Hypoid gears are widely used in the transmission of vehicle drive axles due to their large contact ratio and smooth transmission. However, the control of their meshing performance is rather difficult due to the complex tooth surface and the cumbersome adjustment of machine tool processing parameters.
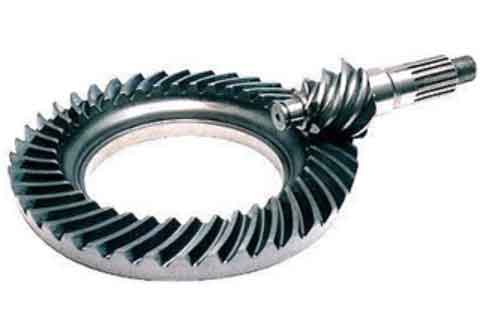
The meshing contact area of the tooth surface is related to the vibration, noise, and running stability of the gear. Due to the existence of processing errors and installation errors, there is a deviation between the actual tooth surface and the theoretical tooth surface. Adjusting the position of the contact area based on the rolling inspection results of the actual processing tooth surface and subsequently correcting the processing parameters is a key link in the control of the meshing performance of hypoid gears. Therefore, precise fitting of the tooth surface based on the measurement results of the actual tooth surface and analyzing the meshing performance is the prerequisite for adjusting and calculating the processing parameters of the tooth surface.
In this paper, based on the measurement results of the actual processing tooth points of hypoid gears, the actual tooth surface is reconstructed using the fitting method of double cubic NURBS surfaces. The discrete tooth surface contact analysis method is adopted to obtain the transmission error and meshing imprint of the real tooth surface, providing a basis for the evaluation of the processing quality and the correction of the processing parameters of hypoid gears.
1. Actual Tooth Surface Fitting
According to the measurement results of the actual tooth surface of hypoid gears, the deviation value δij of the tooth surface measurement points is superimposed with the three-dimensional coordinates of the theoretical tooth surface points to obtain the coordinates of the real tooth surface points, as shown in Equation (1): R_{i, j} = r_{i, j} + δ_{i, j} · n_{i, j}. Here, i and j are the grid point numbers in the tooth height direction and the tooth length direction, respectively; Ri,j and ri,j are the position vectors of the actual and theoretical tooth surface grid points, respectively; ni,j is the unit normal vector of the theoretical tooth surface grid point.
In order to conduct the actual tooth surface contact analysis, the double cubic NURBS surface construction method is used to reconstruct the actual tooth surface of the hypoid gear. The expression of the reconstructed tooth surface is given by Equation (2): S(u, v) = Σ_{i=0}^{n} Σ_{j=0}^{n} N_{i, 3}(u) N_{j, 3}(v) w_{i, j} K_{i, j} / Σ_{i=0}^{n} Σ_{j=0}^{n} N_{i, 3}(u) N_{j, 3}(v) w_{i, j}. In this equation, Ki,j is the control point of the reconstructed tooth surface; i and j are the numbers of the control points, with a total of (m + 1) × (n + 1); wi,j is the corresponding weight factor; N_{i, 3} and N_{j, 3} are the B-spline basis functions in the u-direction (tooth length direction) and v-direction (tooth height direction), respectively. Based on the measurement results of the tooth surface grid points, the control points of the NURBS curve are first calculated along the tooth height direction of the actual tooth surface, and then all the control points of the tooth surface are calculated along the tooth length direction to obtain the reconstructed real tooth surface.
According to the tooth surface measurement standard, the number of tooth surface grid points detected on the gear measuring center is (5 × 9). During the tooth surface contact analysis, in order to obtain the accurate position of the tooth surface meshing point, interpolation and encryption processing of the control points need to be carried out according to the accuracy requirements. As shown in Figure 1, the 45 control grid points can be subjected to double cubic spline interpolation processing to obtain the encrypted grid points.
