By increasing the installation center distance of the helical gear and introducing a fixed backlash value, the dynamic characteristics of the helical gear pair in the excitation system with an installation center distance of 330.308 1 mm will be further evaluated.
1. Dynamic fluctuation characteristics of center distance
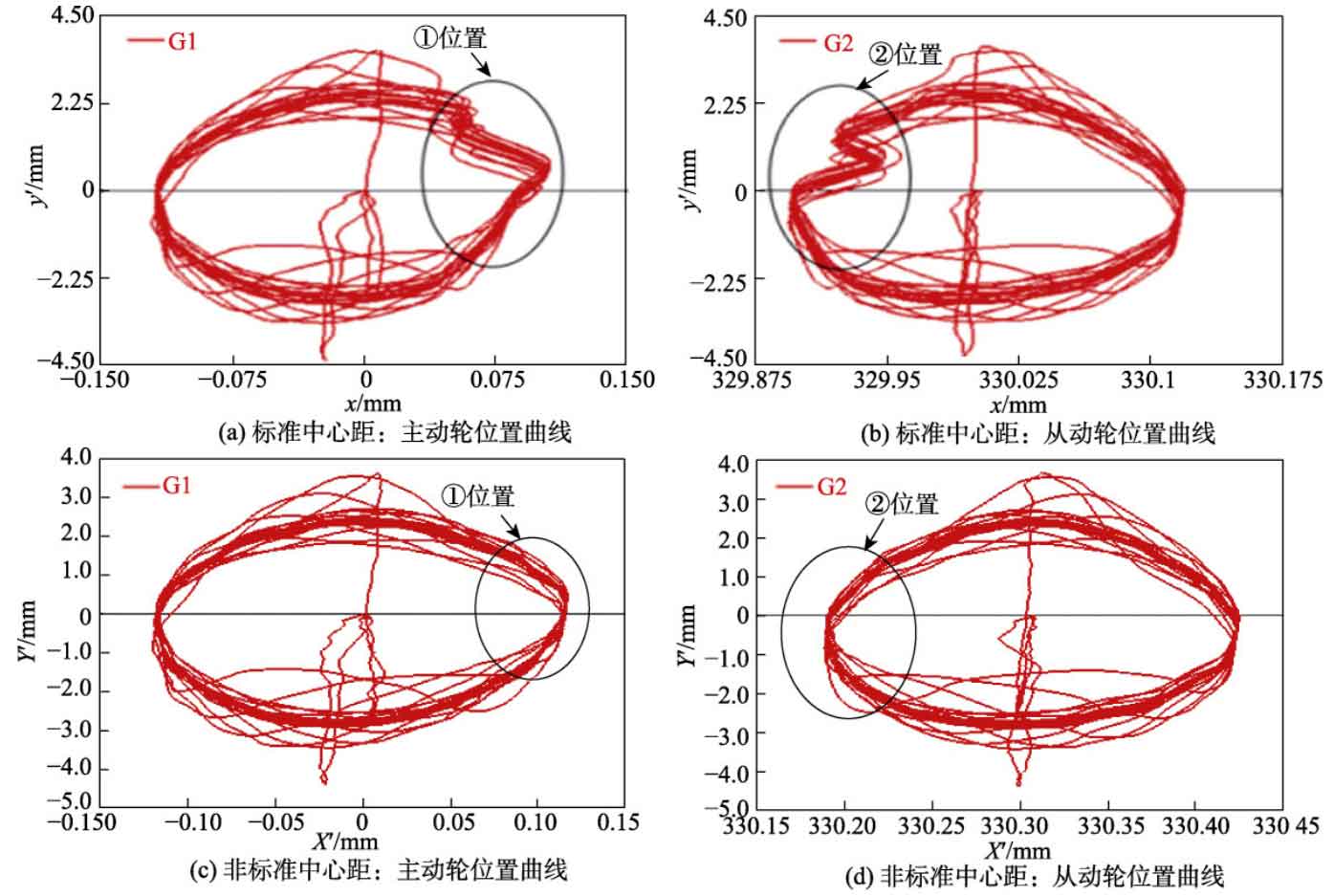
As shown in Figures 1 (a) and (b), the rotating center of the exciter helical gear installed with standard center distance has already moved along the edge of the bearing clearance in the x ‘direction, which is prone to frequent tooth squeezing and large tooth side clearance. The strong curve fluctuations at positions ① and ② are caused by the helical gear tooth squeezing impact. Figures 1 (c) and (d) show the rotation center trajectory of the helical gear with non-standard center distance installation, which is approximately an ellipse. There is no significant fluctuation caused by tooth squeezing collision at positions ① and ②.
