Gear shaping machines have witnessed significant advancements and innovations over the years, contributing to the evolution of gear production technology. Here are some key advancements and innovations in gear shaping machines:
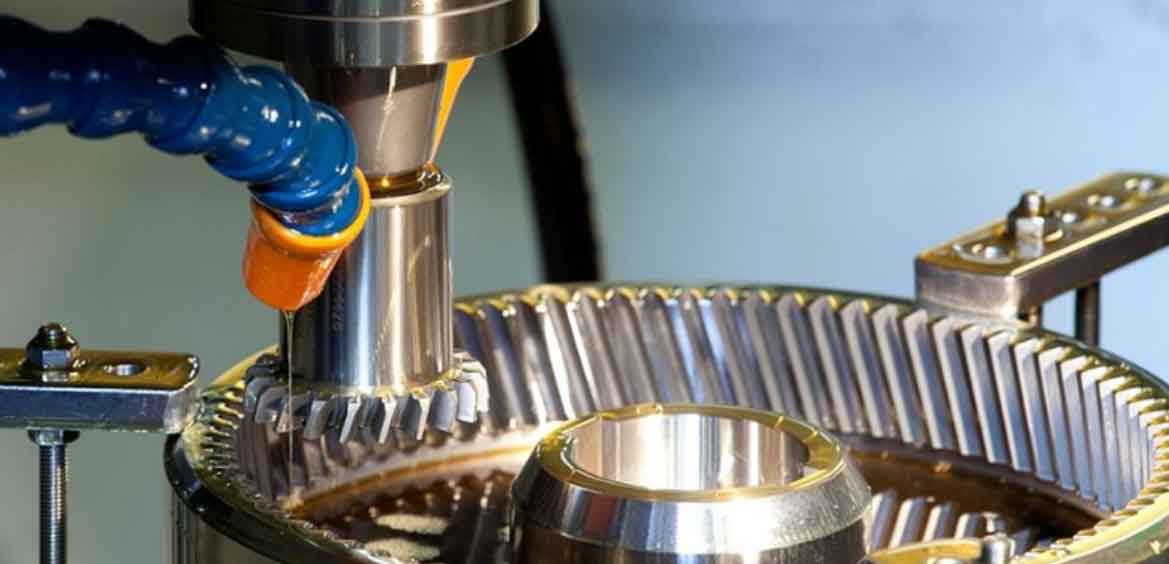
- CNC Control: Computer Numerical Control (CNC) has revolutionized gear shaping machines. Modern gear shaping machines are equipped with advanced CNC systems that offer precise control over cutting parameters, such as feed rate, stroke length, and cutting speed. CNC control enables greater automation, accuracy, and repeatability in gear shaping processes.
- Multi-Axis Capability: Many gear shaping machines now feature multi-axis capabilities, allowing for the simultaneous cutting of multiple gear teeth. This reduces cycle times and increases productivity by cutting several teeth in a single pass. Multi-axis gear shaping machines can produce complex gear geometries and facilitate the manufacturing of high-precision gears.
- Electronic Gear Indexing: Traditional gear shaping machines required mechanical indexing mechanisms to achieve the desired tooth spacing. However, advancements in electronic gear indexing have eliminated the need for complex mechanical mechanisms. Electronic indexing systems use high-precision encoders and servo motors to accurately control the gear rotation, resulting in precise tooth spacing and improved productivity.
- Improved Tooling Systems: Innovations in tooling systems have enhanced the performance and versatility of gear shaping machines. Quick-change tooling systems allow for faster setup and tool changeovers, reducing downtime between gear production runs. Advanced tool materials and coatings, such as carbide or diamond, offer extended tool life and improved cutting performance.
- High-Speed Gear Shaping: High-speed gear shaping machines have been developed to increase production rates and improve overall efficiency. These machines feature high-speed cutting spindles and enhanced control systems to achieve faster cutting speeds while maintaining accuracy and surface finish quality. High-speed gear shaping is particularly beneficial for large-scale production.
- Integrated Automation and Robotics: Gear shaping machines have become more integrated with automation and robotics systems. This integration enables automated loading and unloading of workpieces, tooling changes, and in-process inspections. Robotics can handle complex part manipulation and assist in the efficient transfer of gears between various manufacturing stages.
- Advanced Software and Simulation Tools: Gear shaping machines now come with advanced software and simulation tools for gear design, process optimization, and virtual machining. Computer-aided design (CAD) and computer-aided manufacturing (CAM) software allow for accurate gear tooth profile generation and optimization. Simulation tools help visualize and analyze the gear shaping process before actual production, minimizing errors and maximizing efficiency.
- In-Process Monitoring and Quality Control: Innovations in in-process monitoring and quality control systems have improved gear shaping machine capabilities. Real-time monitoring of cutting forces, tool wear, and dimensional accuracy enables early detection of process deviations and ensures consistent gear quality. Integrated metrology systems within gear shaping machines provide immediate feedback on gear measurements, facilitating quality control during production.
These advancements and innovations in gear shaping machines have significantly enhanced the efficiency, accuracy, and productivity of gear manufacturing. They have opened up possibilities for the production of complex gear geometries, improved surface finish quality, and enabled seamless integration into modern manufacturing processes. Gear shaping machines continue to evolve, driven by the pursuit of higher precision, increased automation, and improved manufacturing capabilities.