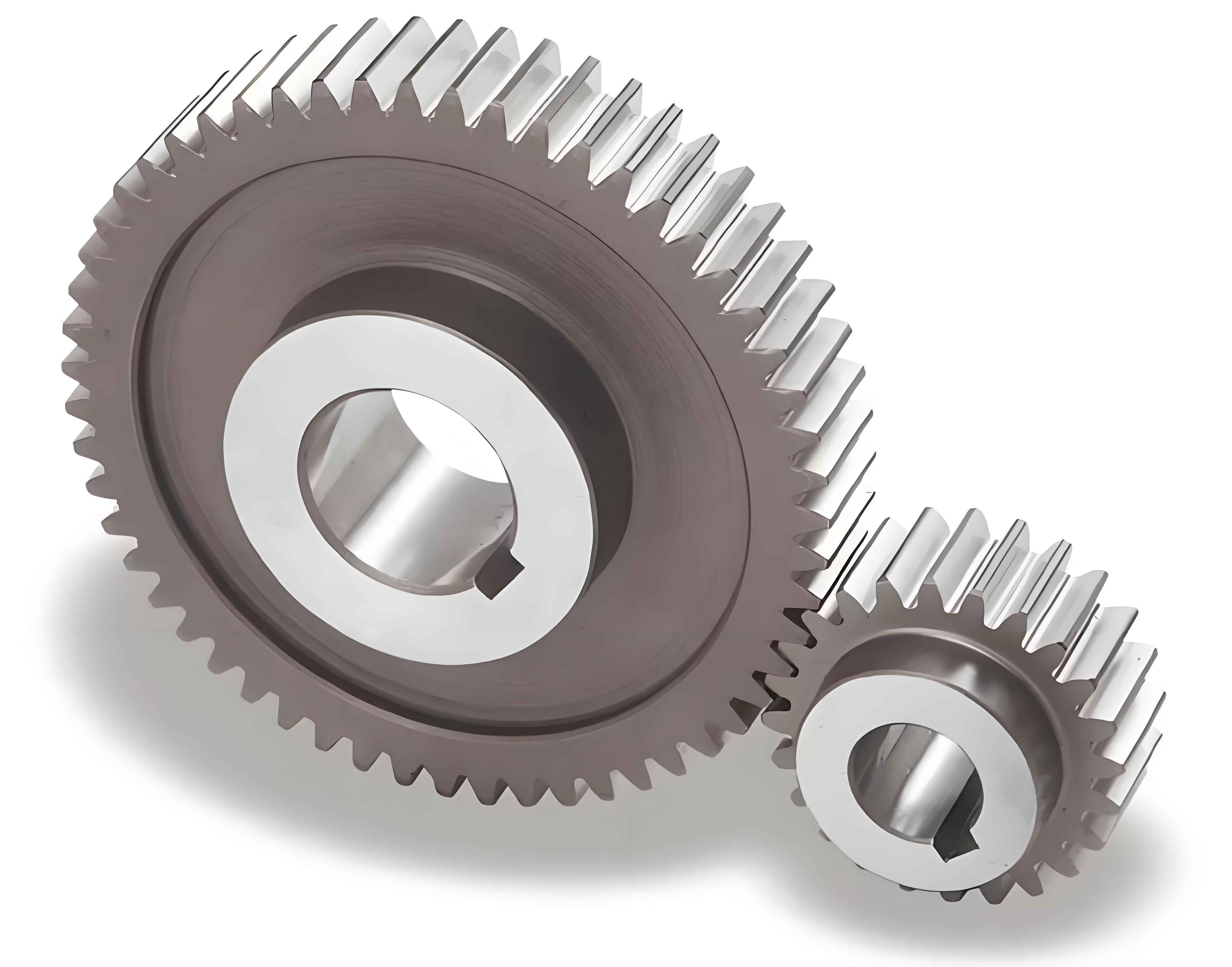
Introduction
Spur gear is fundamental components in many mechanical systems, known for their simplicity and efficiency in transmitting motion and power. However, like all mechanical parts, they are subject to wear and tear over time. Predictive maintenance and condition monitoring are essential strategies for managing the health and longevity of spur gear. This article explores the wear mechanisms affecting spur gear, the importance of predictive maintenance, and the various condition monitoring techniques used to detect and prevent gear failures.