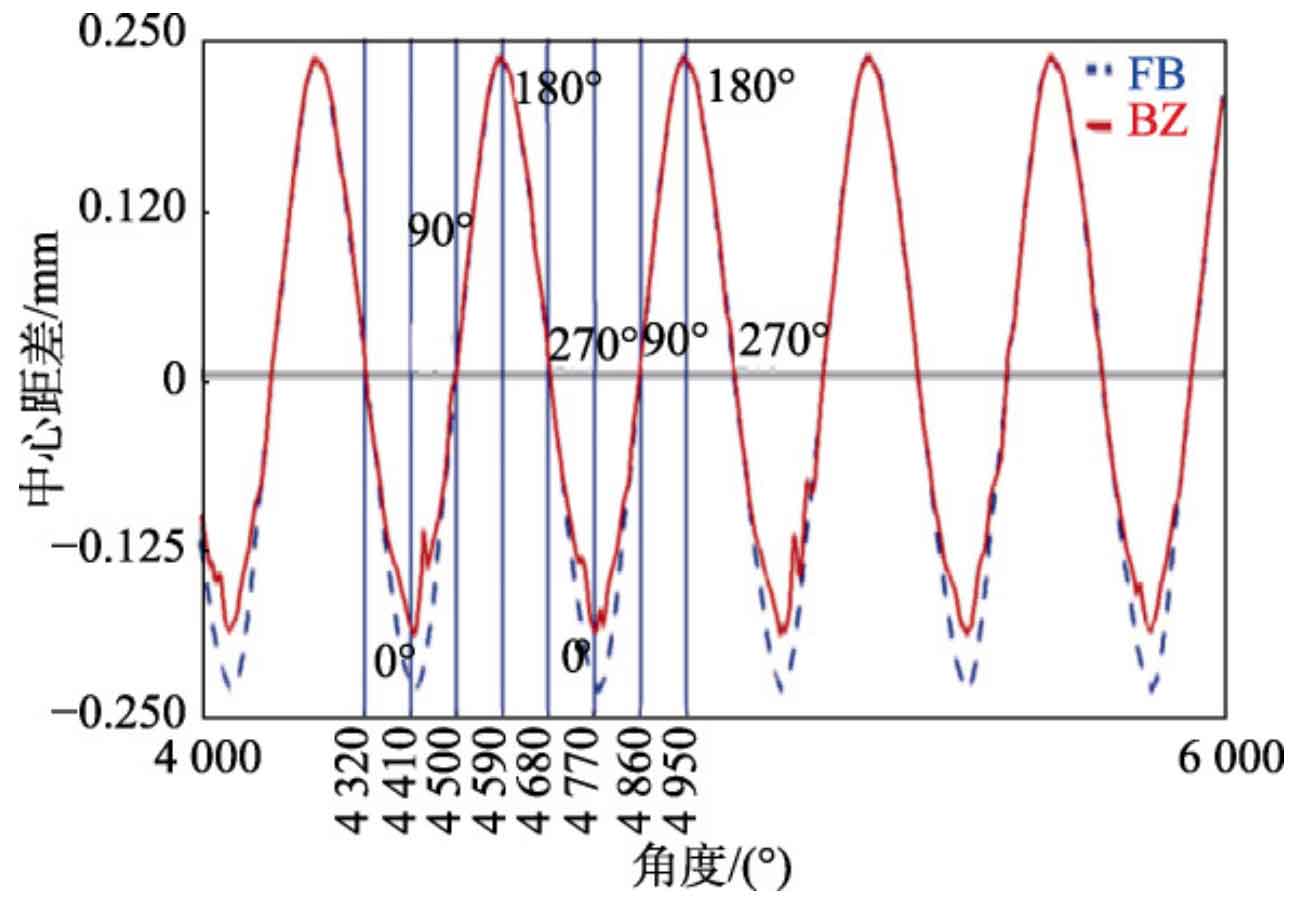
As shown in Figure 2, the maximum fluctuation value of the difference between the actual center distance and the non-standard center distance (blue dashed line) is 0.234 mm, which is the same as the maximum fluctuation value at the standard center distance (red solid line), but the minimum fluctuation value is -0.232 1 mm, and the fluctuation amplitude is less than the increased center distance of 0.305 7 mm. There will be no tooth squeezing phenomenon, which verifies the fatigue life analysis in Figure 3. Due to the lack of suppression effect of tooth squeezing, the fluctuation amplitude of the helical gear in the negative direction is greater when the non-standard center distance is used, and the fluctuation amplitude is close to the positive direction, which also proves the rationality of the entire process.