2. Installation Distance Adjustment Calculation Model
The contact imprint of the actual tooth surface usually deviates from the pre-set position, as shown in Figure 2. M* and M0 are the actual and ideal contact positions, respectively, and the distance coordinate of M* deviating from M0 is (s, t). In the coordinate system (O0: X0, Y0), the coordinates of M* are (x∗ 2, y∗ 2), and there is the following relationship between this point and the three-dimensional tooth surface coordinates (x2, y2, z2) of M0 in the coordinate system (O2: X2, Y2, Z2):
{x2 cos γ2 + √(y2^2 + z2^2) sin γ2 – l_wD = x2^* + t
- x2 sin γ2 + √(y2^2 + z2^2) cos γ2 = y2^* + s}
Here, γ2 is the pitch cone angle of the large gear; lMD is the midpoint cone distance of the large gear tooth surface.
In order to obtain the correction of the processing parameters of the actual tooth surface, it is first necessary to adjust the position of the meshing point to obtain the adjustment amounts of the installation distance of the large gear, the installation distance of the small gear, and the offset distance when the contact point is at M0, and then convert them into the actual machine tool processing correction values.
Based on the rolling method of bevel gears, the tooth surface meshing relationship between the large gear and the small gear is established, as shown in Figure 3.
In Figure 3, (Of: Xf, Yf, Zf) is the fixed coordinate system; (O1: X1, Y1, Z1) and (O2: X2, Y2, Z2) are the follower coordinate systems fixed to the small gear and the large gear, respectively; ΔV, ΔH, and ΔJ are the adjustment amounts of the contact imprint position; V is the offset distance. In the fixed coordinate system, the meshing of the large and small gear tooth surfaces needs to satisfy the following relationship:
{r_f1(u1, v1, φ1, ΔV, ΔH, ΔJ) = r_f2(u2, v2, φ2)
n_f1(u1, v1, φ1, ΔV, ΔH, ΔJ) = n_f2(u2, v2, φ2)
∂r_f1/∂u1 · (∂r_f1/∂u2 × ∂r_f2/∂v2) = 0
∂r_f1/∂v1 · (∂r_f1/∂u2 × ∂r_f2/∂v2) = 0
n_f^(2) · v_f^(12) = f(u1, v1, φ1, u2, v2, φ2, ΔV, ΔH, ΔJ) = 0}
Here, r_f is the position vector of the meshing point; n_f is the unit normal vector of the meshing point; φ is the meshing rotation angle of the gear; u and v are the tooth surface parameters; the subscripts 1 and 2 indicate the small gear and the large gear, respectively; v_f^(12) is the relative motion speed of the large gear and the small gear at the meshing point. During the adjustment of the contact imprint position, it is necessary to keep the tooth side clearance constant, satisfying the following relationship: ΔJ + ΔH tan γ1 = 0. Here, γ1 is the pitch cone angle of the small gear.
Equations (4) and (5) contain multiple equations, which are represented by fd(X) (d = 1, 2,…, 9), respectively, and the solution quantities u1, v1, φ1, u2, v2, φ2, ΔV, ΔH, and ΔJ are represented by X. Since the measured tooth surface equation of the gear is composed of piecewise cubic spline surfaces, the conventional nonlinear solution method is difficult to solve. Using the Newton – Raphson iteration algorithm, the first-order partial derivatives of the 9 variables of the equation system fd are calculated respectively, and a 9 × 9 Jacobi matrix F'(X_kd) can be formed. Denoting the iteration number by k, the final solution of the equation system is [X_d^(h + 1)] = [X_d^h] – F'(X_d^h)^(-1)[f_d] (d = 1, 2,…, 9).
After cyclic iteration calculations, when ||X^(k + 1) – X^k|| < σ (σ is the solution accuracy), X^(k + 1) is the solution of the equation system, that is, the tooth surface coordinates at the meshing position. During the tooth surface contact analysis, this position is taken as the initial iteration point, and by continuously changing the rotation angles of the large gear and the small gear, other meshing points are solved to form the meshing trajectory of the tooth surface.
3. Actual Tooth Surface Contact Performance Analysis
The hypoid gear pair has point contact meshing. At the meshing point position, the distance between the tooth surfaces of the large gear and the small gear is 0, and the tooth surface distance gradually increases along the tooth length direction and the tooth height direction. When the density of the tooth surface grid points is sufficient to meet the solution accuracy requirements, by calculating the minimum distance min(Dp × q), the position of the tooth surface meshing point can be determined.