Wear Mechanisms in Spur Gear
Wear in spur gear can be attributed to several mechanisms, each influencing the gear’s performance and lifespan differently.
Adhesive Wear
Adhesive wear occurs when gear teeth come into direct contact under high load, leading to material transfer between the surfaces.
Characteristics
- Material transfer between contact surfaces
- Increased surface roughness
Contributing Factors
- High contact pressures
- Inadequate lubrication
- Poor surface finish
Abrasive Wear
Abrasive wear is caused by hard particles or asperities on one surface that abrade the opposing surface.
Characteristics
- Surface scratches and grooves
- Progressive material loss
Contributing Factors
- Contaminants in the lubricant
- Presence of hard particles
- Inadequate filtration
Fatigue Wear
Fatigue wear results from repeated cyclic loading, leading to crack initiation and propagation.
Characteristics
- Cracks at the tooth root
- Progressive crack growth leading to tooth breakage
Contributing Factors
- Cyclic loading
- Stress concentrations
- Material defects
Corrosive Wear
Corrosive wear involves the chemical or electrochemical reaction between spur gear material and its environment.
Characteristics
- Pitting and surface roughening
- Material degradation due to chemical reactions
Contributing Factors
- Exposure to corrosive environments
- Inadequate protective coatings
- High humidity and temperature
Table 1: Overview of Wear Mechanisms
Wear Mechanism | Characteristics | Contributing Factors |
---|---|---|
Adhesive Wear | Material transfer, surface roughness | High contact pressures, inadequate lubrication |
Abrasive Wear | Surface scratches, material loss | Contaminants, hard particles, inadequate filtration |
Fatigue Wear | Cracks, progressive crack growth | Cyclic loading, stress concentrations |
Corrosive Wear | Pitting, material degradation | Corrosive environments, high humidity |
Importance of Predictive Maintenance
Predictive maintenance involves monitoring the condition of machinery to predict failures before they occur. This approach offers several advantages over traditional reactive maintenance.
Benefits of Predictive Maintenance
- Reduced Downtime: Early detection of issues prevents unexpected failures and minimizes downtime.
- Cost Savings: Preventing catastrophic failures reduces repair costs and extends gear life.
- Improved Reliability: Continuous monitoring ensures consistent performance and reliability of spur gear system.
- Enhanced Safety: Early identification of potential failures reduces the risk of accidents.
Key Components of Predictive Maintenance
- Condition Monitoring: Continuous or periodic measurement of spur gear health parameters.
- Data Analysis: Interpreting monitoring data to identify patterns and predict failures.
- Maintenance Scheduling: Planning maintenance activities based on predictive insights.
Condition Monitoring Techniques
Several condition monitoring techniques are employed to assess the health of spur gear and predict potential failures.
Vibration Analysis
Vibration analysis involves measuring the vibration signals generated by gear operation. Changes in vibration patterns can indicate wear, misalignment, or damage.
Process
- Data Collection: Sensors measure vibration signals.
- Signal Processing: Analyzing frequency, amplitude, and phase of vibrations.
- Diagnosis: Identifying abnormal patterns indicating wear or damage.
Oil Analysis
Oil analysis examines the lubricant for contaminants and wear particles, providing insights into the gear’s condition.
Process
- Sampling: Regular collection of oil samples from the gearbox.
- Analysis: Testing for wear particles, viscosity, and contamination.
- Interpretation: Identifying wear trends and potential issues.
Acoustic Emission
Acoustic emission monitoring detects high-frequency sound waves generated by crack formation or material deformation.
Process
- Data Collection: Sensors capture acoustic signals.
- Signal Processing: Analyzing sound wave characteristics.
- Diagnosis: Detecting crack initiation and propagation.
Thermography
Thermography uses infrared imaging to measure the temperature distribution across gear surfaces, identifying hot spots that indicate excessive friction or wear.
Process
- Imaging: Capturing infrared images of spur gear.
- Analysis: Identifying temperature anomalies.