2. Analysis of the impact of dynamic characteristics
Figure 4 shows the vibration response curves of the exciter helical gear under standard center distance in the x, y, and z directions. From the time domain (Figure 4 (a), (b), and (c)), it can be seen that the helical gear undergoes periodic vibrations in all three directions that approximate harmonic laws, with severe fluctuations and obvious “impact” characteristics; From the frequency domain (Figure 4 (d), (e), and (f)), the main frequency components are the meshing frequency GMF and its harmonics of the helical gear. There are also obvious rotational frequencies Fr and its harmonics on the x and y vibration acceleration curves, with the maximum amplitude of the rotational frequency, which is mainly caused by the complex motion of the excitation system. In addition, the meshing frequency of helical gears and its harmonics are symmetrically distributed on both sides of the sidebands caused by rotational frequency modulation, and these frequency domain components belong to the irregular jitter caused by the meshing impact of helical gears.
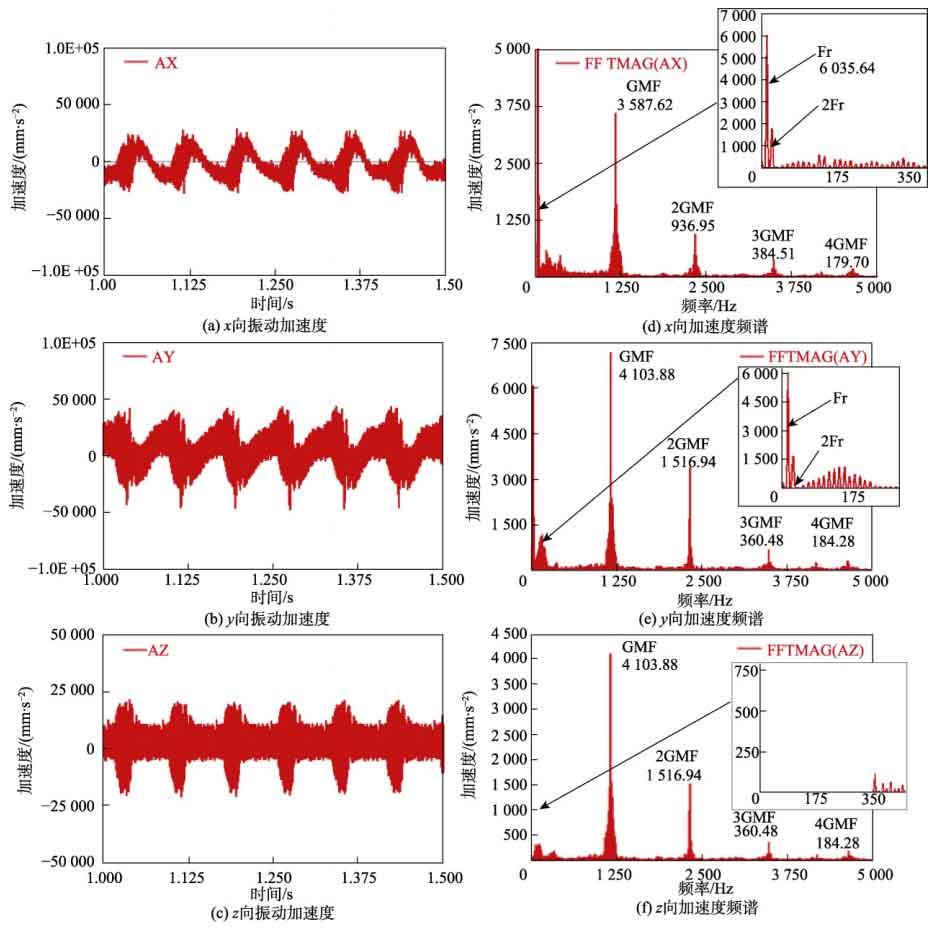
In contrast, under non-standard center distance (see Figure 5), the vibration of the exciter helical gear still exhibits an approximate harmonic pattern in three directions, but there is no strong “impact”, and the vibration fluctuation is significantly reduced; From the frequency domain analysis, the main frequency domain components are the same as the standard center distance, but no obvious sidebands can be seen on both sides of the rotational and meshing frequencies and their harmonics. Therefore, non-standard center distance can effectively improve the dynamic response characteristics of the exciter helical gear.
