In order to test the vibration reduction effect of two-stage high-speed helical gear transmission after modification, and to compare the vibration reduction effect of single-stage high-speed helical gear transmission and two-stage high-speed helical gear transmission, the time-varying meshing stiffness curve before and after the repair and the meshing impact curve before and after the repair are calculated by using the load transfer error curve obtained by simulation The dynamic differential equations of two-stage helical gear transmission are input and compared after solving. Fig. 1, Fig. 2 and Fig. 3 show the vibration time domain response of two tooth pairs at input speeds of 6000rpm, 12000rpm and 15000rpm only after modification of input tooth surface. Fig. 4, FIG. 5 and Fig. 6 show the vibration time domain response of two tooth pairs at input speeds of 6000rpm, 12000rpm and 15000rpm only after tooth surface modification at the output end.
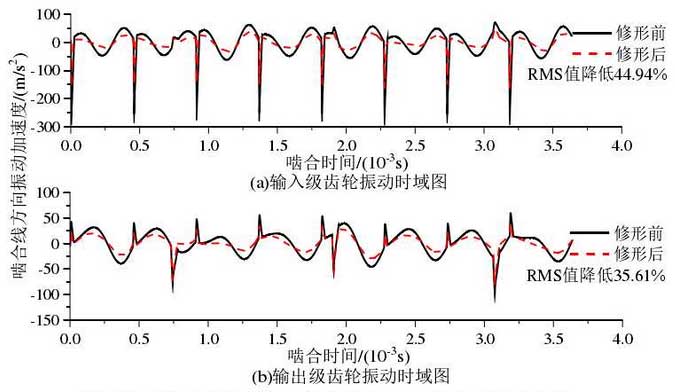
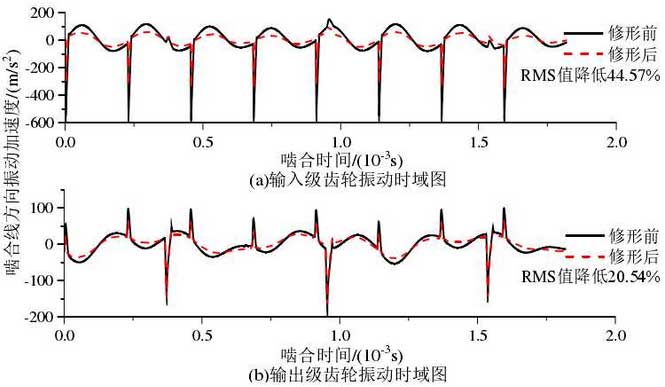
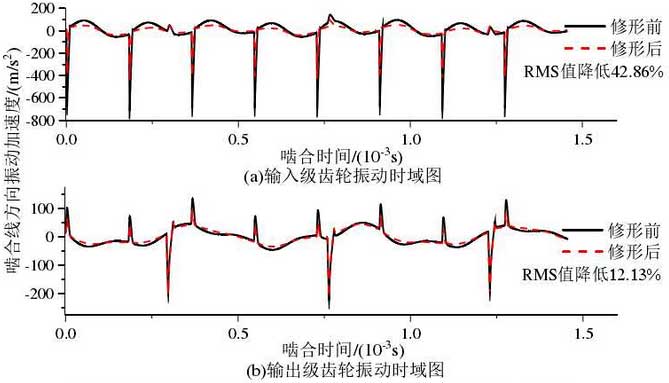
From Fig. 1 to Fig. 3 (a), it can be seen that the relative vibration acceleration fluctuation of the input end teeth pair in the time domain response of the input end teeth pair is reduced, and the vibration acceleration sudden variable caused by the engagement impact force of the input end teeth is also greatly reduced. In the time domain response of the output teeth to the time-domain response of the output teeth to the impact force, the relative vibration acceleration fluctuation of the output end teeth is also slightly reduced, and the vibration acceleration sudden variable caused by the engagement impact force of the input end teeth is also reduced to a certain extent, but the acceleration sudden change caused by the engagement impact force itself is not very obvious.
