Gao Yun used the finite element method to analyze the stress of gear, determined the position of the maximum principal stress at the root of the tooth, and regarded it as the starting point of fatigue crack. Then, the propagation path of the root crack in actual work was simulated and analyzed.In order to understand the time-varying engagement stiffness of gear with cracks and its variation with crack growth, the calculation and analysis of engagement stiffness is embedded into the simulation and analysis process of crack growth, and the variation rule of time-varying engagement stiffness of gear with fatigue crack growth of tooth roots is calculated.
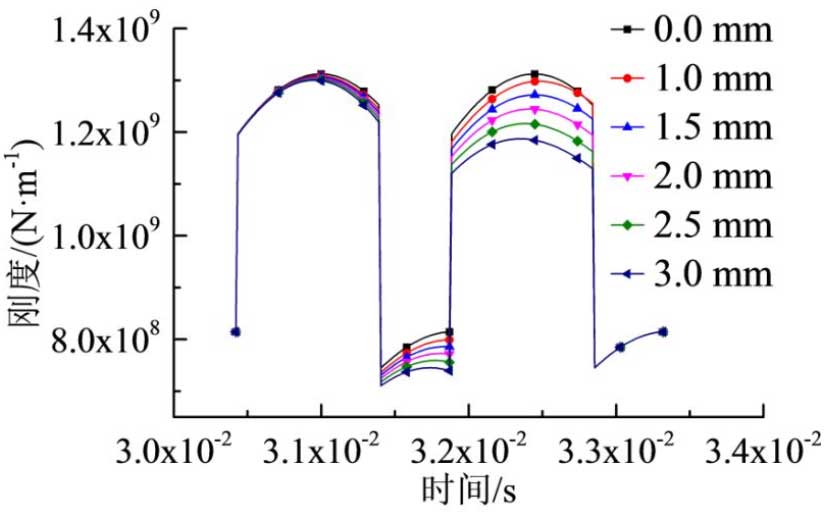
Cracks of different lengths are preset at the maximum principal stress position of the root of the first stage active gear, and then the model is calculated.The results show that the Hertz stiffness and the axial compression stiffness have not changed significantly compared with the calculation of the healthy gear stiffness.However, the moment of inertia of the root section changes significantly with the crack growth, and the bending and torsional stiffness of the gear changes synchronously.Figure shows the time-varying engagement stiffness of a gear system with different length cracks in two engagement cycles under 30 Hz input shaft rotation frequency and 48.8 N.m load.Within 3.0 x 10-2~3.4 x 10-2 s, the teeth with cracks undergo three engagement stages.The overall trend of engagement rigidity of cracked teeth is similar to that of healthy gears, but it decreases with the increase of crack length.During the meshing process, as the cracked teeth bear more and more loads, the range of stiffness change increases; when the cracked teeth bear all loads, the meshing stiffness of the cracked teeth decreases; when the cracked teeth rode out, the load on the cracked teeth decreases and the range of stiffness change decreases.