1. Part manufacturability analysis and forming process design
Figure 1 shows the forging of straight bevel gear, which is made of 20CrMnTi cold drawn round steel. The warm forging process of gear is as follows: blanking (see Fig. 2a) → annealing → phosphating saponification treatment → pre upsetting forming (see Fig. 2b) → re lubrication treatment → heating → closed extrusion forming (see Fig. 2C) → surface cleaning → cold finishing.
(1) Blank lubrication: heat the blank to 150 ℃ ~ 200 ℃, put it into water-soluble graphite solution, and then take it out immediately and dry it quickly. In this way, the billet can prevent oxidation when heated before warm extrusion, and play a lubricating role in the process of warm extrusion.
(2) The billet is heated to 850 ℃ by medium frequency induction heating. This heating method has the advantages of fast heating speed, no oxygen peeling and good working conditions in the workshop.
(3) Mold lubrication spray soluble graphite solution onto the mold.
2. Mold structure design
Fig. 3 is the structure of warm forging die for straight bevel gear used on 8000kN press. The working part of the die is mainly composed of straight bevel gear tooth die 2, female die core 3, upper punch 19 and lower punch 15.
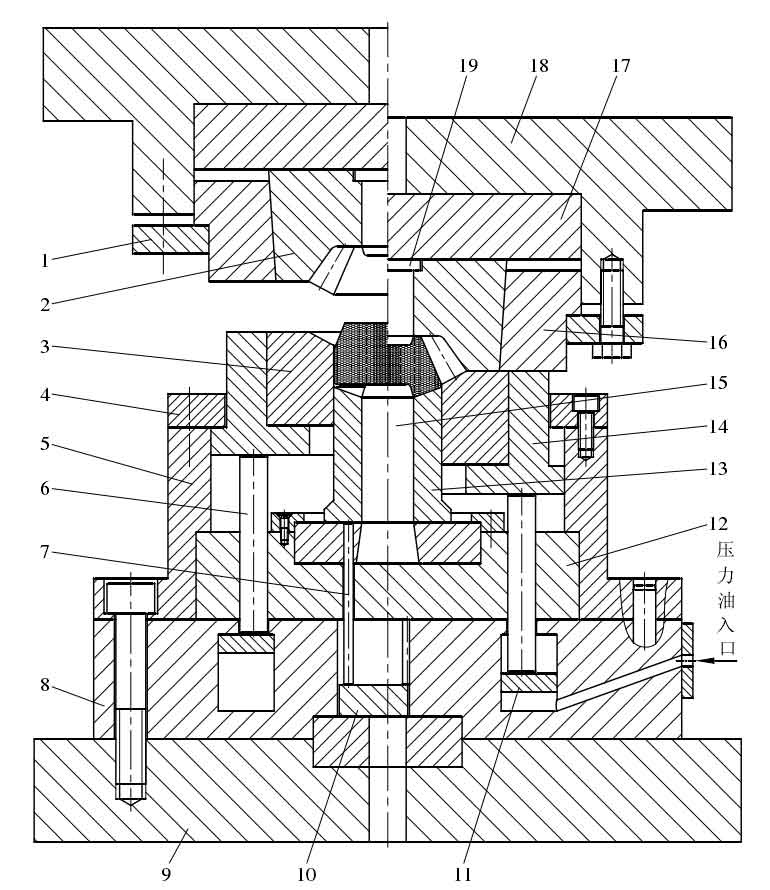
Install the straight bevel gear die 2 on the upper die, which is conducive to the tooth forming of the forging. At the same time, it can ensure that the contact time between the straight bevel gear die and the forging is short, and the temperature rise of the straight bevel gear die will not be too high, so as to avoid premature failure caused by annealing and thermal fatigue of the straight bevel gear die; The die adopts the floating die structure. Compared with the fixed die structure used in the traditional closed non flash die forging, the straight bevel gear forging has small deformation resistance and good filling performance. The die adopts the floating die structure. An oil cylinder is set under the lower die 14. The oil cylinder is filled with oil with a certain pressure with the hydraulic system shown in Fig. 4. The floating of the lower die 14 and the die core 3 is realized by the amount of oil in the oil cylinder. In order to reduce the problem of poor die rigidity caused by hollowing out of the lower die base, the support plate 10 should be designed as shown in Figure 5.
3. Working process of mould
Before the upper and lower dies are closed, the oil cylinder is filled with oil with a certain pressure, and the floating piston 11 is in the upper limit position. Under the support of the pressure bearing rod 6, the lower die 14 and the die core 3 are also in the upper limit position, forming a cavity together with the lower punch 15 and the ejector rod 13; Put the heated pre upsetting blank into the cavity. With the sliding block of the press descending, the straight bevel gear tooth die 2 first contacts the die core 3 and the lower die 14 to form a closed cavity; The upper die continues to go down with the slider to make the upper and lower punch extrude the blank at the same time; During the downward movement of the lower die 14, the floating piston 11 is pushed by the pressure bearing rod 6 to extrude the oil from the oil cylinder; At this time, due to the function of the overflow valve, the stable and high oil pressure is maintained in the oil cylinder to ensure that the upper and lower concave dies are always closed tightly, so as to ensure that the straight bevel gear forging does not have flash, and improve the filling of the corner of the die cavity at the same time; After the extrusion is completed, the slider of the press goes up, and the lower concave die 14 is reset upward by the pressure of the gas top oil, and the punch is disengaged from the forging at the same time; Take out the straight bevel gear forging to complete a cycle.