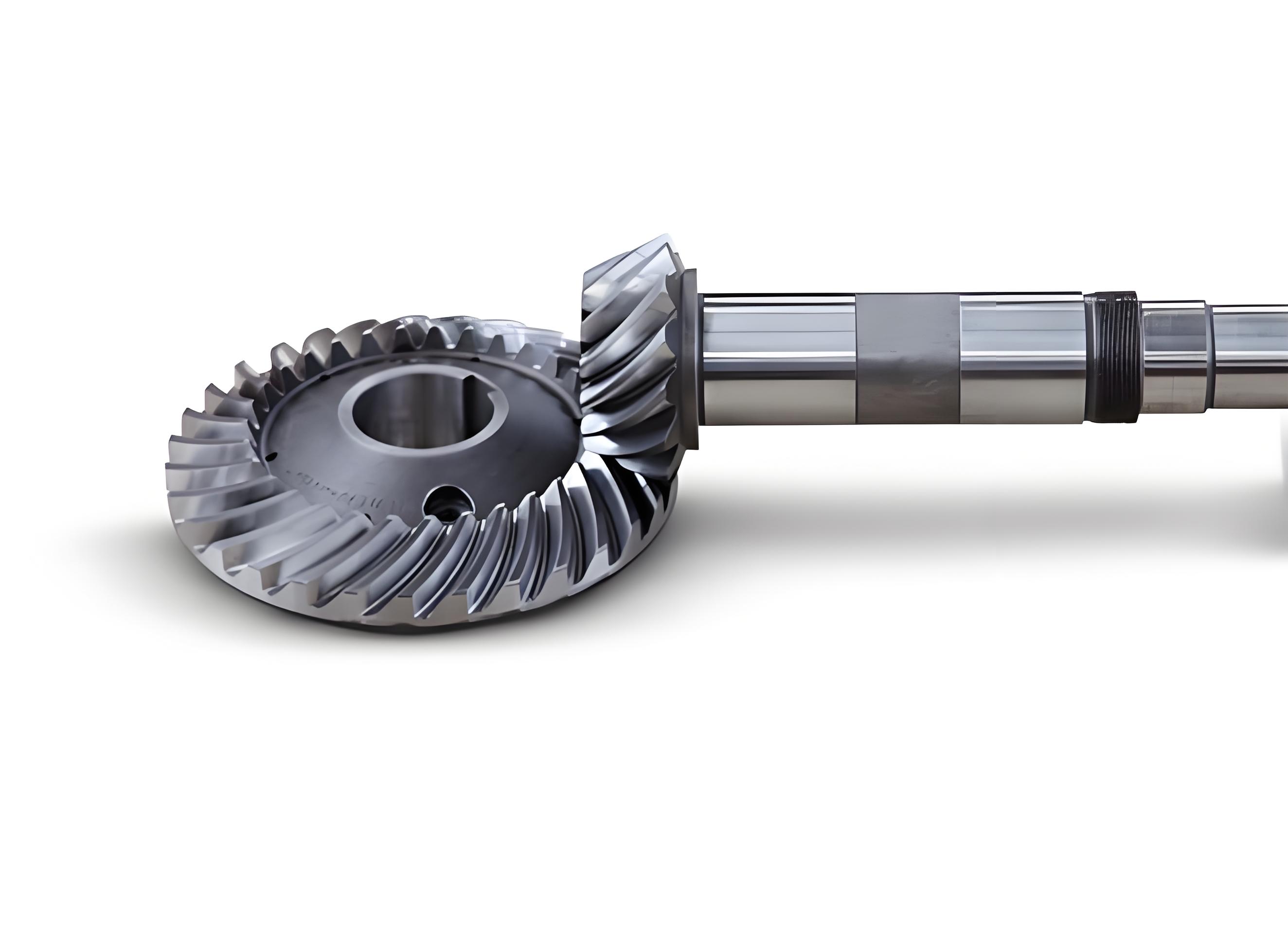
Abstract
Spiral bevel gear is critical components in heavy machinery, playing a vital role in power transmission. The demanding operational conditions in heavy machinery applications often lead to significant wear, which can affect performance and lifespan. This review delves into the wear mechanisms affecting spiral bevel gear and explores effective maintenance strategies to mitigate wear and enhance durability.
