Abstract
This paper proposes a method for recognizing the damage fault of spiral bevel gears using modulation signal bispectrum (MSB) and convolutional neural network (CNN). The vibration acceleration signals are collected from spiral bevel gears under normal, minor damage, and major damage conditions. The modulation signal bispectra of these signals are calculated and used as input samples to train a CNN model. The experimental results show that the proposed method can effectively improve the recognition accuracy of spiral bevel gear damage faults, achieving an average recognition accuracy of 99.91%.
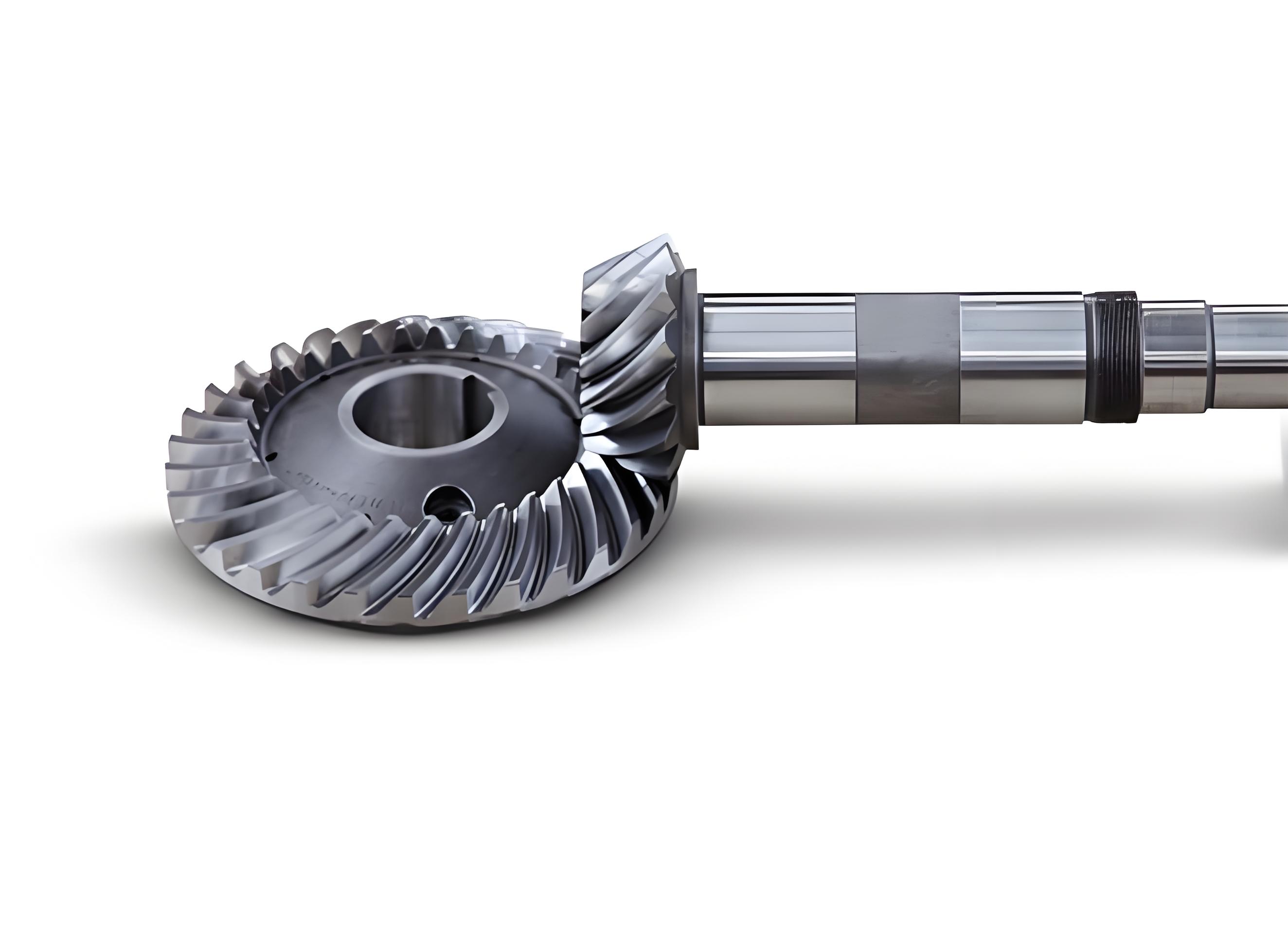
1. Introduction
Spiral bevel gears are widely used in various equipment such as ship propulsion systems, helicopters, aero-engines, and automotive transmission systems due to their advantages of smooth operation, large transmission ratio, high torque capacity, reliability, and compact structure. However, under long-term heavy-duty and variable load conditions, gear damage can occur, leading to vibration, reduced transmission performance, and even catastrophic failures. Therefore, accurate recognition of spiral bevel gear damage faults is essential for predictive maintenance and ensuring safe and stable operation.
