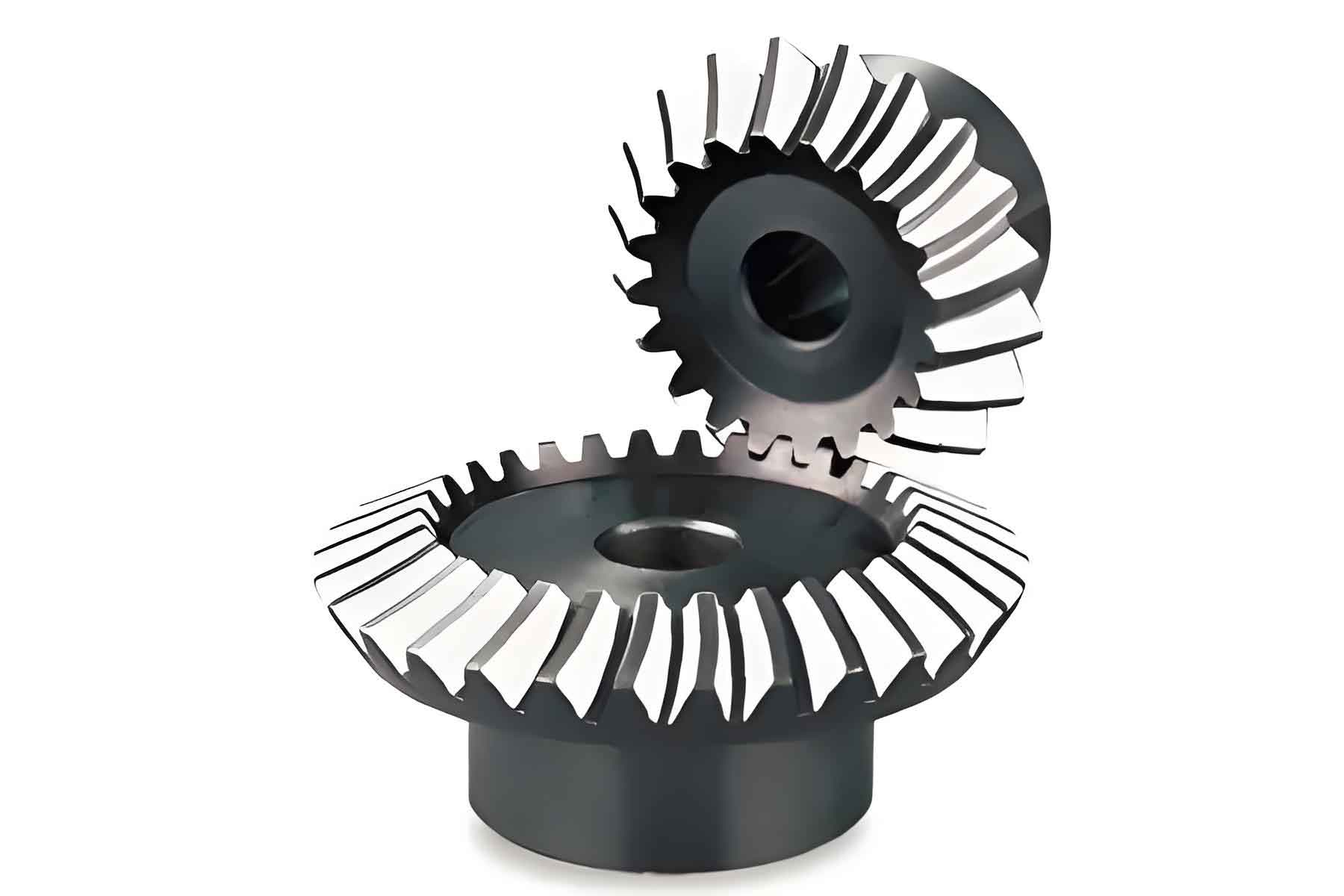
Introduction
Industrial bevel gear is critical components in many mechanical systems, playing a vital role in power transmission. However, the demanding operational environments these gear operate in can lead to significant wear and tear, which, if not detected and managed effectively, can result in system failures and costly downtime. This article explores various wear detection techniques and maintenance strategies for industrial bevel gear, providing insights into best practices for ensuring their longevity and reliability.
Importance of Wear Detection and Maintenance
Effective wear detection and maintenance of bevel gear is essential for several reasons:
- Preventing Unexpected Failures:
- Early detection of wear can prevent sudden bevel gear failures that could disrupt production processes and lead to expensive repairs.
- Extending Gear Lifespan:
- Proper maintenance strategies can significantly extend the operational life of bevel gear, reducing the need for frequent replacements.
- Optimizing Performance:
- Maintaining bevel gear in optimal condition ensures efficient power transmission and overall system performance.
- Cost Savings:
- Proactive maintenance and timely repairs can reduce the overall cost of ownership by minimizing downtime and avoiding catastrophic failures.
Wear Detection Techniques
Various techniques are employed to detect wear in industrial bevel gear. These techniques can be categorized into visual, non-destructive, and analytical methods.
1. Visual Inspection
- Routine Inspections:
- Regular visual inspections of bevel gear can identify obvious signs of wear, such as pitting, scoring, and surface discoloration.
- Endoscopic Inspection:
- Using endoscopic tools to inspect hard-to-reach areas within gearboxes and housings.
Table 1: Visual Inspection Indicators
Indicator | Description | Potential Causes |
---|---|---|
Pitting | Small, shallow depressions on gear teeth | Fatigue, inadequate lubrication |
Scoring | Deep scratches or grooves on gear surfaces | Contaminants, misalignment |
Discoloration | Changes in color (e.g., blue or brown) | Overheating, poor lubrication |
2. Non-Destructive Testing (NDT)
- Ultrasonic Testing:
- Uses high-frequency sound waves to detect internal flaws and cracks in bevel gear materials.
