Abstract: This study focuses on the characteristics of flow field and temperature field in high-speed aeronautical bevel gear with linear velocities up to 160 m/s under oil injection lubrication. Utilizing a thermal-fluid coupling analysis model, significant findings are revealed concerning lubrication effectiveness, convective heat transfer, and windage loss, providing support for high-speed gear transmission lubrication and high-load design.
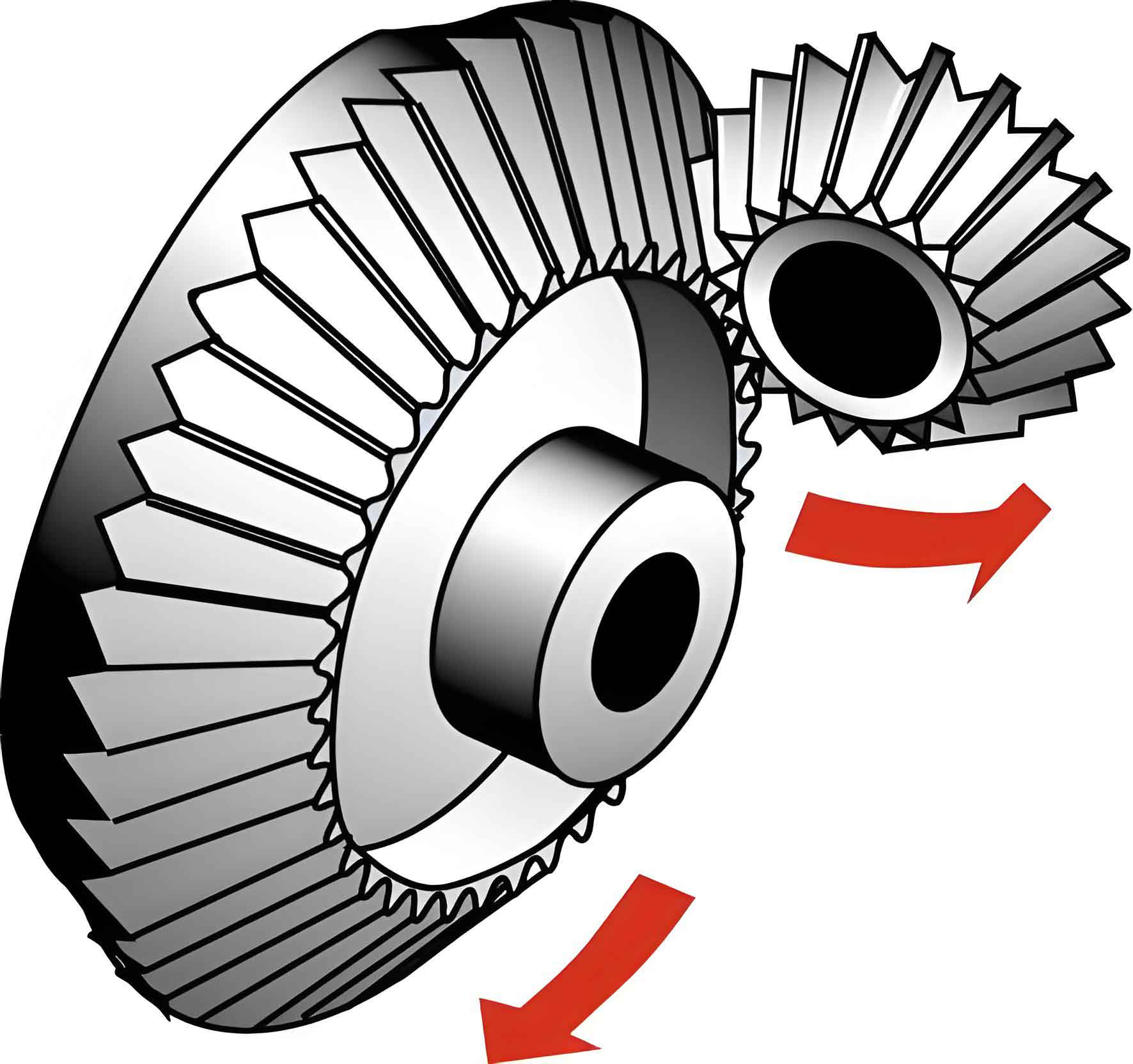
1. Introduction
Bevel gear, known for their high load-carrying capacity and transmission stability, are commonly used in mechanical transmission systems of high-end equipment such as aerospace engines and helicopters. However, under high-speed and heavy-load conditions, issues such as gear scuffing and pitting are exacerbated, posing risks to equipment service safety. Traditional gear lubrication designs often rely on empirical formulas, neglecting the impact of actual lubrication conditions like gear speed, oil spray velocity, and spray angle. This study aims to address these gaps, particularly in the context of high linear velocities.