The complexity of the meshing process and the harsh working environment of spiral bevel gears make their fault feature recognition challenging. Traditional fault diagnosis methods, such as vibration analysis based on time-domain or frequency-domain features, often struggle to extract meaningful features from noisy and nonlinear signals. Modulation signal bispectrum (MSB), as an advanced signal processing technique, demonstrates strong demodulation capability and noise suppression, making it suitable for fault diagnosis in rotating machinery. Convolutional neural networks (CNNs), on the other hand, have shown great potential in improving the accuracy and efficiency of fault diagnosis due to their strong data mining capabilities.
This paper combines MSB and CNN to develop a novel spiral bevel gear damage fault recognition method. MSB is used to extract features from the vibration signals, while CNN is employed to classify the extracted features and identify the fault conditions.
2. Theoretical Background
2.1 Modulation Signal Bispectrum (MSB)
MSB is an extension of the bispectrum, which is a higher-order statistical tool used to analyze nonlinear and non-Gaussian signals. MSB has been shown to be effective in extracting fault features from noisy signals, especially in rotating machinery applications.
Given a discrete-time vibration signal x(t), its Fourier transform Xf(ω) is defined as:
Xf(ω)=DFT[x(t)]=t=−∞∑∞x(t)e−j2πωt
The MSB of x(t) is given by:
textBMSfc(fx,fc)=E[Xfc+fxXfc−fxXfc∗Xfc∗]
where E[⋅] denotes the mathematical expectation, fc is the carrier frequency, fx is the modulation frequency, (fc+fx) is the upper sideband frequency, and (fc−fx) is the lower sideband frequency. The amplitude AMSfc(fx) and phase ϕMSfc,fx of MSB are:
textAMSfc(fx)=E[Xfc+fxXfc−fxXfc∗Xfc∗]
phiMSfc,fx=ϕfc+fx+ϕfc−fx−∣ϕfc∣−∣ϕfc∣
MSB can also be visualized as an image, where the axes represent the frequency components and the color intensity reflects the magnitude of the bispectrum. This visualization provides a useful representation for further analysis and classification using machine learning techniques.
2.2 Convolutional Neural Networks (CNNs)
CNNs are a type of deep learning model that have achieved remarkable success in image recognition, object detection, and other computer vision tasks. They excel at automatically extracting hierarchical features from raw input data through convolutional layers, pooling layers, and fully connected layers.
A typical CNN architecture consists of the following layers:
- Input Layer: Preprocesses the raw input data, such as image normalization.
- Convolutional Layers: Extract local features by applying convolutional filters and nonlinear activation functions.
- Pooling Layers: Reduce the dimensionality of the feature maps by downsampling, typically using max-pooling or average-pooling.
- Fully Connected Layers: Classify the extracted features and output the prediction results.
CNNs are well-suited for processing image-like inputs, such as the MSB images generated from vibration signals.
3. Proposed Methodology
The proposed method for recognizing spiral bevel gear damage faults combines MSB and CNN as follows:
- Collect Vibration Signals: Acquire vibration acceleration signals from spiral bevel gears under normal, minor damage, and major damage conditions using accelerometers.
- Preprocess and Segment Signals: Segment the collected signals into equal-length data segments and apply normalization.
- Calculate MSB Features: Compute the modulation signal bispectra of the preprocessed signal segments and convert them into images.
- Construct Training and Testing Datasets: Split the MSB images into training and testing sets.
- Train CNN Model: Design and train a CNN model using the training set of MSB images.
- Fault Recognition: Use the trained CNN model to classify the testing set of MSB images and evaluate the recognition accuracy.
