Helical gear is widely used in various industrial applications due to their ability to transmit power smoothly and quietly. However, even these gears can be sources of noise and vibration if not properly designed, manufactured, and maintained. Effective noise and vibration control in helical gear transmissions is crucial for ensuring the longevity and efficiency of machinery. This article explores the factors influencing noise and vibration in helical gear and presents strategies for mitigating these issues.
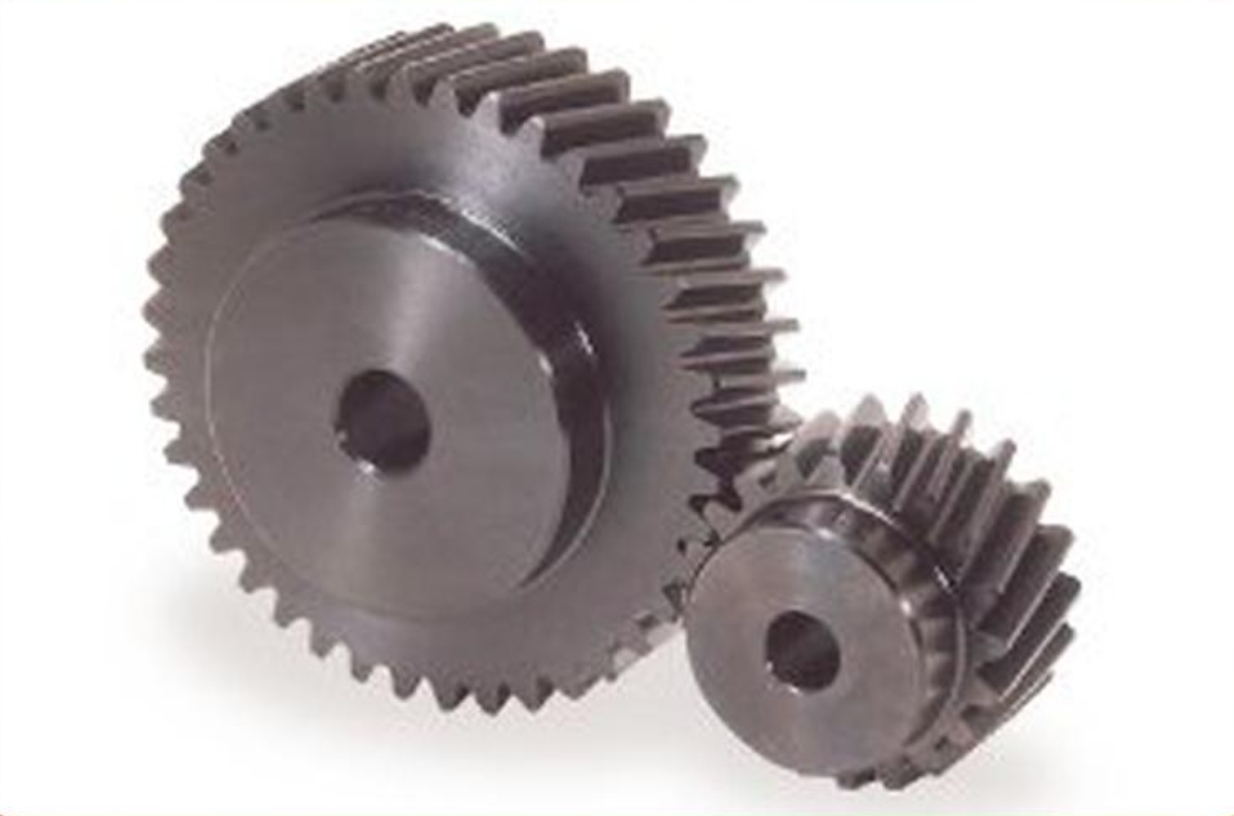
Factors Influencing Noise and Vibration
- Gear Design: The geometry of helical gear teeth, including helix angle, pressure angle, and module, plays a significant role in noise generation. Optimizing these parameters can reduce noise levels.
- Manufacturing Accuracy: Imperfections in the manufacturing process, such as tooth surface roughness, lead to vibrations and noise. Precision machining and finishing are essential.
- Material Properties: The choice of materials for helical gear affects their noise and vibration characteristics. High-quality materials with good damping properties can help reduce noise.
- Lubrication: Proper lubrication reduces friction and wear, which in turn lowers noise and vibration. The type and viscosity of the lubricant are critical factors.
- Assembly and Alignment: Misalignment of helical gear during assembly can cause uneven load distribution, leading to increased noise and vibration. Accurate alignment is necessary.
- Operational Conditions: Load variations, speed fluctuations, and environmental conditions can impact the noise and vibration levels of helical gear.
Strategies for Noise and Vibration Control
- Design Optimization: Using computer-aided design (CAD) and finite element analysis (FEA) to optimize helical gear geometry and tooth profile.
- Precision Manufacturing: Implementing advanced manufacturing techniques such as helical gear grinding and honing to achieve high surface finish and accuracy.
- Material Selection: Choosing materials with high strength, good wear resistance, and damping properties.
- Lubrication Management: Selecting appropriate lubricants and ensuring proper lubrication intervals and methods.
- Accurate Assembly: Ensuring precise alignment and assembly of helical gear to minimize misalignment and imbalance.
- Dynamic Balancing: Balancing helical gear components dynamically to reduce vibrations.
- Vibration Damping: Incorporating damping materials and isolators in helical gear housing and support structures.
Case Study: Implementation of Noise and Vibration Control
A manufacturing plant implemented a noise and vibration control program for their helical gear transmissions. The following measures were taken:
- Design Review: Optimized helical gear design using CAD and FEA tools.
- Material Upgrade: Switched to a higher-grade steel with better damping properties.
- Precision Machining: Improved manufacturing processes to reduce surface roughness.
- Enhanced Lubrication: Adopted synthetic lubricants with superior properties.
- Alignment Checks: Implemented regular alignment checks during maintenance.
The results were significant reductions in noise and vibration levels, leading to improved operational efficiency and reduced maintenance costs.
Table: Comparison of Noise and Vibration Levels Before and After Implementation
Measure | Before Implementation | After Implementation |
---|---|---|
Noise Level (dB) | 85 | 70 |
Vibration Level (mm/s) | 4.5 | 2.0 |
Maintenance Frequency | Monthly | Quarterly |
Operational Downtime | 10 hours/month | 3 hours/month |
Gear Lifespan (years) | 5 | 8 |
Conclusion
Effective noise and vibration control in helical gear transmissions requires a comprehensive approach, addressing design, manufacturing, material selection, lubrication, and maintenance. By implementing these strategies, industries can achieve quieter, more reliable, and efficient gear operations, ultimately enhancing productivity and reducing costs.