Due to the low efficiency and precision of gear shaping, which can only cut the soft tooth surface gear, it is not conducive to the application of high-speed and heavy load of the surface gear. With the support of NASA, the military and Boeing, etc., Litvin and others proposed the method of worm hob (grinding wheel) to cut (grind) the surface gear. The principle of this processing method is shown in Figure 3. The profile of the gear shaper cutter (at this time, commonly known as the profile wheel) is needed to define the profile of the worm cutter. The cutter moves along the axis of the profile wheel (dotted line in Fig.5 in Figure 3) to make the tooth feed, which can simulate the axial (longitudinal) profile of the profile wheel. Because the normal profile of the profile wheel moves around the worm axis to form the profile of the cutter, Therefore, when the worm tool rotates around its own axis, it can simulate the rotation of the generating gear, and the workpiece rotates around its own axis. The mesh between the worm tool and the face gear is realized, which simulates the mesh between the generating gear and the face gear.
Workpiece and worm tool are point contact, which belong to double parameter envelope, but because of continuous indexing, the machining efficiency is high. Because on the one hand, it is necessary to simulate the production wheel, on the other hand, it is also necessary to simulate the meshing process between the production wheel and the face gear, even if it is hobbing, the machine tool is relatively complex. If it is gear grinding, because it is necessary to trim the tool in the process of machining, the profile of face gear, small wheel and plane profile can be used to trim the tool. Because it needs to develop into motion in the process of trimming, it is the most complex to trim the tool with plane profile, which increases the complexity of machine tool and operation again.
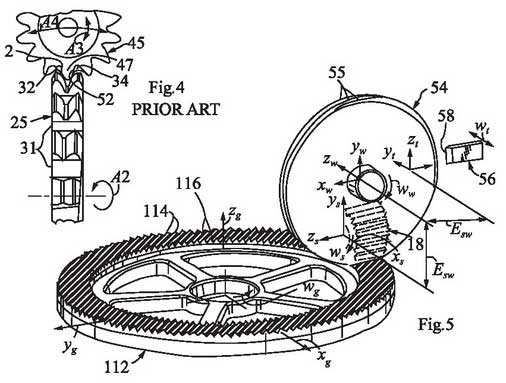
Based on this manufacturing technology, foreign scholars have done extensive and detailed research, such as the design of worm gear cutter, avoiding the singularity of cutter, tooth surface modification and stress analysis, durability test, etc., which has created a good theoretical basis for the practical application of this machining technology. China has also made great progress in the technology of worm tool machining face gear. For example, Wang Yanzhong, Zhao Ning, Zhu Rupeng, Shi Zhaoyao and others have made outstanding contributions in the design of worm tool, tooth surface development, machining experiment and detection.
In foreign countries, worm tools are mainly used for rough cutting and fine grinding of surface gears. However, this is a typical high-precision technology, involving very complex machine tools, motion and control systems, and only a few foreign enterprise groups, such as Boeing, NASA, North Star, etc., master it. For example, the second generation worm wheel face gear grinding machine developed by North Star Company has as many as 13 motion axes, including NC for generating, cutting tool dressing, error compensation and manual adjustment. It is undoubtedly very challenging to precisely control so many motions to make face gear, which also makes the manufacturing cost of face gear extremely expensive. The application of worm tools in cutting and grinding high-precision face gears has promoted the practical and important application of face gears, such as the face gear diffluence confluence transmission system on Apache helicopter. However, limited by the current level of equipment manufacturing in China, the technology of worm tool machining face gear, especially gear grinding technology, still has some difficulties in developing high-end gear grinding machine based on worm tool in a short period of time, and it is difficult to popularize it on a large scale.