The optimal modification scheme of the top broken line arc of the long tooth profile is the modification amount of the driving gear 3 μ m. Modification amount of driven wheel 3 μ m。 Figure 1 shows the time varying meshing force curves before and after the helical gear pair is optimized and modified by the broken line arc at the tooth top of the long tooth profile under different speeds. Although this scheme has a certain effect on the reduction of the time varying meshing force of the helical gear pair under medium speed and high speed conditions, the modified helical gear pair still has a serious meshing impact under low speed conditions.
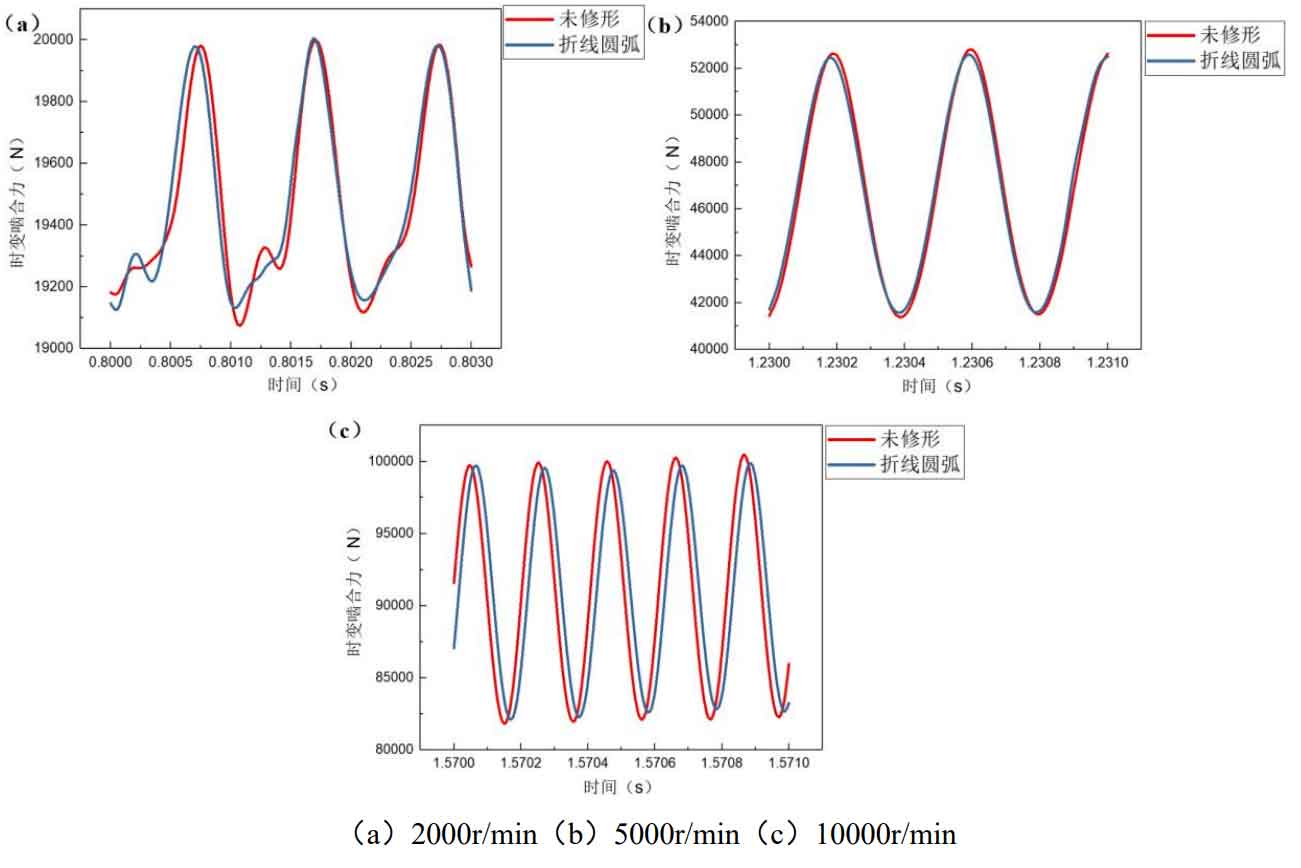
Figure 2 shows the time-varying meshing stiffness curves before and after the optimal modification of the helical gear pair through the long tooth profile and the tooth crest broken line arc. Obviously, the time-varying meshing stiffness of helical gears modified by this scheme has decreased to 4.89 × 108N/m, a decrease of 4.1%.