Introduction
Spiral bevel gear is essential in various heavy machinery applications, such as construction equipment, mining machinery, and industrial drives. Due to their operational environment, these spiral bevel gear is subjected to high loads, varying speeds, and harsh conditions, leading to various wear mechanisms. Understanding these wear mechanisms and implementing effective maintenance strategies is crucial for ensuring the reliability and longevity of spiral bevel gear systems.
Wear Mechanisms
- Abrasive Wear
- Causes: Involves hard particles or asperities that cause material removal from spiral bevel gear surface.
- Indicators: Scratches or grooves on spiral bevel gear teeth surfaces.
- Adhesive Wear
- Causes: Occurs when material transfers from one gear tooth surface to another due to high contact pressure and inadequate lubrication.
- Indicators: Scuffing or smearing of spiral bevel gear teeth surfaces.
- Fatigue Wear
- Causes: Resulting from repeated loading and unloading cycles, leading to crack initiation and propagation.
- Indicators: Pitting or spalling on spiral bevel gear teeth surfaces.
- Corrosive Wear
- Causes: Exposure to corrosive environments leading to chemical reactions on spiral bevel gear surfaces.
- Indicators: Rust or chemical pitting on spiral bevel gear teeth surfaces.
- Surface Wear
- Causes: Micro-level wear due to surface roughness and microstructural imperfections.
- Indicators: Microscopic wear patterns, often detectable through high-resolution imaging.
Maintenance Strategies
- Lubrication Management
- Selection of Lubricants: Choosing appropriate lubricants that can withstand the operational conditions and reduce friction and wear.
- Lubricant Monitoring: Regular analysis of lubricant condition to ensure its effectiveness and detect contamination.
- Condition Monitoring
- Vibration Analysis: Monitoring the vibration signatures of spiral bevel gear systems to detect early signs of wear and misalignment.
- Acoustic Emission Analysis: Using high-frequency sound waves to identify wear and damage in spiral bevel gear teeth.
- Thermography: Employing infrared imaging to monitor temperature variations indicating wear or lubrication issues.
- Predictive Maintenance
- Digital Twins: Implementing digital twin technology for real-time simulation and predictive maintenance scheduling.
- AI and Machine Learning: Utilizing advanced algorithms to predict wear patterns and maintenance needs based on operational data.
- Surface Treatment and Coatings
- Surface Hardening: Applying treatments such as carburizing, nitriding, or induction hardening to enhance surface hardness and wear resistance.
- Protective Coatings: Using advanced coatings like diamond-like carbon (DLC) or titanium nitride (TiN) to reduce friction and protect against corrosive wear.
- Gear Design Optimization
- Material Selection: Choosing materials with superior wear resistance and mechanical properties.
- Tooth Profile Modification: Optimizing spiral bevel gear tooth profiles to distribute load more evenly and reduce stress concentrations.
- Regular Inspections and Overhauls
- Scheduled Inspections: Conducting periodic inspections to identify wear and damage early.
- Preventive Overhauls: Performing preventive maintenance and overhauls based on wear analysis and condition monitoring data.
Conclusion
Effective wear analysis and maintenance strategies are vital for the reliable operation of spiral bevel gear in heavy machinery. By understanding the various wear mechanisms and implementing advanced maintenance techniques, industries can enhance spiral bevel gear performance, extend their lifespan, and reduce downtime. Continued research and development in this field are essential for keeping pace with the evolving demands of heavy machinery applications.
References
- Wear Journal: Articles on wear mechanisms and mitigation techniques for heavy machinery components.
- Tribology International: Research on advanced lubrication and surface treatment technologies.
- Journal of Mechanical Engineering: Studies on condition monitoring and predictive maintenance strategies for spiral bevel gear systems.
- Materials and Design: Papers on material selection and spiral bevel gear design optimization for improved wear resistance.
This review serves as a comprehensive guide for engineers and maintenance professionals in understanding and addressing the wear challenges associated with spiral bevel gear in heavy machinery.