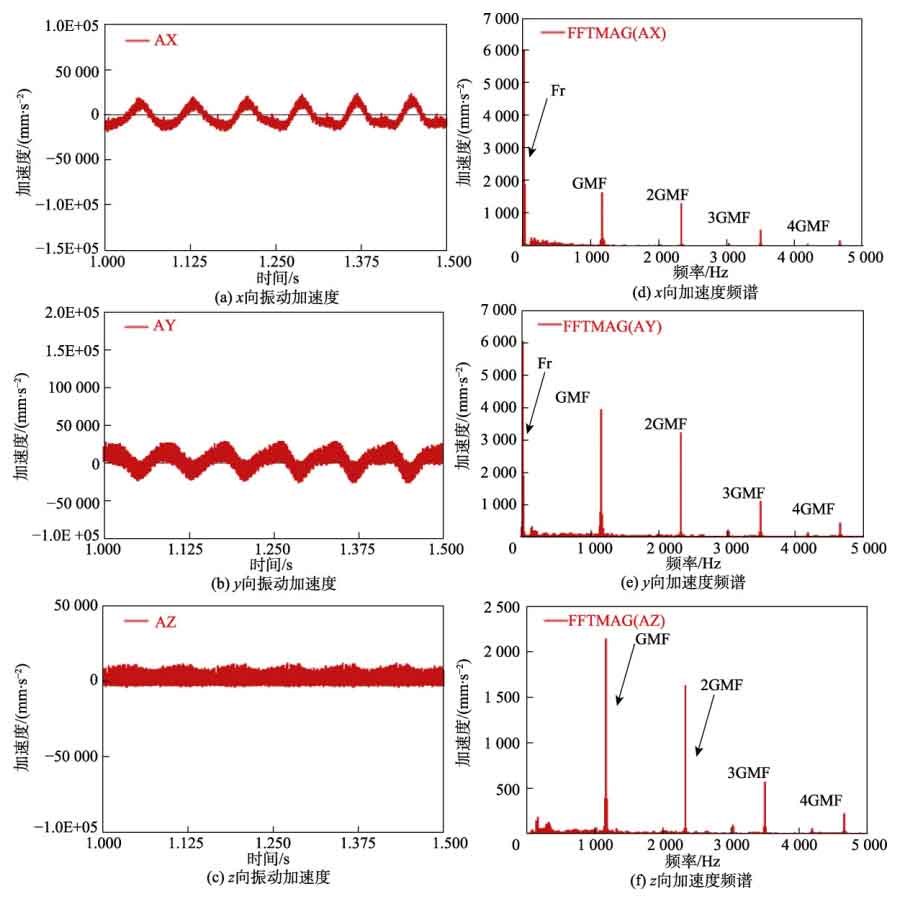
Figure 6 shows the dynamic characteristics of the normal meshing force of the exciter helical gear under standard and non-standard center distances. The red lines represent the normal meshing force of the helical gear, and the blue lines represent the fluctuation of the actual center distance of the helical gear compared to the theoretical center distance. It can be seen that when the center distance fluctuates to the minimum, there is a significant peak in the meshing force of the standard center distance helical gear pair. However, increasing the center distance reduces the meshing force value at this position, and the load change during the meshing process becomes more stable. In addition, it can be seen that the meshing force and acceleration vibration have the same time and frequency domain characteristics.
