The friction coefficient of tooth surface is affected by many factors, which will change with meshing position, lubrication state and micro-morphology of tooth surface.To predict the time-varying friction coefficient of gears, researchers have used several friction coefficient prediction models on different occasions.
1 Coulomb friction model:
The Coulomb force model is the simplest one, and its friction coefficient does not change with the position of meshing contact point, only the direction of friction force changes at the joint:

Where Savg is the given coefficient of friction.
2 Smooth Coulomb Friction Model:
Duan’s research shows that the time-varying friction coefficient has a functional relationship with the slip-rolling ratio and the relative sliding rate near the joint is infinitely close to zero. It is necessary to smooth the Coulomb friction model and obtain the following:

3 Benedict & Kelly Model:
Benedict amp; Kelly model applies when lubrication is in the mixed lubrication state:

Among them, AVG is the average roughness between tooth surfaces, is the dynamic viscosity of lubricating oil, () s95S is the average roughness between tooth surfaces, () s95S is the dynamic roughness of lubricating oil, () s95t is the sliding speed at the engagement point, () e504t is the (e504 speed, () e95t is the coiling speed at the engagement point, which can be defined as follows:
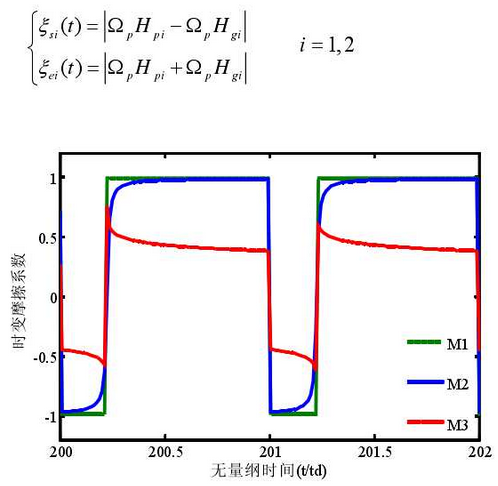
When Savg=0.991 is taken, the time-varying friction coefficients obtained by different friction models are compared as shown in the figure.The friction coefficients of the three models change direction at the gear joint, the Coulomb friction model (M1) changes abruptly at the joint, and the smooth model (M2) transits smoothly at the joint. The friction coefficients of the two models do not change with time, while Benedict amp;The Kelly model (M3) has the largest friction coefficient at the joint and there is a sudden change due to the change of direction. The friction coefficient decreases with the distance from the joint.The friction coefficient of model M3 is smaller than that of M1 and M 2.
According to the actual lubrication conditions, Benedict amp; Kelly model is mainly used for simulation analysis.It can be seen from the formula that when the gear parameters and operating conditions are fixed, the corresponding time-varying friction coefficient can be determined according to the tooth surface roughness.Based on the parameters and working conditions of type A gear in the table, the lubricant is ISO-VG-220 gear oil, the working temperature is 90 C, and the roughness AVG fraction avgS is 0.325um, 0.53um and 0.991um, respectively, to obtain the time-varying friction coefficient distribution as shown in the figure.It can be seen that as the roughness increases, the coefficient of friction increases, reaching its maximum at joint C.