2. Literature Review
Previous research has primarily focused on cylindrical gears with relatively low linear velocities, utilizing computational fluid dynamics (CFD) and experimental methods to analyze gear lubrication and windage loss. However, studies on bevel gear, especially at high linear velocities, are insufficient. Table 1 summarizes key findings from relevant literature.
Reference | Focus | Key Findings |
---|---|---|
Liu et al. | CFD analysis of FZG gearbox lubrication flow field | CFD results highly consistent with experimental observations |
Hildebrand et al. | Influence of guide plate on oil flow in FZG gearbox | Oil agitation and acceleration contribute to churning losses |
Wang et al. | Effect of oil injection methods on high-speed spur gear lubrication | Different injection methods impact gear lubrication |
Zhu et al. | Windage torque analysis of aeronautical bevel gear | Use of deflectors can reduce windage losses by 80% at high speeds |
3. Methodology
This study employs CFD techniques to analyze the flow field and windage power loss in high-speed bevel gear, incorporating a thermal-fluid coupling model to calculate gear temperature distribution. The bevel gear pair used in this study is from an accessory gearbox of an aerospace engine, with a rated power of 223.50 kW and a pinion speed of up to 13800.85 r/min (linear velocity of 91.70 m/s).
4. Results and Discussion
4.1 Flow Field Analysis
The distribution of oil spray columns at different linear velocities is illustrated in Table 2.
Linear Velocity (m/s) | Oil Spray Column Characteristics |
---|---|
40 | Intact spray columns, adequate oil reaching gear mesh area |
160 | Broken and offset spray columns, minimal oil retention in gear mesh area |
As linear velocity increases, the spray columns break up and shift, significantly impacting lubrication effectiveness. This is due to the air barrier created by high-speed gear rotation.
4.2 Oil Distribution and Convective Heat Transfer
The average oil volume fraction on the gear tooth surface decreases by 83.5% as linear velocity increases from 40 m/s to 160 m/s.
Convective heat transfer coefficients on the tooth and end surfaces increase with linear velocity, with the tooth surface values being 2-3 times higher than those on the end surface. However, beyond 120 m/s, oil scarcity leads to a decrease in convective heat transfer in the mesh area.
4.3 Windage Loss and Power Loss
The windage loss increases exponentially with linear velocity, becoming the primary source of power loss in the gear pair beyond 80 m/s. Figure 3 compares the windage loss calculated using the simulation model with empirical formulas and experimental data.
4.4 Temperature Field Analysis
The maximum gear temperature increases by 73% from 169.70°C at 40 m/s to 293.70°C at 160 m/s, posing a significant risk of scuffing failure. Figure 4 shows the temperature field distribution at two typical speeds.
The temperature difference between the highest and lowest points on the gear increases with linear velocity, exacerbating thermal stresses and deformations.
5. Conclusions
This study provides valuable insights into the impact of linear velocity on oil injection lubrication in high-speed aeronautical bevel gear. Key findings include:
- A significant decrease in oil volume fraction on the gear tooth surface as linear velocity increases.
- Increased convective heat transfer coefficients on both tooth and end surfaces, but a decrease in the mesh area due to oil scarcity beyond 120 m/s.
- Exponential growth in windage loss with linear velocity, becoming the primary power loss source beyond 80 m/s.
- Significant increase in gear temperatures and temperature differences, leading to increased thermal stresses and deformations.
These findings support high-speed gear transmission lubrication and high-load design, contributing to the reliability and performance of aerospace equipment.