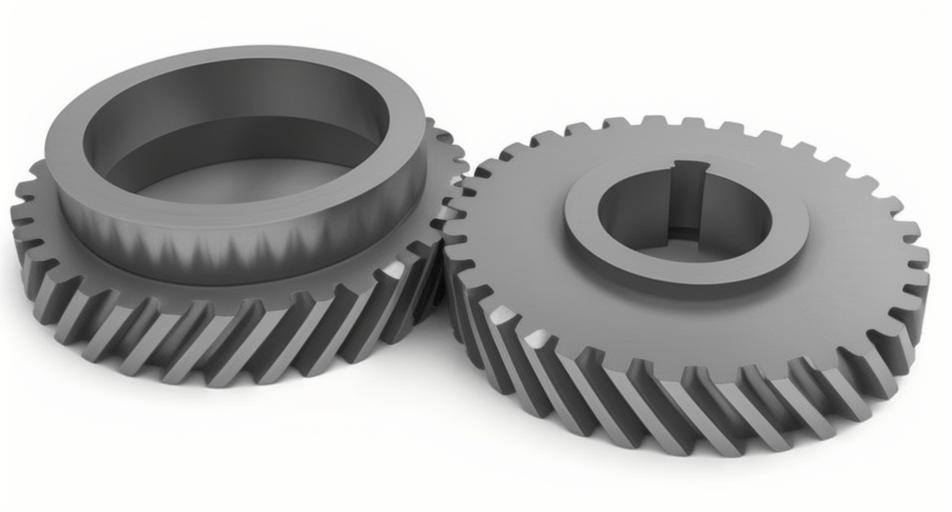
Mechanics of Helical Gear
Design and Structure
- Helix Angle: Helical gear is defined by the angle of the gear teeth. The helix angle, typically between 15° and 30°, determines the overlap and engagement of teeth.
- Tooth Engagement: The teeth of helical gear engage gradually along the helix angle, reducing noise and stress compared to spur gear.
- Axial Thrust: Due to the angled teeth, helical gear produce axial thrust along the shaft, requiring thrust bearings to counteract this force.
- Materials: Common materials include steel, cast iron, brass, and plastic, depending on the application and required strength.
Operation
- Efficiency: Helical gear operate more smoothly and quietly than spur gear, with less vibration due to the gradual engagement of teeth.
- Load Distribution: The load is distributed over multiple teeth, improving strength and reducing wear.
- Direction of Rotation: Helical gear can change the direction of rotation based on the helix angle and configuration (parallel or crossed).
- Lubrication: Proper lubrication is essential to minimize friction and wear, enhancing the lifespan of helical gear.
Applications of Helical Gear
Industrial Machinery
- Conveyors: Helical gear is widely used in conveyor systems due to their ability to handle heavy loads and provide smooth operation.
- Mixers and Agitators: The high efficiency and load distribution properties make them suitable for mixing and agitation processes in various industries.
Automotive
- Transmission Systems: Helical gear is commonly used in automotive transmissions, where quiet operation and high efficiency are crucial.
- Differentials: In differentials, they help in smoothly transferring power to the wheels, enhancing driving comfort and vehicle performance.
Robotics
- Precision Movement: The smooth and accurate motion provided by helical gear is ideal for robotic arms and other precision machinery.
- Load Bearing: Their ability to handle high loads makes them suitable for various robotic applications, from industrial robots to automated guided vehicles (AGVs).
Aerospace
- Engine Components: Helical gear is used in various aerospace applications, including jet engines, where reliability and efficiency are paramount.
- Landing Gear Systems: The load-bearing capability and smooth operation of helical gear is essential for the landing gear systems of aircraft.
Power Generation
- Wind Turbines: Helical gear is employed in wind turbine gearboxes, where they handle high torque and ensure efficient power transmission.
- Hydroelectric Plants: They are also used in hydroelectric power plants to transmit power from turbines to generators.
Consumer Electronics
- Printers and Copiers: Helical gear provide quiet and smooth operation in devices like printers and copiers, enhancing user experience.
- Household Appliances: In appliances like washing machines and blenders, they ensure reliable and efficient performance.
Advantages and Disadvantages
Advantages
- Smooth Operation: Reduced noise and vibration compared to spur gear.
- High Load Capacity: Ability to handle higher loads due to the load distribution across multiple teeth.
- Durability: Enhanced durability and lifespan due to gradual engagement and reduced wear.
Disadvantages
- Axial Thrust: Requires additional components like thrust bearings to manage axial forces.
- Complex Manufacturing: More complex to manufacture compared to spur gear, leading to higher costs.
- Lubrication Needs: Requires consistent and proper lubrication to maintain efficiency and longevity.
Conclusion
Helical gear is crucial component in modern machinery, offering numerous benefits such as smooth operation, high load capacity, and durability. Their applications span various industries, from automotive to aerospace, highlighting their versatility and importance in both heavy industrial machinery and consumer electronics. Despite their disadvantages, the advantages of helical gear make them a preferred choice in many applications where performance and reliability are critical.