Performance Analysis of Gears Produced by Two Processes
The gear produced by a typical gear machining process is shown in Figure 1.Due to the fact that the fiber structure of the part is cut off during the toothed processing (gear hobbing, gear insertion, honing, gear grinding, etc.), although high tooth profile accuracy, tooth phase accuracy and surface finish can be obtained, the force and fracture resistance of the gear are affected. Under the overload condition, there is a potential risk of tooth root fracture.
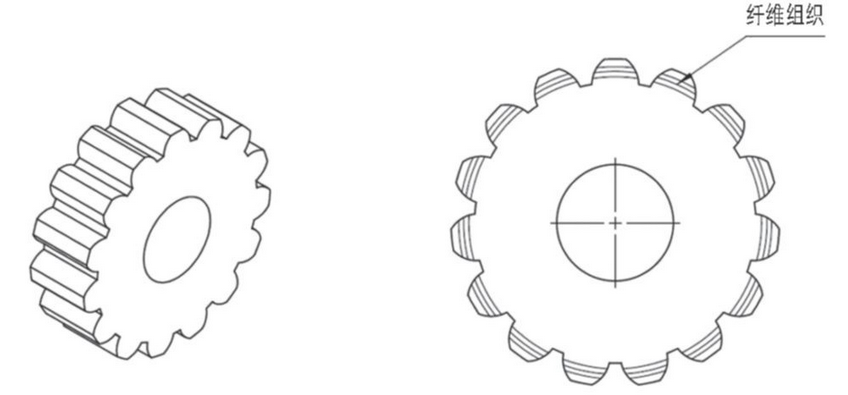
Under the condition of precision forging process, the gear produced is shown in Figure 2.During precision forging, metal under high stress produces plastic deformation, compact structure of gear, continuous metal fiber, much higher fatigue strength and wear resistance than gear machined by cutting, which is suitable for working under frequent impact and heavy load conditions. However, due to its low precision, rough surface, large working noise, low working speed, tooth fatigue damage is easy to occur.
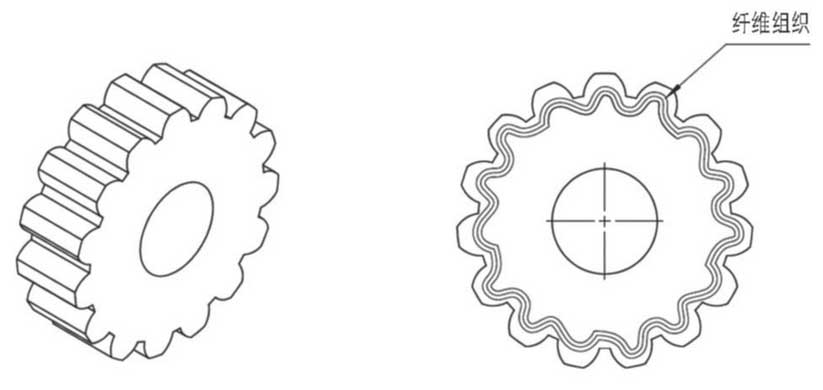
Process Innovation in Gear Processing
With the popularization of CNC machining technology and the mature application of CNC gear hobbing machine and secondary automatic tool alignment technology, we can organically combine the two gear machining processes of CNC machining and precision forging, which can not only obtain good metal fiber structure, improve stress conditions, but also obtain relatively high gear accuracy, reduce metal cutting quantity and improve production efficiency.
In actual production process, gear blank is produced by precision forging, and then precision gear hobbing is carried out by using CNC gear hobbing machine and secondary tool setting device.Gears manufactured in this way have been improved in accuracy, performance and economic value.
Compared with the typical gear machining process, the machining efficiency is improved because the amount of cutting is reduced.ZHY Gear serves a customer who manufactures a batch of new energy automotive gears with a modulus of 3mm, 24 teeth and a precision of 6 to 7 levels.
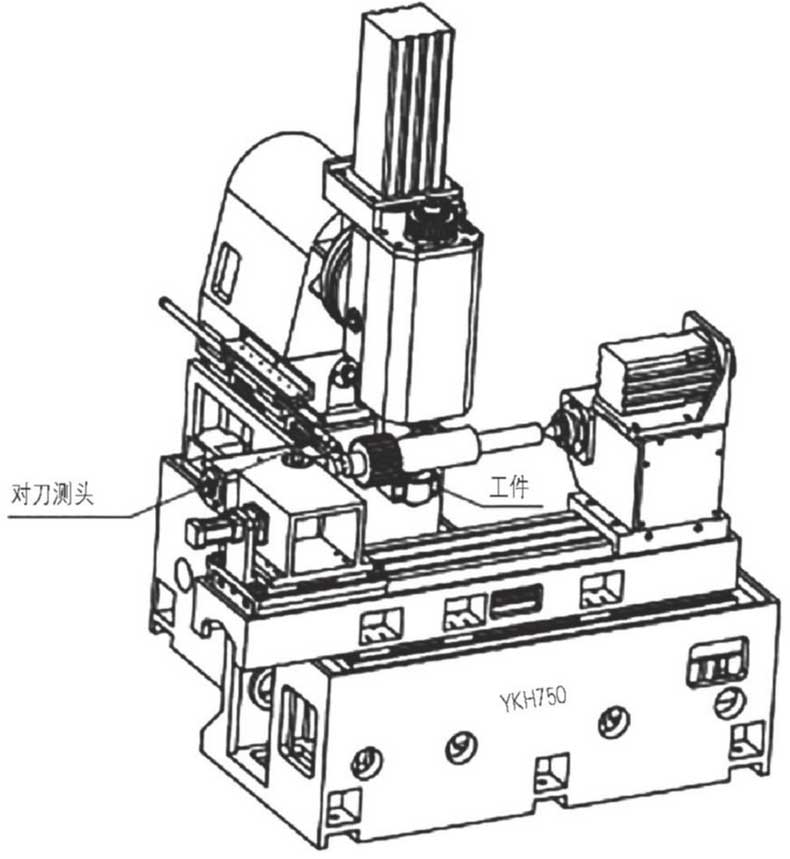
The precision forged gear blank is made for the first time, and then the precision forged gear blank is processed by using secondary tool machining process (only about 6s) on high-speed CNC spline milling machine YKH750. The machining allowance of 0.2mm is hobbed on CNC hobbing machine, only about 1min.
The new process not only improves the production efficiency, but also the performance of gears. In the user’s testing, the force performance of gears manufactured by the new process is significantly higher than that of gears manufactured by traditional methods.
Through a lot of actual production certification and test verification, the combination of precision forging process and typical gear machining process can not only improve product performance, but also improve production efficiency. It is feasible and an innovative process for gear machining.