Introduction
Helical gear plays crucial role in modern mechanical engineering, providing the essential functionality required for a wide range of mechanical systems. The unique design and characteristics of helical gear makes them ideal for applications demanding high efficiency, smooth operation, and the ability to handle significant loads. This article delves into the importance of helical gear in contemporary mechanical engineering, exploring their applications, advantages, and technological advancements.
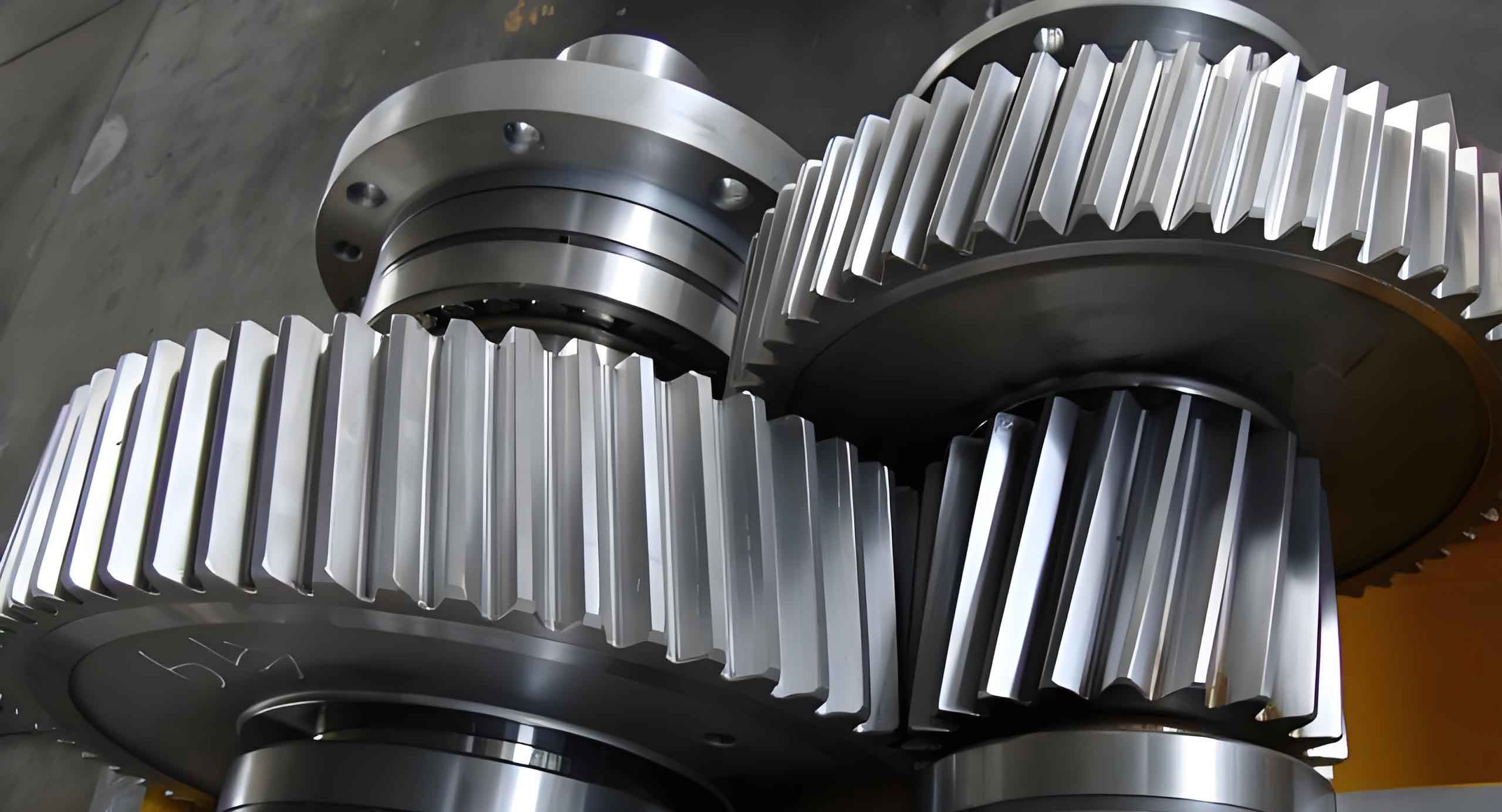
Characteristics of Helical Gear
Helical gear is characterized by their angled teeth, which are cut at an angle to the axis of rotation. This design offers several key advantages over other types of gears, such as spur gear, making helical gear preferred choice in many engineering applications.
Advantages of Helical Gear:
- Smooth Operation: The angled teeth of helical gear engage gradually, resulting in smoother and quieter operation.