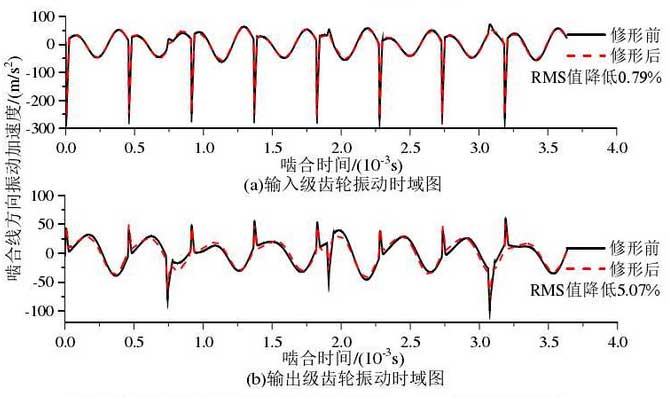
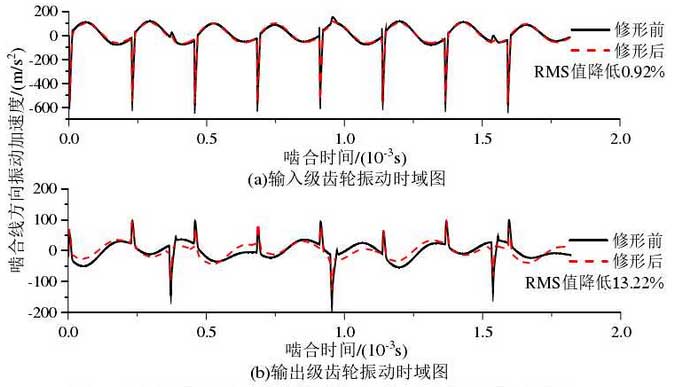
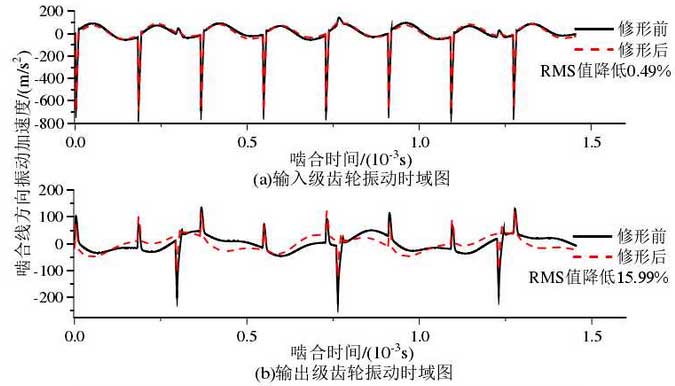
In Fig. 4-6, the gear vibration does not change significantly in the time domain response of the input end teeth only after the modification of the output tooth pair; in the time domain response of the output end tooth pair, the relative vibration acceleration fluctuation and acceleration mutation caused by self engagement impact are reduced.
The phenomena in Fig. 1 to Fig. 6 are consistent with the results of the previous analysis that “the vibration responses of the input end teeth pair and the output end tooth pair influence each other, and the influence of the former on the latter is significantly higher than that of the latter on the former”.
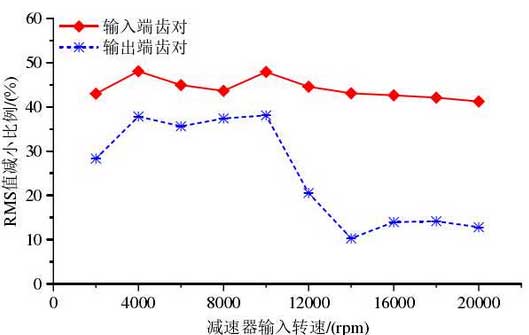
In order to compare the vibration reduction effect of two kinds of gear surface modification systems, which are only modified by the input tooth pair and the output tooth pair at various speeds, the dynamic differential equations are solved and compared with Figures 7 and 8.
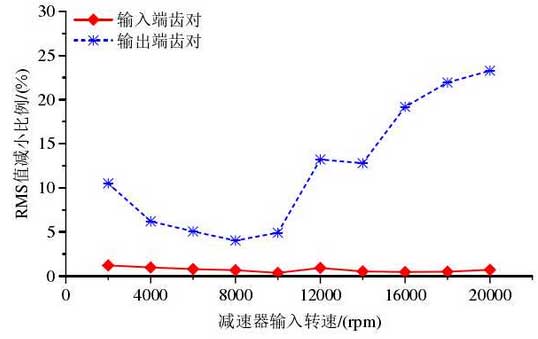
It can be seen from the data in Fig. 7 that only when the input tooth pair is modified, the vibration of the input tooth pair is better, and the vibration of the output tooth pair is also significantly reduced. In Fig. 8, the vibration of the output gear is significantly reduced at each speed when the output gear pair is modified, but the vibration of the input gear is not significantly changed. According to the analysis of the system dynamic characteristics in the previous paper, the phenomenon in Fig. 7 and Fig. 8 is that the vibration of the input end tooth pair has a great influence on the output end tooth pair, so the input end tooth pair and the output end tooth pair have obvious vibration reduction effect after the input end tooth pair is shaped. However, the vibration of the output tooth pair has little influence on the input end tooth pair, so the output end tooth pair modification only has vibration reduction effect on itself. Therefore, in the modification design of two-stage and multi-stage gear systems, the input tooth pairs should be paid more attention to.