- Magnetic Particle Inspection (MPI):
- Detects surface and near-surface defects using magnetic fields and iron particles.
- Dye Penetrant Inspection (DPI):
- Highlights surface-breaking defects by applying a visible or fluorescent dye.
Table 2: Non-Destructive Testing Methods
Method | Principle | Applications |
---|---|---|
Ultrasonic Testing | Sound waves reflect from internal defects | Detecting internal cracks |
Magnetic Particle Inspection | Magnetic fields reveal surface defects | Identifying surface and near-surface flaws |
Dye Penetrant Inspection | Dye highlights surface cracks | Detecting surface-breaking defects |
3. Analytical Techniques
- Vibration Analysis:
- Monitors vibration patterns to identify abnormal bevel gear behavior indicative of wear or misalignment.
- Oil Analysis:
- Examines lubricating oil for metal particles and contaminants that signal wear and tear.
- Acoustic Emission:
- Uses sensors to detect high-frequency sound waves emitted by cracks and defects.
Table 3: Analytical Wear Detection Techniques
Technique | Principle | Benefits |
---|---|---|
Vibration Analysis | Analyzes vibration frequencies | Early detection of wear and misalignment |
Oil Analysis | Analyzes lubricant for contaminants | Identifies wear particles and degradation |
Acoustic Emission | Detects sound waves from defects | Sensitive to early-stage damage |
Maintenance Strategies
Implementing effective maintenance strategies is crucial for managing wear and ensuring the longevity of bevel gear. Key strategies include preventive, predictive, and corrective maintenance.
1. Preventive Maintenance
- Scheduled Inspections:
- Conduct regular inspections and maintenance activities based on a predetermined schedule.
- Lubrication Management:
- Ensure proper lubrication to minimize friction and wear. Use high-quality lubricants and follow manufacturer recommendations for lubrication intervals.
- Alignment Checks:
- Regularly check and adjust gear alignment to prevent excessive wear and misalignment issues.
List of Preventive Maintenance Activities:
- Scheduled visual inspections
- Regular lubrication checks and replenishment
- Alignment verification and adjustment
- Cleaning and debris removal
2. Predictive Maintenance
- Condition Monitoring:
- Use real-time monitoring systems to track bevel gear conditions and predict potential failures based on collected data.
- Trend Analysis:
- Analyze trends in vibration, temperature, and oil quality data to anticipate wear and schedule maintenance proactively.
List of Predictive Maintenance Tools:
- Vibration sensors
- Temperature sensors
- Oil quality analyzers
- Acoustic emission sensors
3. Corrective Maintenance
- Timely Repairs:
- Perform repairs and replacements as soon as wear or damage is detected to prevent further deterioration.
- Root Cause Analysis:
- Investigate and address the root causes of wear to prevent recurrence and improve overall system reliability.
- Component Replacement:
- Replace worn or damaged bevel gear and components with high-quality replacements to restore system functionality.
List of Corrective Maintenance Actions:
- Immediate repair of identified wear or damage
- Replacement of worn or defective bevel gear
- Root cause analysis to identify underlying issues
- Implementation of design or operational improvements
Case Study: Wear Detection and Maintenance in a Manufacturing Plant
Background
A manufacturing plant experienced frequent downtime due to bevel gear failures in their conveyor systems. The plant implemented a comprehensive wear detection and maintenance program to address these issues.
Implementation
- Visual and NDT Inspections:
- Regular visual inspections and periodic ultrasonic testing were conducted to identify early signs of wear and internal defects.
- Predictive Maintenance:
- Vibration analysis and oil analysis were used to monitor gear conditions continuously and predict potential failures.
- Corrective Actions:
- Worn gears were promptly replaced, and root cause analysis was performed to identify and address underlying issues, such as lubrication deficiencies and misalignment.
Results
- Reduced Downtime:
- The frequency of unexpected gear failures and associated downtime was significantly reduced.
- Extended Gear Lifespan:
- Enhanced maintenance practices extended the operational life of bevel gear, reducing the need for frequent replacements.
- Cost Savings:
- The plant achieved substantial cost savings through reduced downtime, lower repair costs, and extended gear lifespan.
Future Trends in Wear Detection and Maintenance
1. Advanced Sensor Technologies
- Smart Sensors:
- Development of smart sensors with enhanced capabilities for real-time monitoring and data analysis.
- Wireless Technology:
- Integration of wireless sensors for easier installation and data transmission in remote or hard-to-access locations.
2. Artificial Intelligence and Machine Learning
- Predictive Analytics:
- Use of AI and machine learning algorithms to analyze data from wear detection systems and predict maintenance needs with greater accuracy.
- Automated Decision-Making:
- Implementation of automated systems that can make maintenance decisions based on real-time data and predictive models.
3. Sustainable Maintenance Practices
- Eco-Friendly Lubricants:
- Development and use of environmentally friendly lubricants that provide effective wear protection while reducing environmental impact.
- Recycling and Reuse:
- Implementing recycling programs for used gear components and lubricants to promote sustainability.
Conclusion
Effective wear detection and maintenance strategies are crucial for ensuring the reliability and longevity of industrial bevel gear. By employing a combination of visual inspections, non-destructive testing, and analytical techniques, industries can identify wear at an early stage and implement appropriate maintenance actions. Adopting preventive, predictive, and corrective maintenance strategies can significantly reduce downtime, extend gear lifespan, and achieve cost savings. As technology advances, the integration of advanced sensor technologies, AI, and sustainable practices will further enhance wear detection and maintenance, ensuring the optimal performance of industrial bevel gear.