- High Load Capacity: Helical gear can handle greater loads due to the increased tooth contact area.
- Efficiency: Helical gear provide efficient power transmission with minimal losses.
- Durability: The design of helical gear enhances their durability and longevity.
Applications of Helical Gear
Helical gear is utilized in a wide variety of applications across numerous industries. Their versatility and performance characteristics make them indispensable in modern mechanical engineering.
Automotive Industry
- Transmissions: Helical gear is commonly used in automotive transmissions to provide smooth and efficient gear changes.
- Differentials: Helical gear in differentials help distribute torque between the wheels, enhancing vehicle stability and performance.
Aerospace Industry
- Engines: Helical gear is used in aircraft engines for reliable power transmission and efficient operation.
- Landing Gear Systems: Helical gear ensure the safe deployment and retraction of landing gear in aircraft.
Industrial Machinery
- Conveyors: Helical gear is employed in conveyor systems for efficient and reliable power transmission.
- Mixers and Agitators: Helical gear ensure smooth operation in industrial mixing applications, enhancing process efficiency.
Renewable Energy
- Wind Turbines: Helical gear is used in the gearboxes of wind turbines to optimize power generation and ensure smooth operation.
- Hydropower Plants: Helical gear plays vital role in the efficient operation of hydropower generation systems.
Technological Advancements in Helical Gear Manufacturing
The manufacturing of helical gear has seen significant advancements, driven by the need for improved performance and efficiency in mechanical systems. These advancements have revolutionized the way helical gear is designed, produced, and utilized.
Precision Gear Grinding
Precision gear grinding has become a cornerstone of helical gear manufacturing. The use of advanced computer numerical control grinding machines allows for the production of helical gear with unparalleled accuracy and consistency.
Benefits of Precision Gear Grinding:
- Enhanced Accuracy: High levels of precision in gear tooth profiles.
- Improved Surface Finish: Smoother surfaces lead to quieter operation and longer gear life.
- Consistent Quality: Automated processes ensure uniform quality in large production runs.
Advanced Materials
The development of advanced materials has significantly impacted helical gear manufacturing. Materials such as alloy steels and composite materials offer enhanced strength, durability, and resistance to wear and corrosion.
Examples of Advanced Materials:
- Alloy Steels: Provide high strength and toughness for heavy-duty applications.
- Composite Materials: Lightweight with excellent wear resistance and reduced friction.
Additive Manufacturing
Additive manufacturing, or 3D printing, has introduced new possibilities in helical gear manufacturing. This technology enables the production of complex gear geometries that were previously difficult or impossible to achieve.
Advantages of Additive Manufacturing:
- Design Flexibility: Creation of intricate gear designs with optimized performance characteristics.
- Reduced Lead Times: Faster prototyping and production processes.
- Cost-Effective: Minimizes material waste and reduces tooling costs.
Advanced Heat Treatment Processes
Heat treatment is essential in enhancing the mechanical properties of helical gear. Advanced processes such as induction hardening and vacuum carburizing improve gear performance and longevity.
Key Heat Treatment Processes:
- Induction Hardening: Provides localized hardening, increasing wear resistance and fatigue strength.
- Vacuum Carburizing: Enhances surface hardness while maintaining core toughness.
CAD/CAM Integration
The integration of computer-aided design and computer-aided manufacturing software has transformed helical gear manufacturing. These tools facilitate precise gear design, simulation, and production planning.
Benefits of CAD/CAM Integration:
- Accurate Gear Modeling: Detailed design of gear tooth profiles and geometries.
- Simulation Capabilities: Prediction and optimization of gear performance under various conditions.
- Efficient Production Planning: Streamlines manufacturing processes, reducing errors and improving productivity.
Comparative Analysis of Manufacturing Techniques
Manufacturing Technique | Precision | Material Efficiency | Lead Time | Cost |
---|---|---|---|---|
Traditional Machining | Moderate | Moderate | Long | High |
CNC Grinding | High | High | Moderate | Moderate |
Additive Manufacturing | High | Very High | Short | Moderate |
Advanced Heat Treatment | High | High | Moderate | Moderate |
Conclusion
Helical gear plays vital role in modern mechanical engineering, offering superior performance, efficiency, and durability in a wide range of applications. The advancements in helical gear manufacturing, including precision gear grinding, the use of advanced materials, additive manufacturing, advanced heat treatment processes, and CAD/CAM integration, have significantly enhanced the capabilities and applications of helical gear. As technology continues to evolve, the role of helical gear in mechanical engineering will only become more critical, driving progress and innovation in various industries.