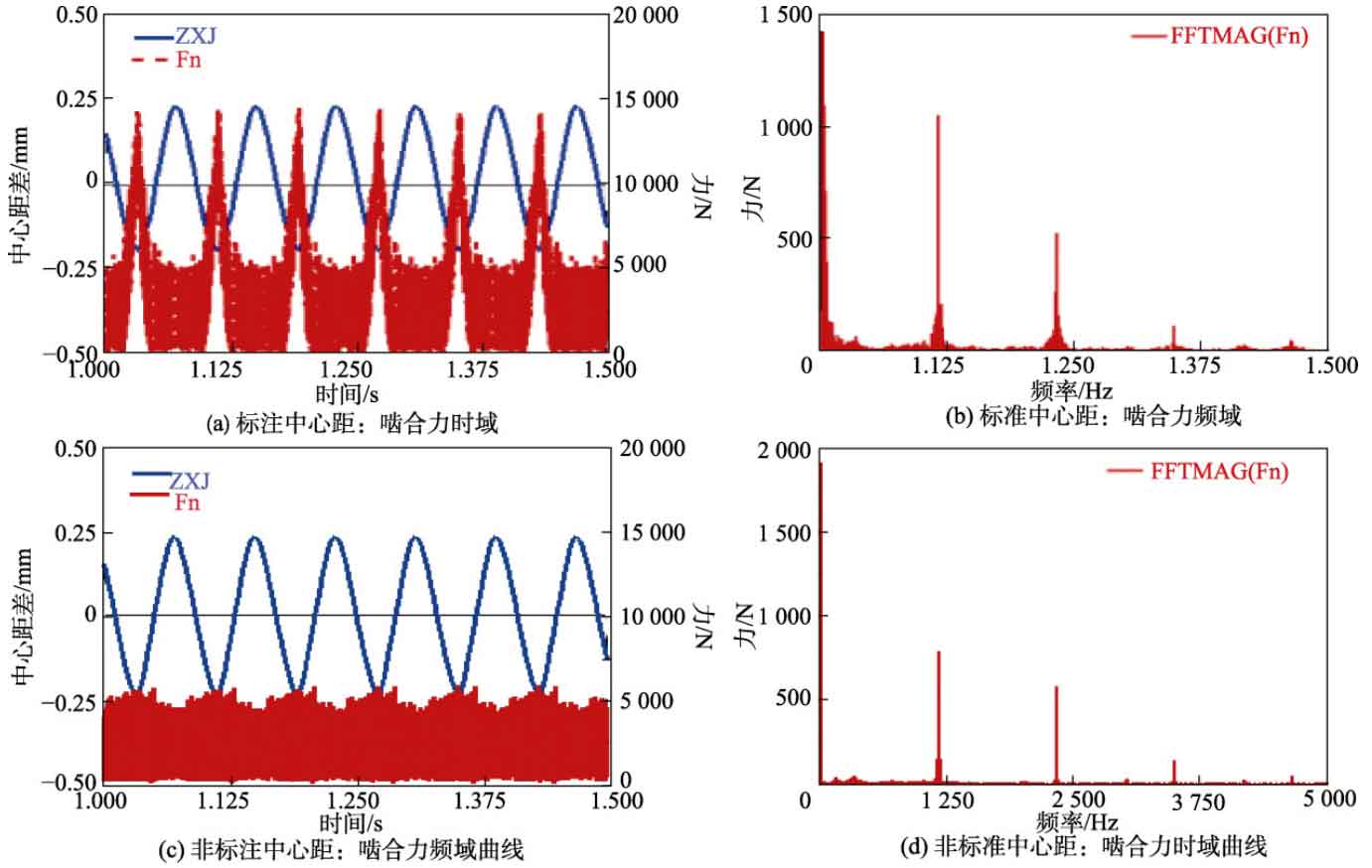
In summary, it can be concluded that increasing the center distance of the helical gear appropriately simplifies the time and frequency domain components of the acceleration signal and normal meshing force of the helical gear, and makes the meshing process of the helical gear smoother. Therefore, on the premise of not affecting the overall vibration law of the exciter, increasing the theoretical center distance appropriately can improve the meshing transmission performance of the mining vibrating screen exciter helical gear pair.