3.1 Signal Acquisition and Preprocessing
Vibration signals were acquired using an accelerometer mounted on the input shaft of a spiral bevel gear test rig. The signals were sampled at 3.2 kHz with a rotating speed of 900 rpm. The acquired signals were then segmented into 1024-point segments and normalized.
3.2 MSB Feature Extraction
For each signal segment, the MSB was calculated and visualized as an image from a top-down perspective to avoid occlusion of features. The MSB images were resized to 128×128 pixels for compatibility with the CNN model.
3.3 CNN Model Design and Training
The CNN model architecture consisted of an input layer, three convolutional layers, two max-pooling layers, a flattening layer, two fully connected layers, and an output layer. The key parameters of the CNN model are summarized in Table 1.
Layer | Number of Filters/Nodes | Kernel Size | Stride | Activation Function |
---|---|---|---|---|
Input Layer | – | – | – | – |
Conv Layer 1 | 8 | 3×3 | 1 | ReLU |
Max-Pool 1 | – | 2×2 | 2 | – |
Conv Layer 2 | 16 | 3×3 | 1 | ReLU |
Max-Pool 2 | – | 2×2 | 2 | – |
Conv Layer 3 | 32 | 3×3 | 1 | ReLU |
Flatten Layer | – | – | – | – |
FC Layer 1 | 128 | – | – | ReLU |
FC Layer 2 | 3 (Number of Classes) | – | – | Softmax |
The model was trained using the Adam optimizer with a learning rate of 0.0001 for 90 epochs. Batch normalization was applied after each convolutional layer to accelerate convergence and improve stability. Dropout was used in the fully connected layers to prevent overfitting.
3.4 Fault Recognition and Evaluation
The trained CNN model was used to classify the testing set of MSB images into normal, minor damage, and major damage classes. The recognition accuracy was evaluated using confusion matrices and average recognition accuracy.
4. Experimental Results
4.1 MSB Feature Visualization
The MSB images generated from the vibration signals of spiral bevel gears under different damage conditions. The distinct patterns in the MSB images indicate that they contain useful information for fault recognition.
4.2 Fault Recognition Accuracy
Table 2 compares the fault recognition accuracy of the proposed MSB+CNN method with other methods, including vibration signal+CNN and MSB+SVM. The MSB+CNN method achieved the highest average recognition accuracy of 99.91%.
Method | Average Recognition Accuracy (%) | Training Time (s) |
---|---|---|
Vibration+CNN | 93.53 | 107 |
MSB+SVM | 99.42 | 2374 |
MSB+BP | 89.37 | 621 |
MSB+CNN | 99.91 | 97 |
4.3 Confusion Matrices
The confusion matrices for the MSB+CNN method and the vibration signal+CNN method. The MSB+CNN method exhibits higher diagonal values, indicating better classification performance.
5. Discussion
The experimental results demonstrate the effectiveness of the proposed MSB+CNN method for recognizing spiral bevel gear damage faults. The high recognition accuracy achieved by the MSB+CNN method can be attributed to several factors:
- Effective Feature Extraction: MSB effectively extracts fault features from noisy and nonlinear vibration signals, providing more discriminative input for the CNN model.
- Automatic Feature Learning: CNN automatically learns hierarchical features from the MSB images, eliminating the need for manual feature engineering.
- Strong Classification Capability: CNN’s ability to classify complex patterns makes it well-suited for fault diagnosis tasks.
Compared to traditional methods, the MSB+CNN method offers the following advantages:
- Higher Recognition Accuracy: The combination of MSB and CNN results in a higher recognition accuracy than using either technique alone.
- Faster Training Time: The MSB+CNN method has a shorter training time than some other machine learning methods, such as SVM.
- Better Generalization: The automatic feature learning capability of CNN enables the model to generalize better to unseen data.
6. Conclusion
This paper proposes a novel method for recognizing spiral bevel gear damage faults based on modulation signal bispectrum and convolutional neural network. The experimental results show that the proposed method achieves a high recognition accuracy of 99.91%, outperforming traditional methods. The MSB+CNN method effectively extracts fault features from noisy vibration signals and automatically learns to classify them, demonstrating its potential for practical applications in predictive maintenance of spiral bevel gears.