When selecting the right gear type for your application, it’s important to consider the specific requirements and constraints. Let’s compare worm gears and spur gears to help you make an informed decision:
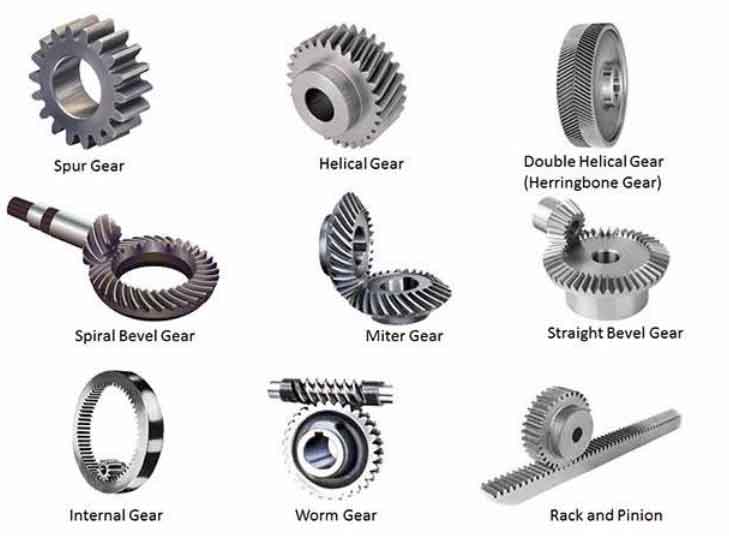
Worm Gears:
- Gear Reduction: Worm gears are known for providing high gear reduction ratios, making them suitable for applications requiring significant speed reduction.
- Self-Locking: Worm gears have a self-locking capability, meaning they resist back-driving and can hold a load in position without additional braking mechanisms.
- Compactness: Worm gears have a compact design, often requiring less axial space compared to spur gears.
- Efficiency: Worm gears generally have lower efficiency compared to spur gears due to the sliding contact between the worm and the worm wheel.
Spur Gears:
- Gear Reduction: Spur gears can provide a range of gear reduction ratios, but typically offer lower ratios compared to worm gears.
- Efficiency: Spur gears have higher efficiency compared to worm gears due to their rolling contact, resulting in less power loss.
- Noise and Vibration: Spur gears can generate more noise and vibration compared to worm gears due to the direct contact between the gear teeth.
- Backlash: Spur gears generally have less backlash compared to worm gears, which can be advantageous for applications requiring precise positioning.
When choosing between worm gears and spur gears, consider the following factors:
- Gear Reduction Ratio: If you require high gear reduction ratios, worm gears are more suitable. If lower gear reduction ratios are sufficient for your application, spur gears can be a viable option.
- Self-Locking Requirement: If your application requires a gear system that resists back-driving and can hold a load in position, worm gears offer inherent self-locking capabilities.
- Efficiency: If high efficiency is a priority and power loss needs to be minimized, spur gears are generally more efficient due to their rolling contact.
- Noise and Vibration: If noise and vibration levels need to be kept to a minimum, worm gears can provide smoother and quieter operation due to their sliding contact.
- Backlash Tolerance: If precise positioning and minimal backlash are critical, spur gears have an advantage with their lower backlash compared to worm gears.
- Space Constraints: If axial space is limited, worm gears’ compact design can be advantageous.
Consider these factors alongside other application-specific requirements such as torque, speed, load capacity, operating conditions, and environmental factors. Consulting with gear engineering experts or conducting detailed analyses can help determine the most suitable gear type for your specific application.