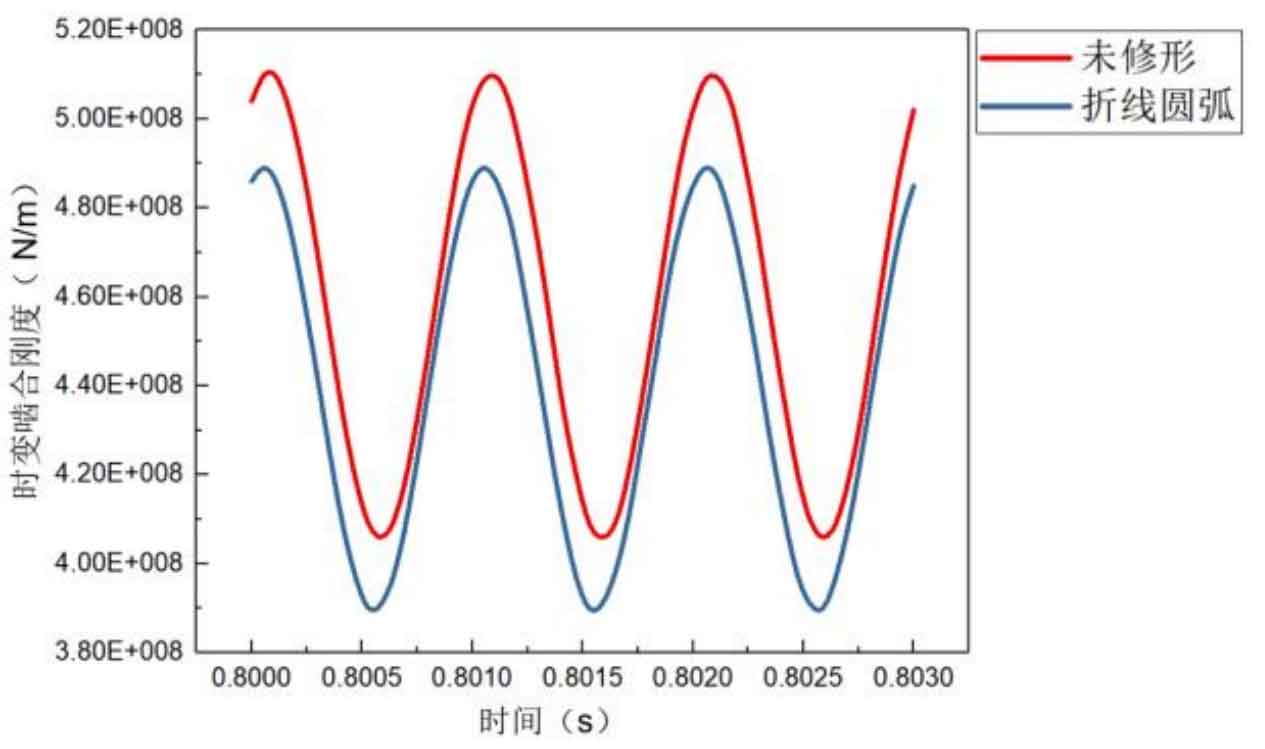
Therefore, on the whole, it can only be said that the internal dynamic excitation of the helical gear pair of the reducer of an electric vehicle has been improved, and the vibration and meshing impact of the helical gear have been alleviated.