This comprehensive article delves into the intricate world of spur gear trains within complex machinery, exploring their simulation and optimization techniques. Spur gears play a vital role in power transmission systems, and optimizing their performance is crucial for enhancing the efficiency, reliability, and longevity of mechanical devices. By combining theoretical analysis, numerical simulations, and practical experiments, this study aims to provide in-depth insights and effective strategies for the design and improvement of spur gear trains.
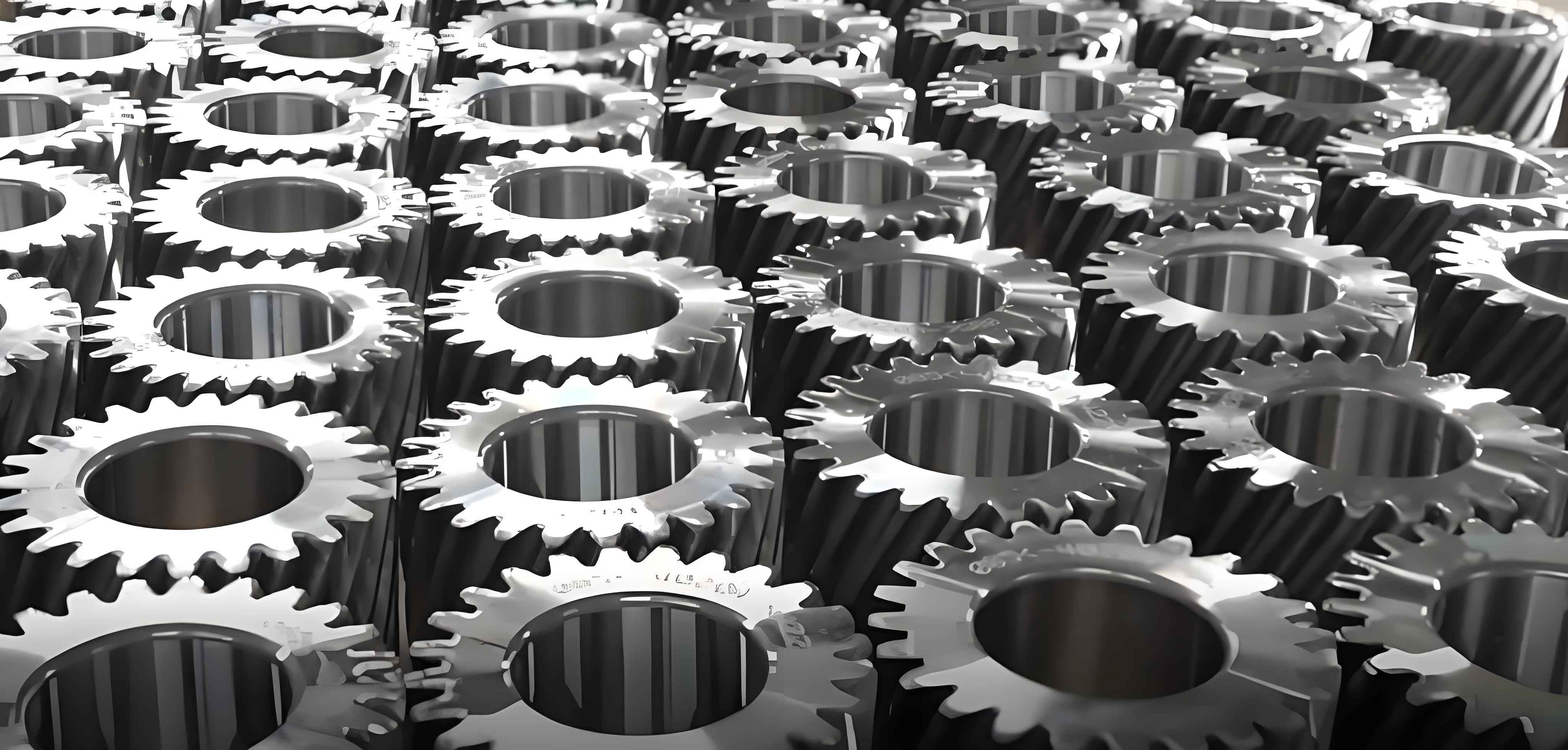
1. Introduction
Spur gears are one of the most common types of gears used in mechanical systems due to their simplicity, ease of manufacture, and wide range of applications. They are extensively employed in various industries such as automotive, aerospace, manufacturing, and robotics. In complex machinery, spur gear trains often operate under demanding conditions, requiring precise design and optimization to ensure smooth and efficient power transfer.
The simulation and optimization of spur gear trains involve multiple factors, including gear geometry, material properties, loading conditions, and lubrication. Understanding the interaction between these parameters is essential for achieving optimal performance and minimizing wear, noise, and vibration.
