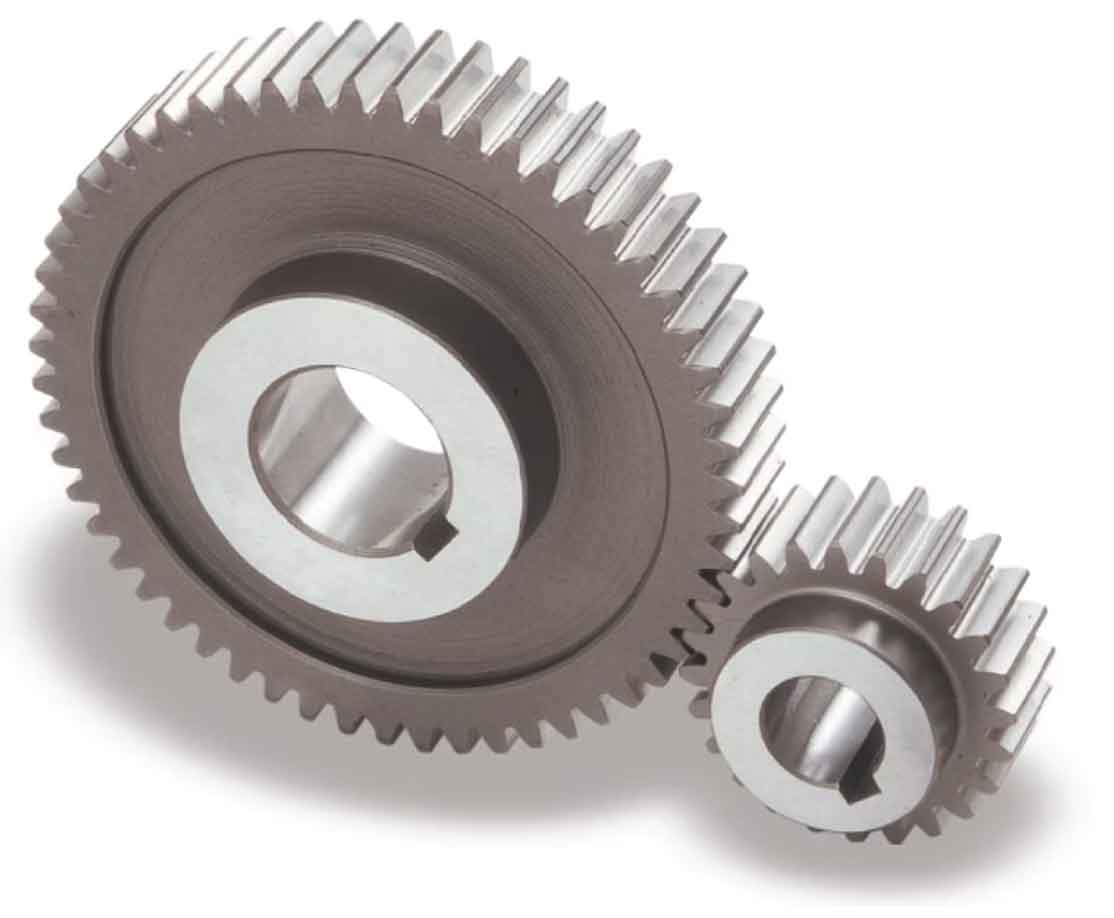
Spur gears play a vital role in automotive engineering, driving innovation and enabling various mechanical systems within vehicles. They are one of the most common types of gears used in automotive applications due to their simplicity, reliability, and efficiency. Let’s explore the role of spur gears in automotive engineering and their impact on innovation.
- Power Transmission: Spur gears are primarily used for power transmission in automobiles. They transfer rotational motion and torque between different components, such as the engine, transmission, differential, and wheels. By meshing together, spur gears enable the transfer of power from the engine to the wheels, allowing the vehicle to move forward or backward.
- Gear Reduction: Spur gears are often used in gear reduction systems to achieve the desired speed and torque output. In automotive applications, gear reduction is essential for optimizing engine performance and improving fuel efficiency. By using different gear ratios, spur gears can convert the high-speed, low-torque output of the engine into lower-speed, higher-torque output at the wheels.
- Transmission Systems: Spur gears are found in manual transmissions and automatic transmissions alike. In manual transmissions, they facilitate gear shifting by engaging different gears with the rotating input shaft. In automatic transmissions, they form part of complex planetary gear systems that allow for smooth gear changes without manual intervention.
- Differential Mechanism: Spur gears are integral to the operation of the differential, a key component in automobiles. The differential allows the wheels on the same axle to rotate at different speeds, enabling smooth cornering and preventing wheel slippage. Spur gears within the differential distribute torque evenly between the wheels, ensuring optimal traction and stability.
- Noise and Vibration Control: Automotive engineers continually work to reduce noise and vibration levels in vehicles. Spur gears, when properly designed and manufactured, offer smooth and quiet operation. Advancements in gear tooth profile design, material selection, and manufacturing techniques have led to reduced gear noise, contributing to a more comfortable driving experience.
- Lightweight and Compact Designs: The ongoing pursuit of lightweight and compact automotive designs has driven innovation in gear manufacturing. Spur gears can be manufactured using lightweight materials such as aluminum or composite materials, reducing overall vehicle weight. Additionally, advanced manufacturing techniques like precision forging, powder metallurgy, and 3D printing enable the production of complex gear geometries with high strength and optimized weight.
- Electric Vehicle Applications: As the automotive industry shifts towards electric vehicles (EVs), spur gears continue to play a crucial role. In EVs, spur gears are used in the electric motor drivetrain to transmit power efficiently from the motor to the wheels. Moreover, EVs often utilize regenerative braking systems that require spur gears to engage and disengage power flow between the motor and the wheels, maximizing energy recapture.
- Advanced Materials and Coatings: The development of advanced materials and coatings has expanded the capabilities of spur gears. High-performance materials like carbon fiber composites, advanced polymers, and ceramics offer enhanced strength, durability, and wear resistance. Surface coatings and treatments further improve gear performance by reducing friction, enhancing lubrication, and preventing corrosion.
In conclusion, spur gears are essential components in automotive engineering, playing a significant role in power transmission, gear reduction, transmission systems, differential mechanisms, noise and vibration control, lightweight designs, electric vehicle applications, and the use of advanced materials. Continued innovation in spur gear design and manufacturing techniques contributes to overall vehicle performance, efficiency, and driver comfort in the ever-evolving automotive industry.