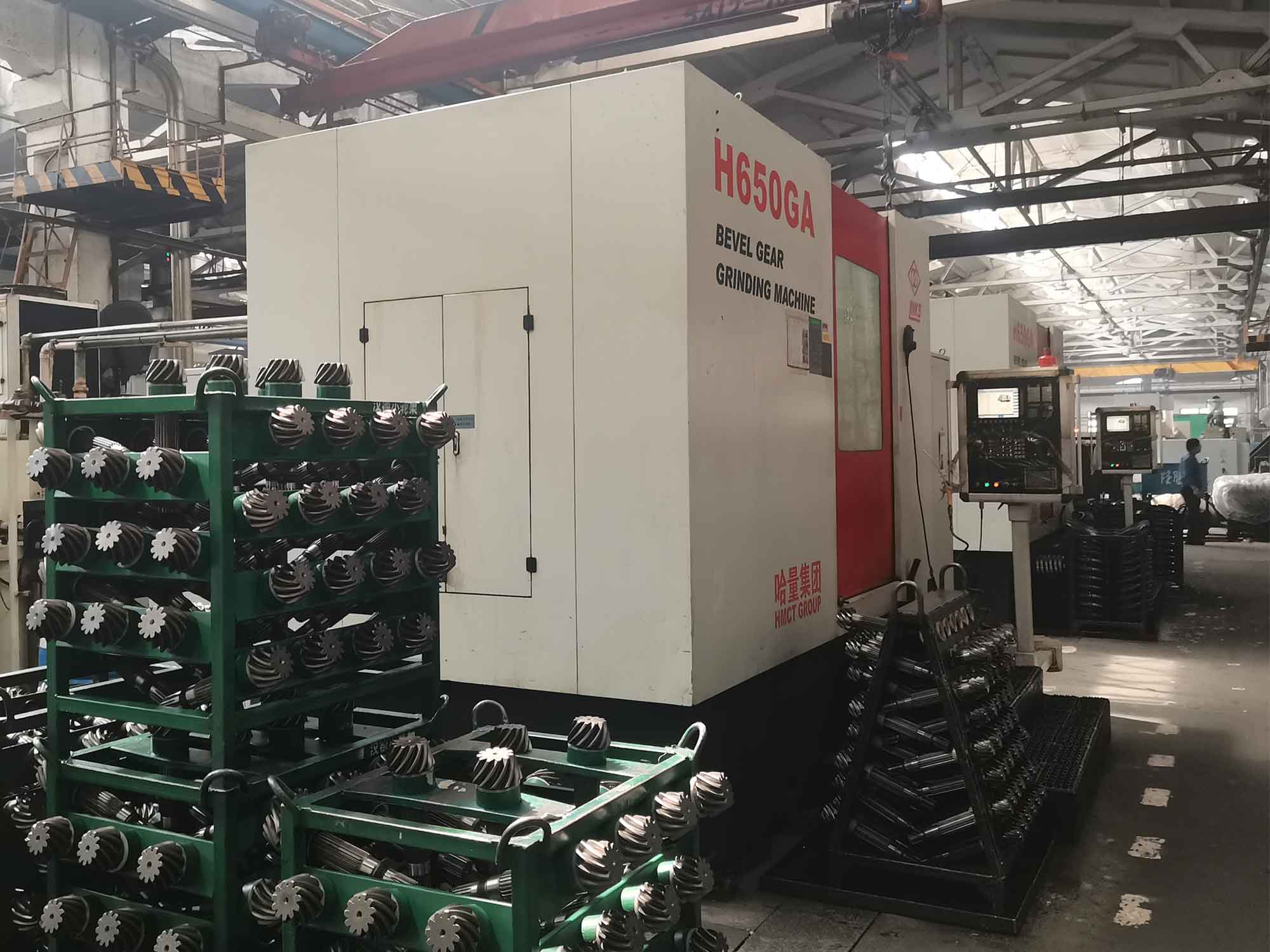
- Material Inspection: Before any manufacturing begins, the materials used to make gears (such as steel, brass, or composite materials) are inspected to ensure they meet the necessary specifications for purity, strength, and suitability.
- Dimensional Accuracy: Precision in gear manufacturing is crucial. Measurements are taken throughout the production process to ensure that each gear’s dimensions meet the precise specifications. This includes checking diameters, tooth size and shape, and overall geometry.
- Surface Quality: The surface finish of a gear can greatly affect its performance and longevity. Surface roughness is measured, and gears are inspected for any imperfections that might lead to premature wear or failure, such as scratches or pits.
- Hardness Testing: Gears often undergo hardness testing to ensure the material has the correct properties for durability and resistance to wear. Techniques such as Rockwell or Brinell hardness tests may be employed.
- Tooth Contact Analysis: Advanced quality control measures include checking the contact pattern between the teeth of the gears under load conditions. This helps in predicting how the gears will perform in real-world applications.
- Noise and Vibration Testing: Gears should operate smoothly and quietly. Testing for noise and vibration during operation can indicate if there are issues with how the gears mesh or if there are defects in the material or gear manufacturing process.
- Statistical Process Control (SPC): Many gear manufacturers use SPC to monitor and control the quality of their gear manufacturing processes statistically. This approach helps in identifying trends and deviations in real-time, allowing for immediate corrections.
- Final Inspection and Testing: After the gears are manufactured, they undergo a final comprehensive inspection. This includes a repeat of all the tests performed during the earlier stages of production, ensuring that the final product meets all specifications.
- Assembly Testing: If the gear is part of a larger assembly, it’s crucial to test the entire assembly to ensure that all components interact correctly. This testing can identify issues that might not be apparent when testing individual gears, such as alignment and interaction with adjacent parts.
- Lifetime Testing: To simulate long-term usage, gears may undergo accelerated life testing. This involves running the gear at higher than normal speeds or loads to predict how long it will last under normal conditions. This testing helps in assessing the durability and the expected lifecycle of the gear.
- Certification and Compliance: Depending on the industry and application, gears might need to meet specific regulatory standards or certifications. For example, gears used in automotive or aerospace applications must adhere to strict industry standards regarding performance and safety. Compliance with such standards is verified through rigorous testing and documentation as part of quality control.
- Metrology Instruments: Utilizing advanced metrology instruments can enhance the accuracy of measurements during gear manufacturing process. Tools like coordinate measuring machines (CMM), gear testers, laser scanners, and micrometers provide precise readings that are critical for maintaining high-quality production.
- Traceability: Each gear is often given a unique identifier that allows its gear manufacturing history to be traced. This includes details about the material batch, machine settings, operator details, and inspection results. Traceability is essential for quality control, as it helps in pinpointing issues and preventing similar problems in future production batches.
- Feedback Loop: A robust feedback mechanism between the product testing team, gear manufacturing floor, and the design team is crucial. This ensures that any issues which are identified can be fed back into the design and gear manufacturing process to improve the product in continuous cycles.
- Training and Standards: Regular training for staff on the latest quality control techniques and industry standards is fundamental. Keeping the team updated with new technologies, materials, and methods ensures that quality control measures are effectively implemented and adhered to.
- Use of Software Tools: Many gear manufacturers employ specialized software tools for gear design and gear manufacturing that integrate quality control features. These tools can simulate gear performance, predict failures, and optimize manufacturing processes before actual production begins.
Implementing rigorous quality control measures in gear manufacturing helps in reducing the rate of failures, increases customer satisfaction, and reduces costs related to rework and warranty claims. Each step in the process is crucial for ensuring that the final product can perform effectively under the expected loads and conditions.