2. Spur Gear Geometry and Terminology
Before delving into the simulation and optimization aspects, it is crucial to have a clear understanding of the basic geometry and terminology of spur gears. A spur gear consists of a cylindrical body with teeth evenly spaced along the circumference. The key parameters that define a spur gear include the module, number of teeth, pitch diameter, pressure angle, and tooth profile.
The module (m) is the ratio of the pitch diameter (d) to the number of teeth (z), given by the equation m = d / z. The pressure angle (α) determines the shape and contact characteristics of the teeth. Common pressure angles include 20° and 25°.
The tooth profile of a spur gear is typically based on standard involute curves, which provide smooth meshing and uniform power transmission. The addendum and dedendum are the portions of the tooth above and below the pitch circle, respectively.
3. Dynamics of Spur Gear Trains
The dynamic behavior of spur gear trains is a complex phenomenon that influences their performance and reliability. When gears mesh, forces and torques are exchanged, resulting in vibrations, noise, and potential fatigue failure. The dynamic analysis of spur gear trains considers factors such as tooth meshing stiffness, backlash, damping, and inertia.
Tooth meshing stiffness is a key parameter that varies during the meshing cycle and depends on the tooth contact geometry and material properties. Backlash, which is the clearance between mating teeth, can cause impact and noise. Damping helps to dissipate energy and reduce vibrations.
4. Simulation Methods for Spur Gear Trains
Several simulation techniques are available for analyzing the behavior of spur gear trains. Finite element analysis (FEA) is widely used to model the stress, deformation, and contact mechanics of gears. In FEA, the gear geometry is discretized into a mesh of elements, and boundary conditions and loads are applied to simulate the meshing process.
Multibody dynamics simulations can also be employed to study the overall motion and dynamic response of the gear train system. These simulations take into account the interactions between gears, shafts, bearings, and other components.
5. Load Analysis and Stress Distribution
Accurate determination of the loads acting on spur gears is essential for predicting their stress distribution and fatigue life. Loads can be classified as static loads (such as transmitted torque) and dynamic loads (caused by vibrations and shock). The Hertzian contact theory is commonly used to calculate the contact stress between meshing teeth.
The stress distribution within a spur gear is not uniform and depends on the tooth profile and loading conditions. Peak stresses occur at the root of the teeth and the contact area. Fatigue analysis is often performed to assess the durability of gears under cyclic loading.
6. Optimization Objectives and Constraints
The optimization of spur gear trains aims to achieve specific performance objectives while satisfying various constraints. Common optimization objectives include minimizing weight, maximizing power transmission efficiency, reducing noise and vibration, and extending the fatigue life. Constraints may include gear size limitations, strength requirements, manufacturing tolerances, and cost considerations.
7. Optimization Approaches
Different optimization algorithms can be employed to optimize spur gear trains. Genetic algorithms, particle swarm optimization, and gradient-based methods are some commonly used techniques. These algorithms search the design space to find the optimal combination of parameters that meet the specified objectives and constraints.
In addition to parametric optimization, topological optimization can also be utilized to explore novel gear geometries that offer improved performance.
8. Effects of Lubrication and Surface Treatment
Lubrication plays a crucial role in reducing friction and wear between meshing gears. The type and properties of the lubricant, as well as the lubrication regime (boundary, mixed, or hydrodynamic), significantly affect the performance of spur gear trains.
Surface treatments such as case hardening, shot peening, and coating can enhance the surface hardness and fatigue resistance of gears, thereby improving their durability.
9. Experimental Validation and Case Studies
To validate the simulation results and optimization strategies, experimental studies are often conducted. Experiments can include gear tests on specialized rigs to measure forces, vibrations, noise, and temperature. Case studies of real-world applications demonstrate the effectiveness of the proposed simulation and optimization methods.
10. Future Trends and Challenges
The field of spur gear train simulation and optimization is constantly evolving. Emerging technologies such as additive manufacturing, advanced materials, and intelligent control systems present new opportunities and challenges. Future research may focus on developing more accurate simulation models, integrating multi-physics phenomena, and considering sustainability and reliability aspects.
Tables
Table 1: Key Parameters of Spur Gears
Parameter | Definition | Formula |
---|---|---|
Module (m) | Ratio of pitch diameter to number of teeth | m = d / z |
Pitch Diameter (d) | Diameter at which teeth are evenly spaced | d = m * z |
Pressure Angle (α) | Angle determining tooth contact characteristics | – |
Table 2: Common Materials for Spur Gears and Their Properties
Material | Strength | Hardness | Cost |
---|---|---|---|
Steel | High | Varies | Moderate |
Cast Iron | Moderate | Low | Low |
Aluminum | Low | Low | Low |
Lists
List 1: Factors Affecting the Dynamic Behavior of Spur Gear Trains
- Tooth meshing stiffness
- Backlash
- Damping
- Inertia
List 2: Optimization Constraints for Spur Gear Trains
- Gear size limitations
- Strength requirements
- Manufacturing tolerances
- Cost considerations