3.1 Tooth Surface Two-Dimensional Golden Section Encryption
In optimization algorithms, the golden section algorithm is simple, has a fast convergence speed, and has a significant effect. It is the basis of many optimization algorithms. The two-dimensional golden section method is based on the one-dimensional algorithm, which divides the feasible planar rectangular region in the two-dimensional direction at a ratio of 0.618 and 0.382, respectively. Then, the function values at the center of each small rectangle after division are compared, and the rectangular region where the minimum function value is located is continuously divided until the size of the rectangular region is smaller than the given accuracy. The convergence of the two-dimensional golden section has been strictly proven mathematically.
First, the initial meshing point positions of the large and small gears are calculated, and then according to the solution accuracy, the area near the meshing point is subjected to secondary or multiple two-dimensional golden section encryption. For different gear rotation angles, the meshing point that meets the accuracy requirements is sought. The tooth surface encryption process is shown in Figure 4.
3.2 Tooth Surface Meshing Interference Judgment
The meshing state of the tooth surface points is judged by whether the two tooth surfaces interfere with each other, that is, whether the inner product of the difference vector between the point Pij 2 on the tooth surface of the large gear and the point Pij 1 on the tooth surface of the small gear and the normal vector at the point Pij 1 is less than 0, which is expressed as Equation (8): S^{p × q} = n_{j 1}^{i j} · (r_{j 2}^{i j} – r_{j 1}^{i j}).
If min(Sp × q) < 0, then the tooth surfaces of the large gear and the small gear have meshing interference. The calculation process of the tooth surface meshing analysis is shown in Figure 5.
4. Example Analysis
According to the calculation process shown in Figure 5, the hypoid gear of a certain vehicle axle is calculated and solved. The basic parameters of the gear pair are shown in Table 1, and the measurement results of the tooth surfaces of the small gear and the large gear are shown in Figure 6.
According to the tooth surface meshing analysis solution process shown in Figure 5, the transmission error curve and contact imprint of the actual tooth surface are obtained, as shown in Figure 7(a). The contact imprint of the convex surface of the large gear is biased towards the large end. According to the position of the contact imprint, the approximate adjustment amount of the imprint is determined as follows: the moving distance t in the small end direction is 7 mm, and the moving distance s in the tooth top direction is 1 mm. Using Equation (6) to solve, the adjustment amounts of ΔV, ΔH, and ΔJ are obtained as 0.312 mm, -0.433 mm, and 0.062 mm, respectively. The contact analysis result of the adjusted tooth surface is shown in Figure 7(b). This adjustment amount can be converted into the corresponding correction amount of the machine tool processing parameters, such as tool position and wheel position correction. The specific method can refer to Reference [17], and will not be repeated here.
The purpose of the tooth surface rolling inspection is to check whether the position and shape of the actual tooth surface contact imprint meet the expected design requirements. In order to verify the correctness of this algorithm, the contact imprint rolling inspection results before and after the adjustment of the processing parameters are compared on the CNC rolling inspection machine, as shown in Figure 8. The contact imprint of the actual convex surface of the large gear shown in Figure 8(b) is consistent with the result of the simulation analysis. The position of the tooth surface contact area after the correction of the processing parameters of the small gear concave surface shown in Figure 8(c) is that the contact area has moved from the large end of the convex surface of the large gear to a position close to the midpoint of the tooth surface. The theoretical analysis is consistent with the actual processing rolling inspection result, which verifies the correctness of the model established in this paper.
5. Conclusions
(1) Based on the measurement results of the actual tooth surface of hypoid gears, the tooth surfaces of the large and small gears are reconstructed using double cubic NURBS surfaces. Based on the two-dimensional tooth surface golden section encryption method, the contact performance analysis algorithm of the actual tooth surface is compiled, and this algorithm can be used to quickly solve the tooth surface meshing trajectory, avoiding the cumbersome solution of nonlinear equation systems.
(2) The meshing performance analysis algorithm of the actual tooth surface can replace the traditional rolling inspection test, and the corresponding tooth surface processing parameters can be inversely adjusted and corrected through the adjustment calculation results of the contact area.
(3) Taking the hypoid gear pair of a certain vehicle axle as an example for rolling inspection verification, it shows that the contact imprint of the actual tooth surface is basically consistent with the actual rolling inspection result, which verifies the correctness of the actual tooth surface meshing analysis algorithm.