- Interpretation: Diagnosing areas of high friction and wear.
Table 2: Comparison of Condition Monitoring Techniques
Technique | Key Parameters Measured | Advantages | Limitations |
---|---|---|---|
Vibration Analysis | Vibration frequency, amplitude | Early detection, detailed analysis | Requires expertise for interpretation |
Oil Analysis | Wear particles, viscosity, contamination | Direct indication of wear, cost-effective | Requires regular sampling |
Acoustic Emission | High-frequency sound waves | Sensitive to crack formation, real-time monitoring | Requires sensitive equipment |
Thermography | Temperature distribution | Visual detection of hot spots, non-invasive | Limited to surface temperature |
Implementing Predictive Maintenance
Step-by-Step Implementation
- Assessment: Evaluate the current maintenance practices and identify key areas for improvement.
- Selection of Techniques: Choose appropriate condition monitoring techniques based on spur gear system requirements.
- Installation: Set up sensors and monitoring equipment.
- Data Collection: Establish a schedule for regular data collection.
- Data Analysis: Use software tools and expert analysis to interpret the data.
- Maintenance Planning: Schedule maintenance activities based on predictive insights.
- Review and Optimization: Continuously review the effectiveness of the predictive maintenance program and make necessary adjustments.
Case Study: Predictive Maintenance in a Manufacturing Plant
Initial Situation
A manufacturing plant experienced frequent gear failures, leading to high downtime and repair costs. The plant decided to implement a predictive maintenance program focusing on vibration analysis and oil analysis.
Implementation Process
- Assessment: Identified key gearboxes and critical points for monitoring.
- Selection of Techniques: Chose vibration analysis and oil analysis for their effectiveness and cost-efficiency.
- Installation: Installed vibration sensors on critical gearboxes and established an oil sampling schedule.
- Data Collection: Collected vibration data continuously and oil samples monthly.
- Data Analysis: Used specialized software to analyze vibration patterns and laboratory analysis for oil samples.
- Maintenance Planning: Scheduled maintenance based on the analysis, addressing issues before failures occurred.
Results
- Reduced Downtime: Gear failures decreased by 40%.
- Cost Savings: Maintenance costs reduced by 25%.
- Improved Reliability: Gearbox reliability improved significantly.
- Enhanced Safety: Reduced risk of sudden failures and associated hazards.
Table 3: Comparison of Initial and Post-Implementation Performance
Parameter | Initial State | Post-Implementation |
---|---|---|
Gear Failures | Frequent | Reduced by 40% |
Maintenance Costs | High | Reduced by 25% |
Gearbox Reliability | Moderate | Improved significantly |
Safety Risks | High | Reduced |
Future Trends in Predictive Maintenance
Integration of IoT and AI
The integration of the Internet of Things (IoT) and Artificial Intelligence (AI) in predictive maintenance offers advanced capabilities for real-time monitoring and automated data analysis.
Benefits
- Real-Time Monitoring: Continuous data collection and instant alerts.
- Automated Analysis: AI algorithms analyze data and predict failures.
- Enhanced Decision Making: Data-driven insights for proactive maintenance planning.
Advanced Sensor Technologies
Development of advanced sensor technologies, such as wireless and nano-sensors, provides more accurate and comprehensive monitoring capabilities.
Benefits
- Wireless Sensors: Easy installation and maintenance.
- Nano-Sensors: High sensitivity to detect early signs of wear and tear.
Table 4: Future Trends in Predictive Maintenance
Trend | Description | Potential Benefits |
---|---|---|
IoT and AI Integration | Real-time monitoring and automated analysis | Proactive maintenance, reduced downtime |
Advanced Sensor Technologies | Development of wireless and nano-sensors | Enhanced accuracy, early detection |
Conclusion
Wear and tear in spur gear is an inevitable challenge that can be effectively managed through predictive maintenance and condition monitoring techniques. By understanding the wear mechanisms and implementing advanced monitoring methods, industries can significantly enhance the reliability, efficiency, and lifespan of their gear systems. Future advancements in IoT, AI, and sensor technologies promise to further revolutionize predictive maintenance, offering even greater benefits in terms of performance and cost savings.