Helical gear is a type of cylindrical gear with helix-shaped teeth. They are widely used in various mechanical systems for their unique advantages over straight-cut or spur gear. Here’s an overview of their mechanics, advantages, and applications:
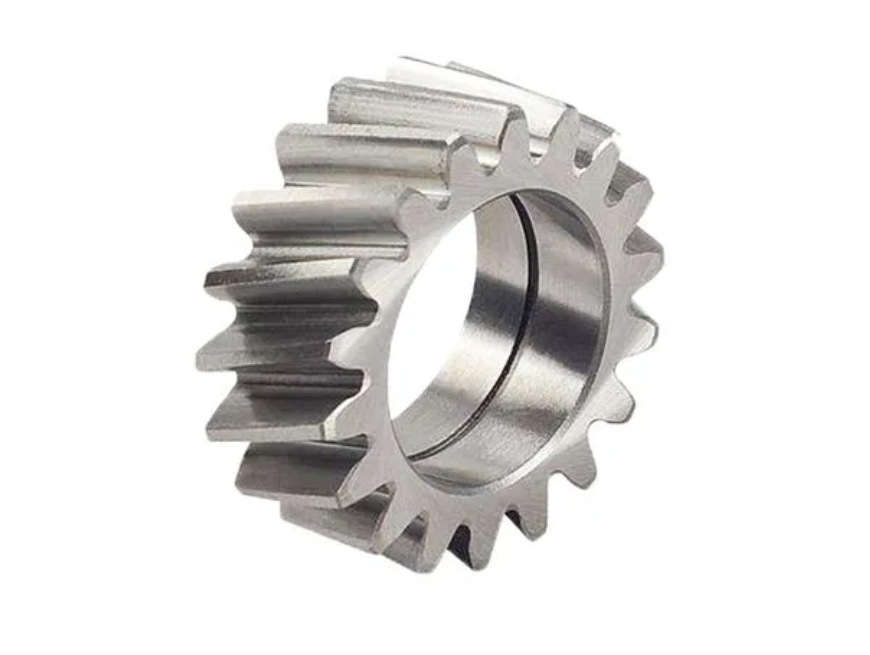
Mechanics of Helical Gear
- Helix Angle: The teeth of helical gear are cut at an angle (the helix angle) to the gear’s axis. This angle is crucial in determining the gear’s characteristics and performance.
- Meshing Process: Unlike spur gear which mesh with their entire width at once, helical gear mesh gradually. The contact starts at one end of the tooth and progressively spreads along the tooth as the gears rotate.
- Load Distribution: Due to the angled teeth, the load is distributed over several teeth. This results in smoother operation and reduced stress on each tooth.
- Axial Thrust: Helical gear generate axial thrust – a force along the axis of the gear. This necessitates the use of thrust bearings to absorb these forces.
- Right-Handed vs. Left-Handed: Helical gear can have right-handed or left-handed helix angles, and gear with opposite hands mesh together.
Advantages
- Quiet Operation: Due to the gradual engagement of the teeth, helical gear operate more quietly and smoothly than spur gear, making them ideal for high-speed applications.
- Higher Load Capacity: The extended surface contact between teeth allows helical gear to handle heavier loads.
- Longer Lifespan: Even distribution of forces leads to less wear and tear, thereby extending the gear’s lifespan.
- Higher Speeds and Torque Transmission: They are suitable for transmitting motion and power between parallel or right-angle shafts, especially at higher speeds.
Disadvantages
- Axial Thrust: The axial forces require additional bearing support, which can complicate the design and increase costs.
- Efficiency Loss: Due to the sliding contact of the teeth, there can be more friction and heat generation, leading to slightly lower efficiency compared to spur gear.
Applications
- Automotive Transmissions: Helical gear are commonly used in car transmissions for their smooth operation and ability to handle varying loads.
- Machinery: In industrial machines, helical gears are preferred for their durability and quiet operation.
- High-Speed Applications: Equipment like turbines and jet engines use helical gear to handle high rotational speeds.
- Consumer Electronics: In devices like printers and office equipment, their quiet operation is a significant advantage.
- Power Transmission Systems: They are used in various systems where smooth power transmission is essential.
In summary, helical gear offer smoother and quieter operation with higher load capacity, making them a preferred choice in many applications, albeit with the added complexity of managing axial thrust and slightly reduced efficiency.